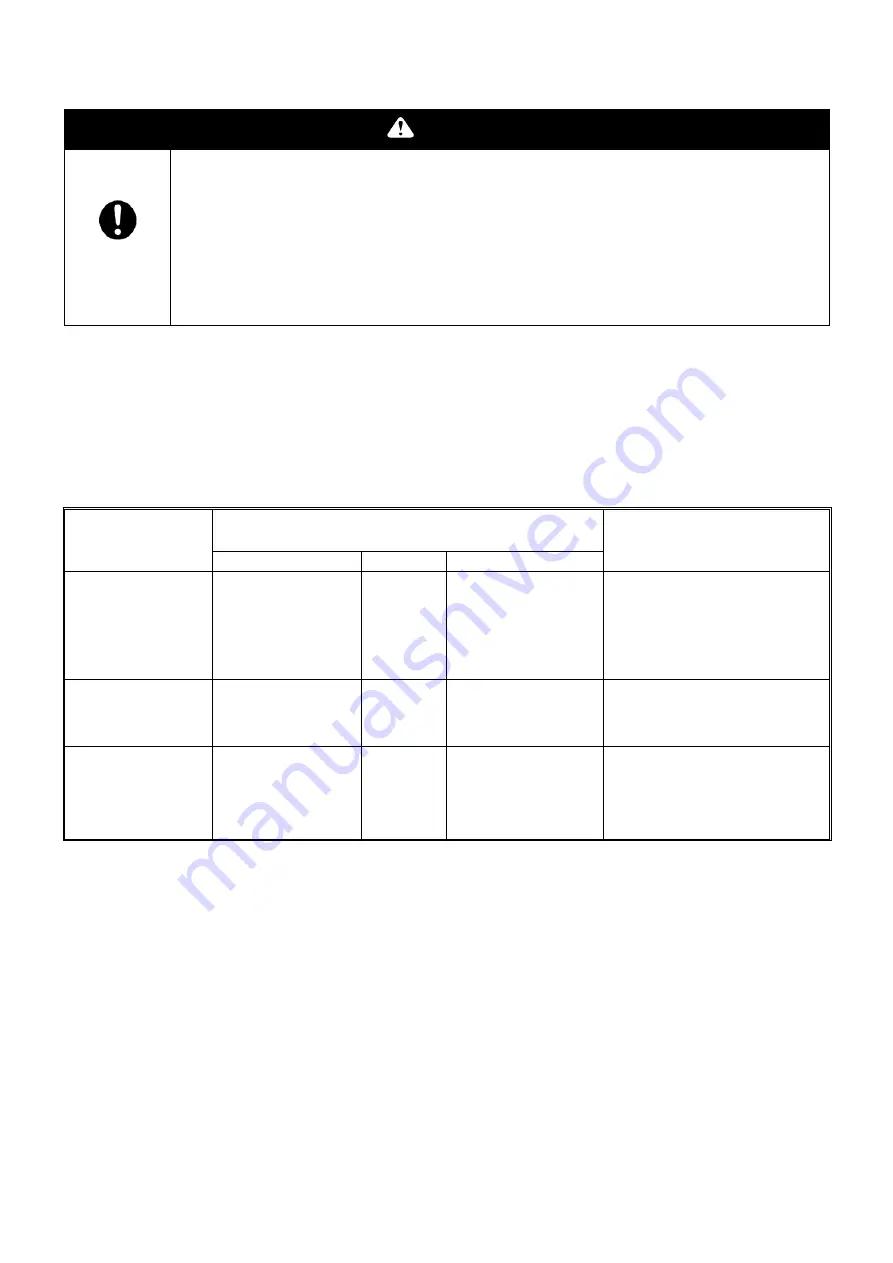
5-25
2.8 MAINTENANCE
AND
INSPECTION
DANGER
Compulsory
- Perform daily check.
If maintenance and inspections are not performed, failures and damage cannot be found, which
may result in accidents.
- Perform the following steps before starting the inspection.
(1) Cutoff “OFF” the input power.
(2) Check that the charge lamp is off after 10 minutes has elapsed.
(3) Use a tester that is capable of measuring DC high voltage (more than DC 800V), and check
that the DC main circuit voltage (between PA–PC) is under 45V.
If this step is not performed before inspection, it may lead to an electrical shock.
Perform daily inspections and periodical inspections to avoid failure due to aging, life of parts and impact from
the environment such as temperature, humidity, dust, and vibration.
2.8.1 DAIRY INSPECTION
Electrical parts are weak against heat. In order to increase the life of the unit, place in an environment where dust
does not cumulate, and where the ambient temperature is low, and well ventilated.
The purpose of the daily inspection is to maintain the environment, and to discover operational abnormalities before
accidents occur by comparing operation data records.
Inspection target
Inspection procedure
Criterion
Check item
Cycle
Inspection method
1. Room environment
1) Dust, temperature,
gas
As required
1) Visual inspection,
thermometer,
olfaction
1) Improve areas of concern.
2) Dripping of water
and other liquid
As required
2) Visual inspection
2) Pay attention to scratches.
