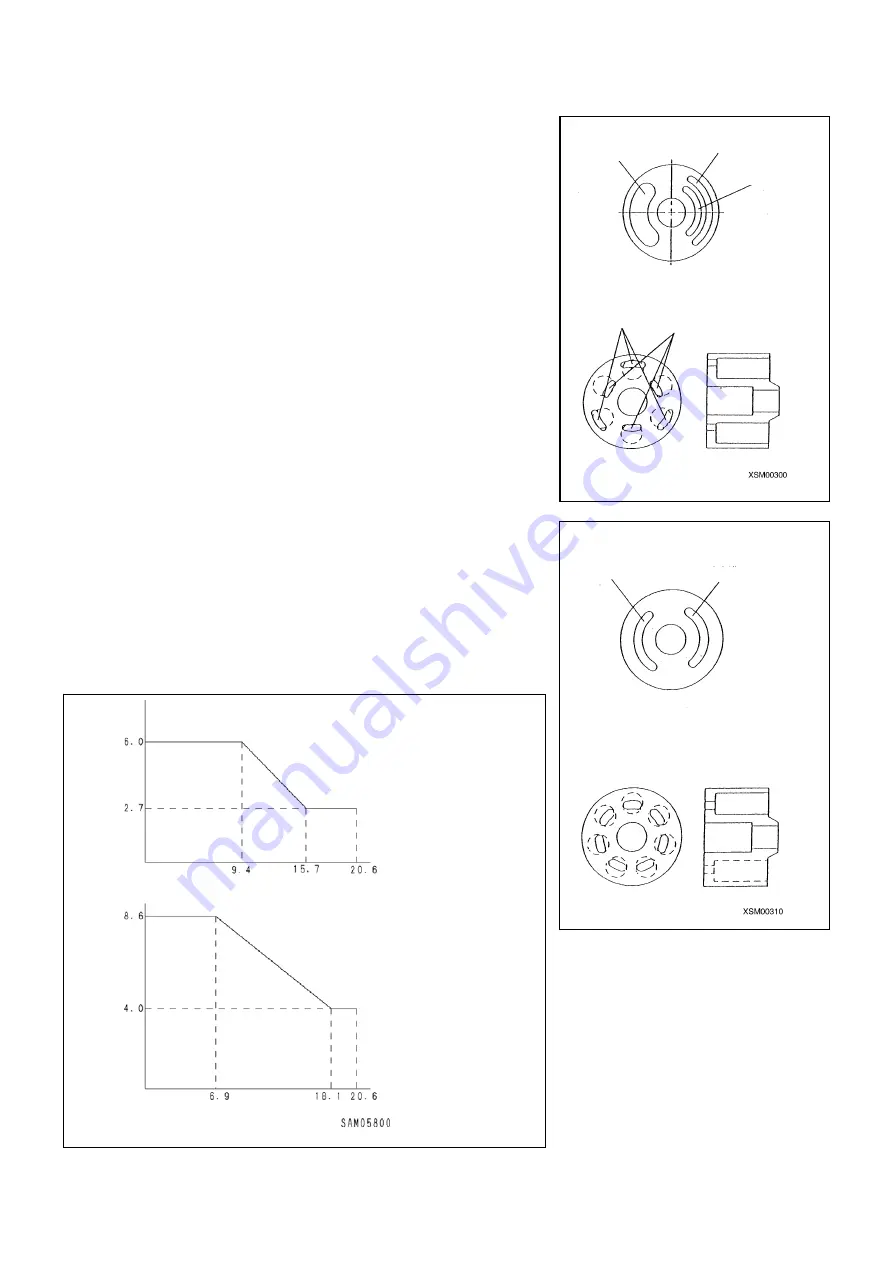
2-54
5.4 OPERATING PRINCIPLES
1. Overview
This hydraulic pump consists of such a mechanism that allows this
compact and light-weight pump to perform pumping actions equivalent to
two pumps while occupying a space required for a single pump only.
To utilize the engine power effectively, this pump has been designed to
have a fixed horsepower control characteristic for suppressing the
discharge rate in commensurate with the increase of pump load.
Accordingly, this pump is equipped with a mechanism to decrease its
discharge rate in such a way that when pump discharge pressures P1 and
P2 increase to raise the resultant force in combination with the piston
force to allow the swash plate to overcome the spring tension so that it tilts
around the rocking center of the rocking pin.
2. Structure and actions
In a swash plate type variable piston pump, in order for the pump to be
equipped with the pumping function of two pumps each having an equal
capacity that are accommodated in the pump case for a single pump, an
even number of pistons are incorporated.
While a conventional valve plate has, as shown in the bottom right figure,
a single port each for the intake and discharge is provided, this system
comprises a pair of intake port and discharge port each on the outside
(P1) and the inside (P2).
Every other pump box in row of the cylinder barrel opens either toward the
outside (P1) or inside (P2).
While the intake occurs in similar way for both inside and outside, the
discharge of inside and outside performs different delivery actions.
