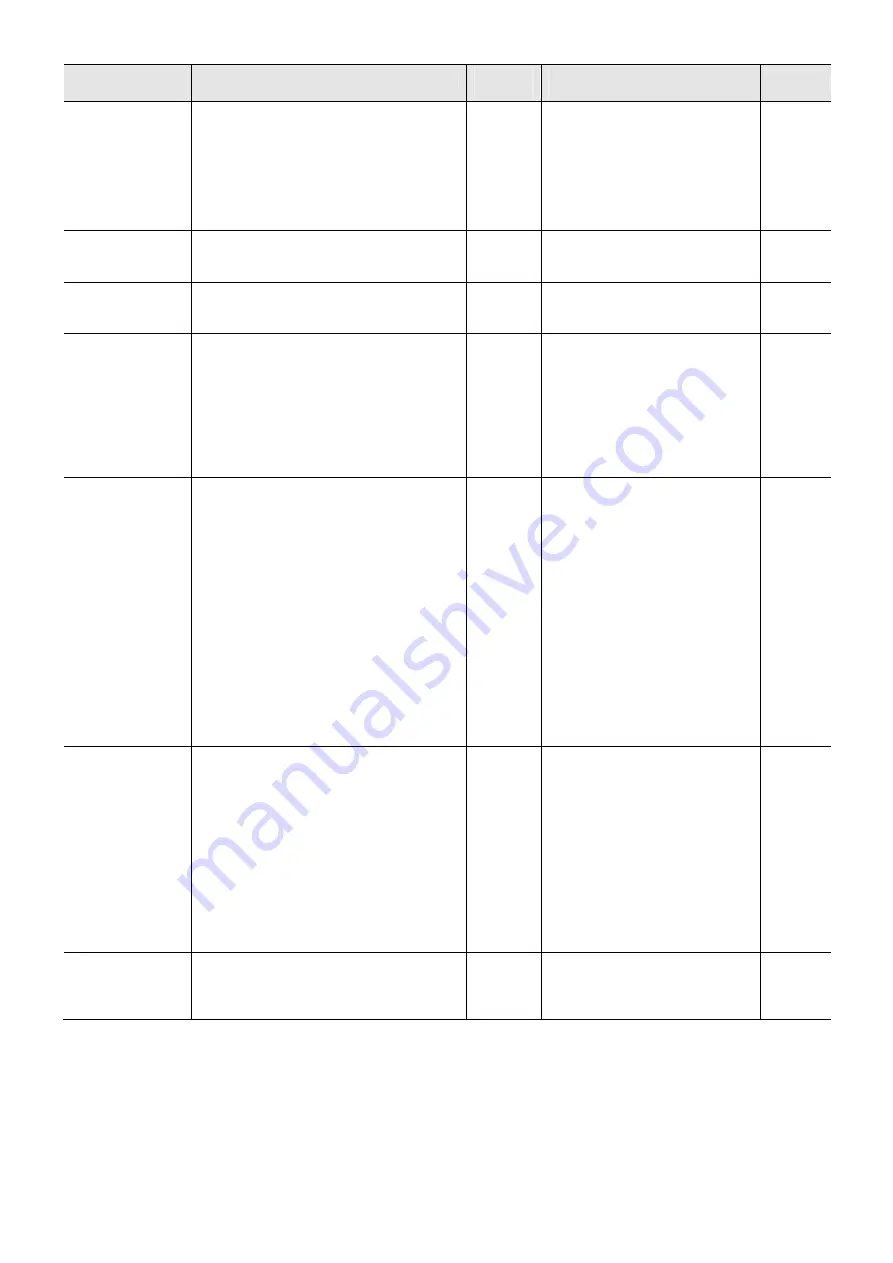
5-18
Name
Content
Alarm
code
Check content and
countermeasures
Reference
Modbus
communication
fault
Trips if timeout occurs when the setting for
the communication error selection is trip
(C076 = 00).
E41.
Is the communication speed
correct?
• Check the settings.
Is the wiring distance appropriate?
• Check the communication
cables.
Are there any breakages?
• Check the wirings.
Driveprogramming
fault
• Program fault (E43.
– E45.
)
• User trip (E50.
– E59.
)
E43.
–
E59.
Refer to “DriveProgramming
Users Manual (SBCE-369)” for
details.
Optional unit fault
Error reported from optional units.
E60.
–
E68.
Refer to the manuals of the
optional units for details.
Optional unit
timeout
Trips when timeouts occur in the
communication between the inverter and
the optional units.
E69.
Optional units are disconnected.
• Check if the fixing screws are
loose, and that the optional
units are properly attached
with the inverter.
Optional units are damaged.
• If the optional units are
properly attached, they may be
damaged.
Encoder breakage Trips if the status, where the motor rotation
detected by the encoder is below the start
frequency (b082), continues consecutively
for more than the encoder breakage
detection time (P077
≠
0), when the output
frequency is above the creep speed setting
(P015).
E80.
Breakage or bad connection of the
encoder wirings.
• Check the encoder wirings.