3) Room temperature
As required
3) Thermometer
3) Maximum 60°C
2. Component and
parts
1) Vibration, noise
As required
Feeling of the box
external
If abnormal, open the door, and
inspect the trance, reactor,
contactor, relay and cooling fan.
Stop the operation if necessary.
3. Operation data
(Output side)
1) Load current
As required
1) Moving iron type AC
amperometer
Must be within rated.
No large changes shall be observed
compared to the normal data.
2) Voltage (*)
As required
2) Rectifier type AC
amperometer
3) Temperature
As required
3) Thermometer
(*) The voltage may vary depending on the measuring equipment. The same tester or amperometer should be used for inspections,
and the indicated value shall be recorded.
■
Check point
1. Whether there are any abnormalities in the installation environment
2. Whether there are any abnormalities in the cooling system
3. Whether there is any abnormal vibration or sound
4. Whether there is any abnormal heat or discolorization
5. Whether there is any abnormal smell
6. Whether there are any abnormal vibration, sound or temperature in the motor
7. Whether there are any cumulation of debris (conductive material)
Summary of Contents for MK0003
Page 2: ......
Page 8: ...0 6...
Page 12: ...1 4 2 DIMENSIONAL DRAWING OF OUTRIGGER WIDTH...
Page 17: ...1 9 4 WORKING RADIUS LIFTING HEIGHT...
Page 18: ...1 10 Working range diagram Outrigger extended to maximum Main boom 1 section...
Page 19: ...1 11 Working range diagram Outrigger extended to maximum Main boom 2 sections...
Page 20: ...1 12 Working range diagram Outrigger extended to maximum Main boom 2 5 sections...
Page 21: ...1 13 Working range diagram Outrigger extended to maximum Main boom 3 sections...
Page 22: ...1 14 Working range diagram Outrigger extended to minimum Main boom 1 section...
Page 23: ...1 15 Working range diagram Outrigger extended to minimum Main boom 2 sections...
Page 24: ...1 16 Working range diagram Outrigger extended to minimum Main boom 2 5 sections...
Page 25: ...1 17 Working range diagram Outrigger extended to minimum Main boom 3 sections...
Page 26: ...1 18 5 RATED TOTAL LOAD CHART...
Page 32: ...2 4...
Page 33: ...2 5 1 HYDRAULIC CIRCUIT DIAGRAM 200 1176600...
Page 34: ...2 6...
Page 35: ...2 7 2 HYDRAULIC PIPING DIAGRAM 2 1 CRANE ROTATING PART 200 1171800...
Page 41: ...2 13 2 2 CONTROL LINE A...
Page 43: ...2 15 2 3CONTROL LINE B Perform spiral winding on the entire perimeter of the hose of this part...
Page 45: ...2 17 2 4 TRAVEL LINE...
Page 47: ...2 19 2 5 OUTRIGGER LINE...
Page 49: ...2 21 2 6 PT LINE 102 1152000 4...
Page 69: ...2 41...
Page 70: ...2 42...
Page 71: ...2 43...
Page 76: ...2 48 4 8 ENGINE ACCESSORIES 102 1149200...
Page 90: ...2 62 7 2 INTERNAL STRUCTURE...
Page 120: ...2 92 Part B Writing method for wire number Two places...
Page 123: ...2 95 Figure 1 Index point Figure 2 Connection diagram...
Page 166: ...2 138 15 4 APPEARANCE OF OUTRIGGER ON REAR LEFT SIDE 200 2167300...
Page 173: ...2 145 17 ELECTRIC CIRCUIT DIAGRAM 200 1176500 01...
Page 174: ...2 146 18 ELECTRIC SYSTEM 18 1 1 WIRE HARNESS OF MACHINE BODY 1 200 1172200 1...
Page 176: ...2 148 18 1 2 WIRE HARNESS OF MACHINE BODY 2 200 1172200 2...
Page 179: ...2 151 19 CONTROL ASSEMBLY 19 1 CONTROLLER 1 TTC60 Pin arrangement...
Page 180: ...2 152 TTC60 I O...
Page 181: ...2 153 2 TTC36X Pin arrangement...
Page 182: ...2 154 TTC36X lower part I O...
Page 209: ...2 181 19 2 5 LIST OF CONTROLLER INPUT MONITORING...
Page 210: ...2 182 19 2 6 LIST OF CONTROLLER ANALOG INPUT OUTPUT MONITORING...
Page 245: ...3 9 1 2 3 ANGLE METER 360 S200M3297000...
Page 274: ...3 38...
Page 293: ...4 19 8 SERVICE LOCATIONS...
Page 294: ...4 20...
Page 296: ...5 2 1 ELECTRICAL MOTOR UNIT ASSEMBLY Unit weight 180 kg...
Page 324: ...5 30...
Page 325: ...5 31 4 ELECTRICAL DIAGRAM S200M3122000 01...
Page 326: ...5 32 S200M3122000 02...
Page 336: ...6 8 1 3 2 INTERNAL STRUCTURE OF WINCH MOTOR...
Page 345: ...6 17 4 WORKING RADIUS LIFTING HEIGHT OF ONE FALL WINCH...
Page 348: ......