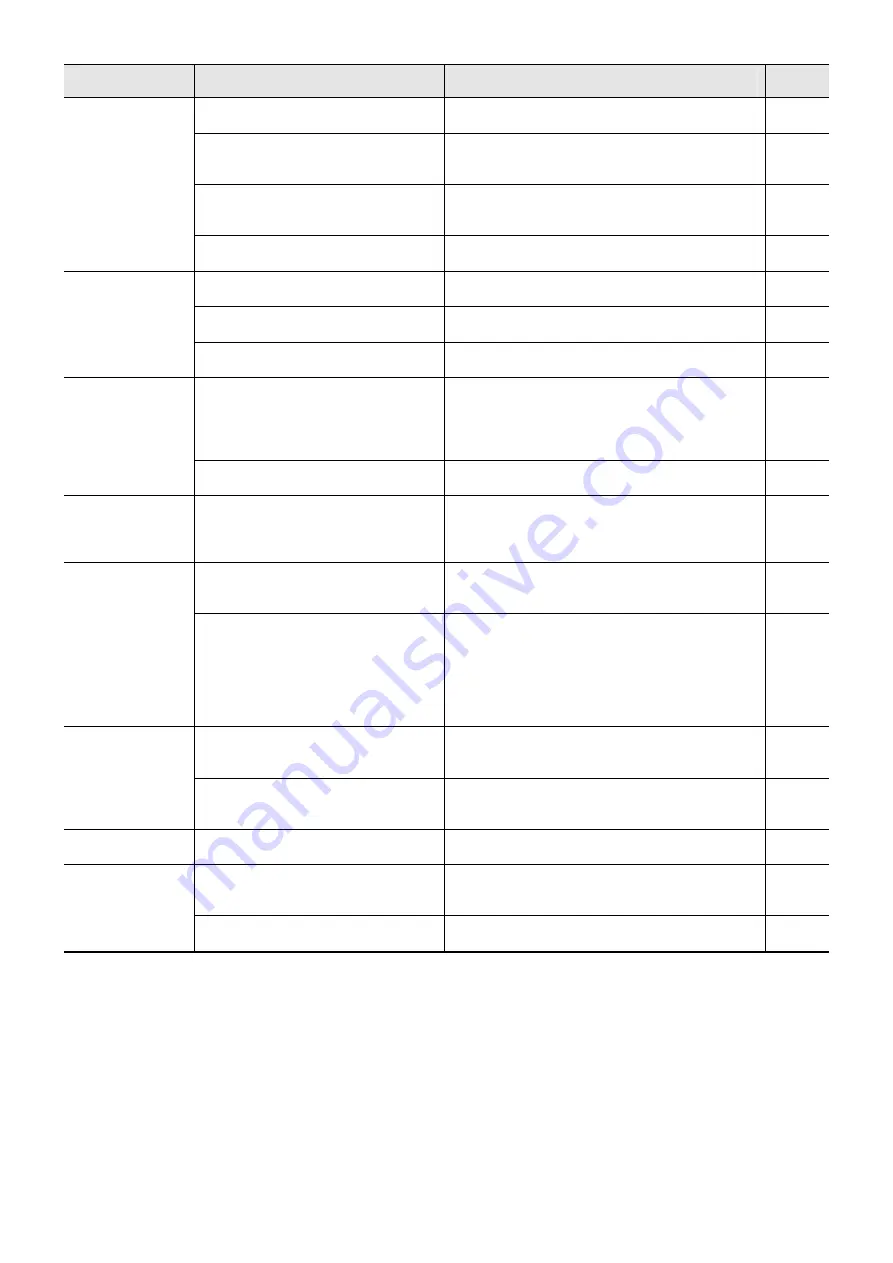
5-24
Symptom
Content of the likely cause
Countermeasures
Reference
Unable to run/set
from the optional
unit
(communication
unit).
The primary/secondary run command
selection (A002/A202) is incorrect.
Set the primary/secondary run command selection
(A002/A202) to “04: optional unit”.
The primary/secondary frequency
command selection (A001/A201) is
incorrect.
Set the primary/secondary frequency command
selection (A001/A201) to “04: optional unit”.
Incorrect address.
Check that the index/sub index (EtherCat) and
Class/Instance/Attribute (CompoNet/DeviceNet)
are correct.
Modbus mapping function is set.
Set the Modbus mapping function selection (P200)
to “00: standard Modbus address”.
Unable to connect
the CX-Drive.
CX-Drive version is incorrect.
Prepare Ver. 2.8 if connecting 3G3MX2 series V1
type.
The software number of the inverter is
inconsistent.
Match the CX-Drive to the software number of the
inverter to connect to.
The endian function of the Modbus
mapping function is set improperly.
Set Modbus mapping endian selection (P400) to
“00: big endian”.
Unable to set the
parameter from
CX-Drive.
The inverter is running.
Stop the inverter, and reset the settings after the
motor slows down and stops. If set to the mode
where changes are permitted while running (b031 =
10), some of the parameters can be changed while
running.
Modbus mapping function is set.
Set the Modbus mapping function selection (P200)
to “00: standard Modbus address”.
Overload
protection (E05)
occurs on brake
control.
Inverter is running in brake restrain
state.
Release the run command of the inverter in brake
restrain state. Overload protection may occur in DC
breaking.