Since this system has an even number of pistons, each having the same
diameter, being mounted on the common pitch circle with others, and
slides on the common swash plate, the discharge rates from outside (P1)
and inside (P2) are equal.
Further, since the sole swash plate allows the discharge rate of both P1
and P2 plates to vary equally with the variation of tilt angle of swash plate
in its variable control action, no difference in discharge rate is brought
about.
Conventional swash plate type
piston pump
Operating principle
Intake port
Discharge port P
1
Discharge port P
2
(a) Valve plate
Discharge port P
1
and opening
Discharge port P
2
and opening
Intake port
Discharge port
(a) Valve plate
(b) Cylinder barrel
Engine pump
Item number: 353S57600000
Electric pump
Item number: 329S33800001
Discharge pressure P1 = P2 (MPa)
Discharge pressure P1 = P2 (MPa)
Di
sc
harge ra
te
q1 =
q2 (
cc/
rev
)
Di
sc
harge ra
te
q1 =
q2 (
cc/
rev
)
(b) Cylinder barrel
Summary of Contents for MK0003
Page 2: ......
Page 8: ...0 6...
Page 12: ...1 4 2 DIMENSIONAL DRAWING OF OUTRIGGER WIDTH...
Page 17: ...1 9 4 WORKING RADIUS LIFTING HEIGHT...
Page 18: ...1 10 Working range diagram Outrigger extended to maximum Main boom 1 section...
Page 19: ...1 11 Working range diagram Outrigger extended to maximum Main boom 2 sections...
Page 20: ...1 12 Working range diagram Outrigger extended to maximum Main boom 2 5 sections...
Page 21: ...1 13 Working range diagram Outrigger extended to maximum Main boom 3 sections...
Page 22: ...1 14 Working range diagram Outrigger extended to minimum Main boom 1 section...
Page 23: ...1 15 Working range diagram Outrigger extended to minimum Main boom 2 sections...
Page 24: ...1 16 Working range diagram Outrigger extended to minimum Main boom 2 5 sections...
Page 25: ...1 17 Working range diagram Outrigger extended to minimum Main boom 3 sections...
Page 26: ...1 18 5 RATED TOTAL LOAD CHART...
Page 32: ...2 4...
Page 33: ...2 5 1 HYDRAULIC CIRCUIT DIAGRAM 200 1176600...
Page 34: ...2 6...
Page 35: ...2 7 2 HYDRAULIC PIPING DIAGRAM 2 1 CRANE ROTATING PART 200 1171800...
Page 41: ...2 13 2 2 CONTROL LINE A...
Page 43: ...2 15 2 3CONTROL LINE B Perform spiral winding on the entire perimeter of the hose of this part...
Page 45: ...2 17 2 4 TRAVEL LINE...
Page 47: ...2 19 2 5 OUTRIGGER LINE...
Page 49: ...2 21 2 6 PT LINE 102 1152000 4...
Page 69: ...2 41...
Page 70: ...2 42...
Page 71: ...2 43...
Page 76: ...2 48 4 8 ENGINE ACCESSORIES 102 1149200...
Page 90: ...2 62 7 2 INTERNAL STRUCTURE...
Page 120: ...2 92 Part B Writing method for wire number Two places...
Page 123: ...2 95 Figure 1 Index point Figure 2 Connection diagram...
Page 166: ...2 138 15 4 APPEARANCE OF OUTRIGGER ON REAR LEFT SIDE 200 2167300...
Page 173: ...2 145 17 ELECTRIC CIRCUIT DIAGRAM 200 1176500 01...
Page 174: ...2 146 18 ELECTRIC SYSTEM 18 1 1 WIRE HARNESS OF MACHINE BODY 1 200 1172200 1...
Page 176: ...2 148 18 1 2 WIRE HARNESS OF MACHINE BODY 2 200 1172200 2...
Page 179: ...2 151 19 CONTROL ASSEMBLY 19 1 CONTROLLER 1 TTC60 Pin arrangement...
Page 180: ...2 152 TTC60 I O...
Page 181: ...2 153 2 TTC36X Pin arrangement...
Page 182: ...2 154 TTC36X lower part I O...
Page 209: ...2 181 19 2 5 LIST OF CONTROLLER INPUT MONITORING...
Page 210: ...2 182 19 2 6 LIST OF CONTROLLER ANALOG INPUT OUTPUT MONITORING...
Page 245: ...3 9 1 2 3 ANGLE METER 360 S200M3297000...
Page 274: ...3 38...
Page 293: ...4 19 8 SERVICE LOCATIONS...
Page 294: ...4 20...
Page 296: ...5 2 1 ELECTRICAL MOTOR UNIT ASSEMBLY Unit weight 180 kg...
Page 324: ...5 30...
Page 325: ...5 31 4 ELECTRICAL DIAGRAM S200M3122000 01...
Page 326: ...5 32 S200M3122000 02...
Page 336: ...6 8 1 3 2 INTERNAL STRUCTURE OF WINCH MOTOR...
Page 345: ...6 17 4 WORKING RADIUS LIFTING HEIGHT OF ONE FALL WINCH...
Page 348: ......