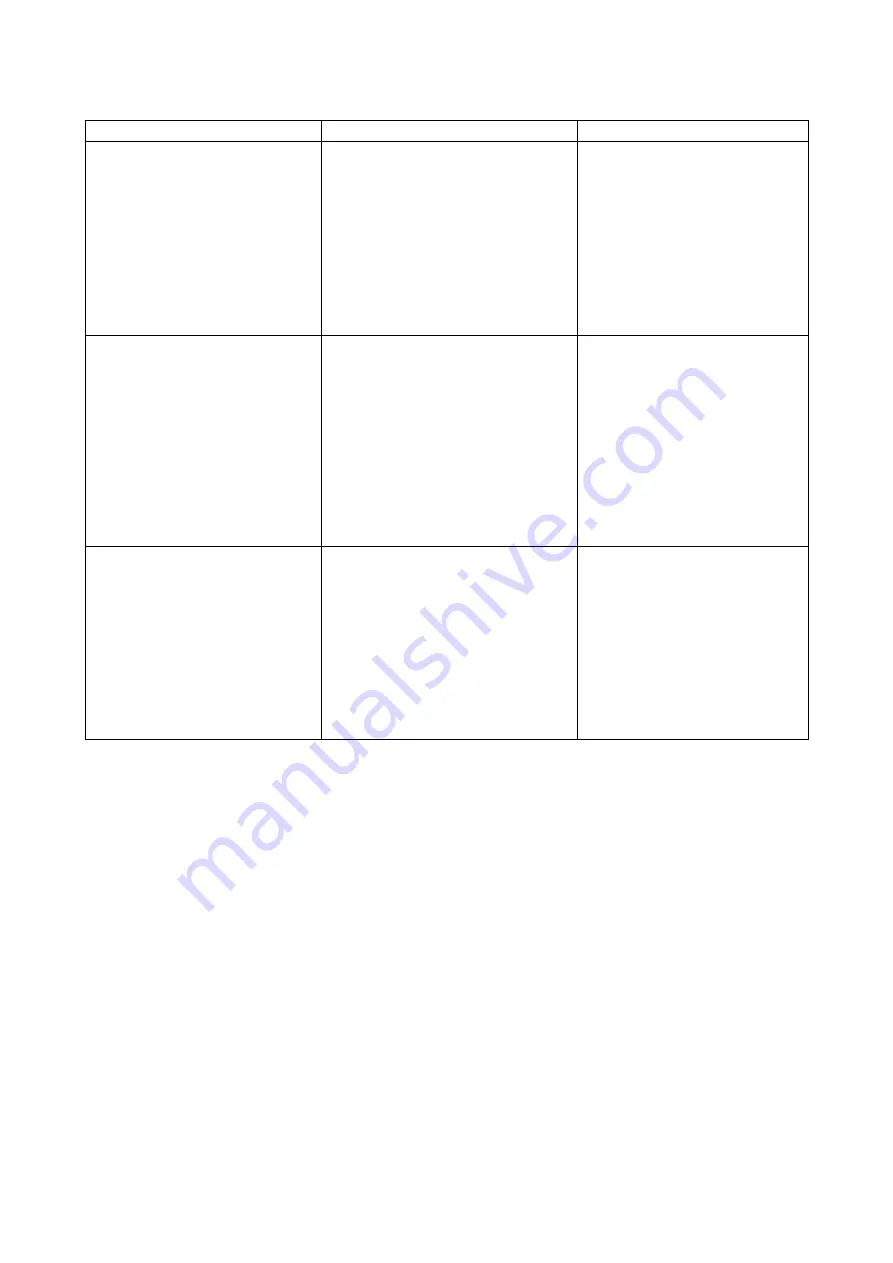
6-10
1.3.3 FAILURE CAUSE AND COUNTERMEASURE
●
Trouble of winch motor
Symptom Cause Remedy
A. There are abnormal noise and
vibration.
1. Air remains in the circuit and
motor.
2. Cavitation
(occurrence of negative
pressure)
• Completely bleed air from the
circuit. When the motor
generates negative pressure,
the air in the case is sucked.
Therefore, air may not bled
completely. Inspect the drain
piping.
• Restudy the hydraulic circuit
and take measures to prevent
the occurrence of negative
pressure.
B. Normal rotational speed
cannot be achieved.
3. Insufficient flow rate of oil
4. Overheat, increase in leak
amount due to inappropriate
viscosity of hydraulic oil
5. Failure in the motor
• Study the supply circuit such
as the pump circuit and leak
from the relief valve and
eliminate the cause.
• Eliminate the cause.
• Replace the motor. (Check an
outside drain amount of the
motor. If the drain amount is
normal, there is often other
cause.)
C. Normal torque cannot be
achieved.
6. Normal pressure is not
generated due to an error in the
circuit on the motor inlet side.
7. Abnormally high pressure is
generated in the circuit on the
motor outlet side.