Brake error (E36)
occurs on brake
control.
Brake control release current has not
been reached.
Either make the brake control release wait time
(b121) longer, or reduce the brake control release
current (b126).
Brake check signal is not being
inputted.
• Correct the wirings of the brake check signal
(44: BOK). If not in use, remove the brake check
signal from the multi function input setting.
• Correct the sequence so that the brake check
signal (44: BOK) is inputted after the brake
release.
• Replace the brake if it is damaged.
Load drops on
brake control.
Insufficient brake control release
current.
• Raise the brake control release current (b126).
• Set the control method (A044/A244) to “03:
sensor less vector control”.
The frequency to release/restrain the
brake is low.
Raise either the brake control release frequency
(b125), brake control restrain frequency (b127) or
the creep speed setting (P015).
PM motor rotates
on startup.
The motor magnetic pole position is
incorrect on startup.
Set the PM motor start method selection (H123) to
“01: default position estimation enabled”.
Overcurrent
protection (E03)
occurs when
starting with the
PM motor.
PM motor is out of step.
Raise the PM motor start current (H117).
Adjust according to the “PM motor mode
adjustment”.
Excessive load.
Reduce the load. Or make the acceleration time
longer.
Summary of Contents for MK0003
Page 2: ......
Page 8: ...0 6...
Page 12: ...1 4 2 DIMENSIONAL DRAWING OF OUTRIGGER WIDTH...
Page 17: ...1 9 4 WORKING RADIUS LIFTING HEIGHT...
Page 18: ...1 10 Working range diagram Outrigger extended to maximum Main boom 1 section...
Page 19: ...1 11 Working range diagram Outrigger extended to maximum Main boom 2 sections...
Page 20: ...1 12 Working range diagram Outrigger extended to maximum Main boom 2 5 sections...
Page 21: ...1 13 Working range diagram Outrigger extended to maximum Main boom 3 sections...
Page 22: ...1 14 Working range diagram Outrigger extended to minimum Main boom 1 section...
Page 23: ...1 15 Working range diagram Outrigger extended to minimum Main boom 2 sections...
Page 24: ...1 16 Working range diagram Outrigger extended to minimum Main boom 2 5 sections...
Page 25: ...1 17 Working range diagram Outrigger extended to minimum Main boom 3 sections...
Page 26: ...1 18 5 RATED TOTAL LOAD CHART...
Page 32: ...2 4...
Page 33: ...2 5 1 HYDRAULIC CIRCUIT DIAGRAM 200 1176600...
Page 34: ...2 6...
Page 35: ...2 7 2 HYDRAULIC PIPING DIAGRAM 2 1 CRANE ROTATING PART 200 1171800...
Page 41: ...2 13 2 2 CONTROL LINE A...
Page 43: ...2 15 2 3CONTROL LINE B Perform spiral winding on the entire perimeter of the hose of this part...
Page 45: ...2 17 2 4 TRAVEL LINE...
Page 47: ...2 19 2 5 OUTRIGGER LINE...
Page 49: ...2 21 2 6 PT LINE 102 1152000 4...
Page 69: ...2 41...
Page 70: ...2 42...
Page 71: ...2 43...
Page 76: ...2 48 4 8 ENGINE ACCESSORIES 102 1149200...
Page 90: ...2 62 7 2 INTERNAL STRUCTURE...
Page 120: ...2 92 Part B Writing method for wire number Two places...
Page 123: ...2 95 Figure 1 Index point Figure 2 Connection diagram...
Page 166: ...2 138 15 4 APPEARANCE OF OUTRIGGER ON REAR LEFT SIDE 200 2167300...
Page 173: ...2 145 17 ELECTRIC CIRCUIT DIAGRAM 200 1176500 01...
Page 174: ...2 146 18 ELECTRIC SYSTEM 18 1 1 WIRE HARNESS OF MACHINE BODY 1 200 1172200 1...
Page 176: ...2 148 18 1 2 WIRE HARNESS OF MACHINE BODY 2 200 1172200 2...
Page 179: ...2 151 19 CONTROL ASSEMBLY 19 1 CONTROLLER 1 TTC60 Pin arrangement...
Page 180: ...2 152 TTC60 I O...
Page 181: ...2 153 2 TTC36X Pin arrangement...
Page 182: ...2 154 TTC36X lower part I O...
Page 209: ...2 181 19 2 5 LIST OF CONTROLLER INPUT MONITORING...
Page 210: ...2 182 19 2 6 LIST OF CONTROLLER ANALOG INPUT OUTPUT MONITORING...
Page 245: ...3 9 1 2 3 ANGLE METER 360 S200M3297000...
Page 274: ...3 38...
Page 293: ...4 19 8 SERVICE LOCATIONS...
Page 294: ...4 20...
Page 296: ...5 2 1 ELECTRICAL MOTOR UNIT ASSEMBLY Unit weight 180 kg...
Page 324: ...5 30...
Page 325: ...5 31 4 ELECTRICAL DIAGRAM S200M3122000 01...
Page 326: ...5 32 S200M3122000 02...
Page 336: ...6 8 1 3 2 INTERNAL STRUCTURE OF WINCH MOTOR...
Page 345: ...6 17 4 WORKING RADIUS LIFTING HEIGHT OF ONE FALL WINCH...
Page 348: ......