The actual motor rotation is below
the start frequency (b082) for
more than the breakage detection
time (P077).
• Parameter adjustment
Make P077 longer, and P015
higher.
This also occurs when the motor
rotation is below the start
frequency during the simple
positioning.
• Parameter adjustment
Make P077 longer, and P015
higher.
Overspeed
Trips when the motor rotation is over
maximum frequency × overspeed fault
detection level (P026
≠
0).
E81.
Determined in the speed detection
of the encoder.
Breakage or bad connection of the
encoder wirings
• Check the encoder wirings.
Inconsistency in the encoder
pulse value.
• Check the encoder pulse
value. P011
The actual motor rotation is over
the fault detection level.
• Adjust the overspeed fault
detection level P026.
Positioning control
range trip
Trips when the current position exceeds the
specified position range (P072, P073) in the
simple positioning control.
E83.
Check the current position.
• Check the parameter (P072,
P073).
• Check the origin point.
Summary of Contents for MK0003
Page 2: ......
Page 8: ...0 6...
Page 12: ...1 4 2 DIMENSIONAL DRAWING OF OUTRIGGER WIDTH...
Page 17: ...1 9 4 WORKING RADIUS LIFTING HEIGHT...
Page 18: ...1 10 Working range diagram Outrigger extended to maximum Main boom 1 section...
Page 19: ...1 11 Working range diagram Outrigger extended to maximum Main boom 2 sections...
Page 20: ...1 12 Working range diagram Outrigger extended to maximum Main boom 2 5 sections...
Page 21: ...1 13 Working range diagram Outrigger extended to maximum Main boom 3 sections...
Page 22: ...1 14 Working range diagram Outrigger extended to minimum Main boom 1 section...
Page 23: ...1 15 Working range diagram Outrigger extended to minimum Main boom 2 sections...
Page 24: ...1 16 Working range diagram Outrigger extended to minimum Main boom 2 5 sections...
Page 25: ...1 17 Working range diagram Outrigger extended to minimum Main boom 3 sections...
Page 26: ...1 18 5 RATED TOTAL LOAD CHART...
Page 32: ...2 4...
Page 33: ...2 5 1 HYDRAULIC CIRCUIT DIAGRAM 200 1176600...
Page 34: ...2 6...
Page 35: ...2 7 2 HYDRAULIC PIPING DIAGRAM 2 1 CRANE ROTATING PART 200 1171800...
Page 41: ...2 13 2 2 CONTROL LINE A...
Page 43: ...2 15 2 3CONTROL LINE B Perform spiral winding on the entire perimeter of the hose of this part...
Page 45: ...2 17 2 4 TRAVEL LINE...
Page 47: ...2 19 2 5 OUTRIGGER LINE...
Page 49: ...2 21 2 6 PT LINE 102 1152000 4...
Page 69: ...2 41...
Page 70: ...2 42...
Page 71: ...2 43...
Page 76: ...2 48 4 8 ENGINE ACCESSORIES 102 1149200...
Page 90: ...2 62 7 2 INTERNAL STRUCTURE...
Page 120: ...2 92 Part B Writing method for wire number Two places...
Page 123: ...2 95 Figure 1 Index point Figure 2 Connection diagram...
Page 166: ...2 138 15 4 APPEARANCE OF OUTRIGGER ON REAR LEFT SIDE 200 2167300...
Page 173: ...2 145 17 ELECTRIC CIRCUIT DIAGRAM 200 1176500 01...
Page 174: ...2 146 18 ELECTRIC SYSTEM 18 1 1 WIRE HARNESS OF MACHINE BODY 1 200 1172200 1...
Page 176: ...2 148 18 1 2 WIRE HARNESS OF MACHINE BODY 2 200 1172200 2...
Page 179: ...2 151 19 CONTROL ASSEMBLY 19 1 CONTROLLER 1 TTC60 Pin arrangement...
Page 180: ...2 152 TTC60 I O...
Page 181: ...2 153 2 TTC36X Pin arrangement...
Page 182: ...2 154 TTC36X lower part I O...
Page 209: ...2 181 19 2 5 LIST OF CONTROLLER INPUT MONITORING...
Page 210: ...2 182 19 2 6 LIST OF CONTROLLER ANALOG INPUT OUTPUT MONITORING...
Page 245: ...3 9 1 2 3 ANGLE METER 360 S200M3297000...
Page 274: ...3 38...
Page 293: ...4 19 8 SERVICE LOCATIONS...
Page 294: ...4 20...
Page 296: ...5 2 1 ELECTRICAL MOTOR UNIT ASSEMBLY Unit weight 180 kg...
Page 324: ...5 30...
Page 325: ...5 31 4 ELECTRICAL DIAGRAM S200M3122000 01...
Page 326: ...5 32 S200M3122000 02...
Page 336: ...6 8 1 3 2 INTERNAL STRUCTURE OF WINCH MOTOR...
Page 345: ...6 17 4 WORKING RADIUS LIFTING HEIGHT OF ONE FALL WINCH...
Page 348: ......