8. Increase in leak amount due to
overheat
9. Failure in the motor
• Study the supply circuit such
as the pump circuit and relief
valve and eliminate the cause.
• Study the return side circuit
and eliminate the cause. For
example, clogging of circuits,
clogging of the return filter or
reverse installation
• Eliminate the cause.
• Replace the motor.
* In general, inspection of an outside drain amount is very effective for trouble shooting of the motor. Empirically, if
the outside drain amount is normal, the motor has no abnormality in many cases.
1.3.4 PRECAUTIONS IN WINCH MOTOR
1. Gear oil change timing
(1) First change (first change after operation start) : 500 hours
(2) Second time onward
: Every 1000 hours or yearly
However, if gear oil decreased for some reason, check the cause, take measures and replenish gear oil.
Gear oil change quantity: 0.75L
Summary of Contents for MK0003
Page 2: ......
Page 8: ...0 6...
Page 12: ...1 4 2 DIMENSIONAL DRAWING OF OUTRIGGER WIDTH...
Page 17: ...1 9 4 WORKING RADIUS LIFTING HEIGHT...
Page 18: ...1 10 Working range diagram Outrigger extended to maximum Main boom 1 section...
Page 19: ...1 11 Working range diagram Outrigger extended to maximum Main boom 2 sections...
Page 20: ...1 12 Working range diagram Outrigger extended to maximum Main boom 2 5 sections...
Page 21: ...1 13 Working range diagram Outrigger extended to maximum Main boom 3 sections...
Page 22: ...1 14 Working range diagram Outrigger extended to minimum Main boom 1 section...
Page 23: ...1 15 Working range diagram Outrigger extended to minimum Main boom 2 sections...
Page 24: ...1 16 Working range diagram Outrigger extended to minimum Main boom 2 5 sections...
Page 25: ...1 17 Working range diagram Outrigger extended to minimum Main boom 3 sections...
Page 26: ...1 18 5 RATED TOTAL LOAD CHART...
Page 32: ...2 4...
Page 33: ...2 5 1 HYDRAULIC CIRCUIT DIAGRAM 200 1176600...
Page 34: ...2 6...
Page 35: ...2 7 2 HYDRAULIC PIPING DIAGRAM 2 1 CRANE ROTATING PART 200 1171800...
Page 41: ...2 13 2 2 CONTROL LINE A...
Page 43: ...2 15 2 3CONTROL LINE B Perform spiral winding on the entire perimeter of the hose of this part...
Page 45: ...2 17 2 4 TRAVEL LINE...
Page 47: ...2 19 2 5 OUTRIGGER LINE...
Page 49: ...2 21 2 6 PT LINE 102 1152000 4...
Page 69: ...2 41...
Page 70: ...2 42...
Page 71: ...2 43...
Page 76: ...2 48 4 8 ENGINE ACCESSORIES 102 1149200...
Page 90: ...2 62 7 2 INTERNAL STRUCTURE...
Page 120: ...2 92 Part B Writing method for wire number Two places...
Page 123: ...2 95 Figure 1 Index point Figure 2 Connection diagram...
Page 166: ...2 138 15 4 APPEARANCE OF OUTRIGGER ON REAR LEFT SIDE 200 2167300...
Page 173: ...2 145 17 ELECTRIC CIRCUIT DIAGRAM 200 1176500 01...
Page 174: ...2 146 18 ELECTRIC SYSTEM 18 1 1 WIRE HARNESS OF MACHINE BODY 1 200 1172200 1...
Page 176: ...2 148 18 1 2 WIRE HARNESS OF MACHINE BODY 2 200 1172200 2...
Page 179: ...2 151 19 CONTROL ASSEMBLY 19 1 CONTROLLER 1 TTC60 Pin arrangement...
Page 180: ...2 152 TTC60 I O...
Page 181: ...2 153 2 TTC36X Pin arrangement...
Page 182: ...2 154 TTC36X lower part I O...
Page 209: ...2 181 19 2 5 LIST OF CONTROLLER INPUT MONITORING...
Page 210: ...2 182 19 2 6 LIST OF CONTROLLER ANALOG INPUT OUTPUT MONITORING...
Page 245: ...3 9 1 2 3 ANGLE METER 360 S200M3297000...
Page 274: ...3 38...
Page 293: ...4 19 8 SERVICE LOCATIONS...
Page 294: ...4 20...
Page 296: ...5 2 1 ELECTRICAL MOTOR UNIT ASSEMBLY Unit weight 180 kg...
Page 324: ...5 30...
Page 325: ...5 31 4 ELECTRICAL DIAGRAM S200M3122000 01...
Page 326: ...5 32 S200M3122000 02...
Page 336: ...6 8 1 3 2 INTERNAL STRUCTURE OF WINCH MOTOR...
Page 345: ...6 17 4 WORKING RADIUS LIFTING HEIGHT OF ONE FALL WINCH...
Page 348: ......