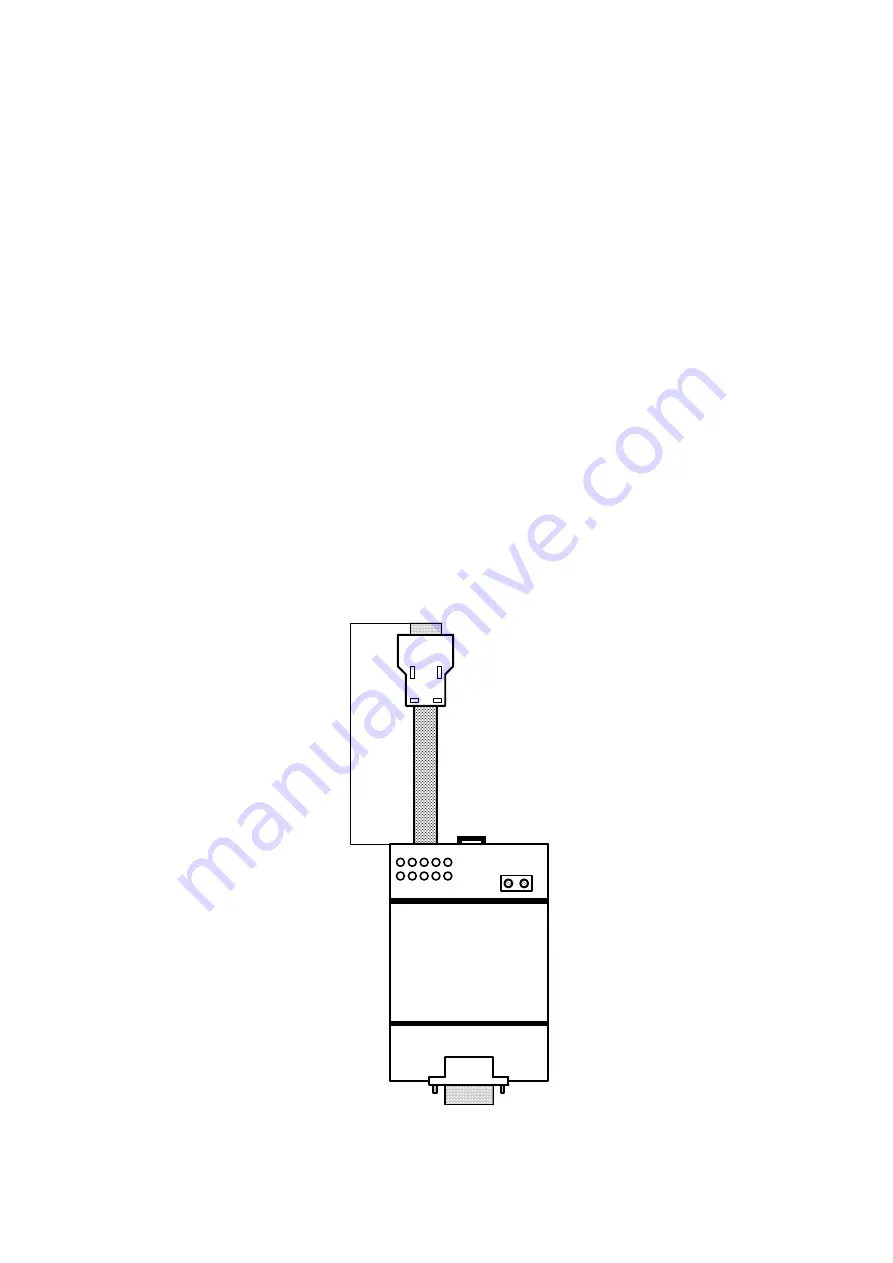
—————— TPD32-EV ——————
80
4.7 DIGITAL ENCODER INTERFACE DEII
4.7.1 Description
The option card DEII has been projected to adapt, to separate galvanically and to connect a digital encoder to
the input XE1 of the converters TPD32-EV regulations boards. As standard, this input is arranged for the con
-
nection of an analog encoder.
The card DEII will be fixed externally to the drive by the mounting rail DIN EN 50 022-35. The input female
connector
XS1
must be connected to the digital encoder using a 9-pole male connector, through a shielded cable,
Tasker c/186 (6 x 2 x 0.22) with a maximal length of 150 m.
Male output connector XS2 with 1.5 m shielded cable must be connected to the 9-pin connector fitted on the
TPD32-EV control card. The input voltage can be 15V...24V (HTL) or 5V (TTL), depending on whether the
encoder to be connected is type HTL or TTL. When the voltage connected to terVenc and 0Venc is
switched on, the HTL or TTL LED will light up. If the encoder has HTL outputs, switch S1-S2-S3 must be
positioned on HTL side (default configuration); on the opposite side if the encoder has a TTL output. If switch
S1-S2-S3 is positioned on TTL side, vVenc is also connected to pin 9 of XS1, in addition to pin 2.
S4 jumper is used to cut out the channel C (no impulse) from the test of encoder loss. S4 closed = canal C in
-
cluded, S4 open = canal C cut out. The EL LED lights up to signal the absence of at least one encoder signal.
The function that checks the absence of encoder signals works correctly only with encoders with complementary
outputs. It does NOT work with single-ended encoder drivers.
The jumper SH is mounted on condition of standard delivery; it must be cut only in case of the shield side en
-
coder is connected to the chassis of the motor, to avoid the forming a ground ring.
For converter operation with the DEII card it is necessary to set the jumper S5, S6 on the regulation board in
position A.
1
3
5
7
9
4
2
6
8
SH
XS1
+V
enc
0V
enc
Cable
Lengt
h
=
1.5m
DEII
XS2
Figure 4.7.1.1: DEII card
Summary of Contents for TPD32-EV-...-2B
Page 1: ... Instruction manual Industrial Application DC drives TPD32 EV ...
Page 372: ... TPD32 EV 372 9 BLOCK DIAGRAM 9 1 CONTROL BLOCK DIAGRAMS ...
Page 373: ... Instruction manual 373 ...
Page 374: ... TPD32 EV 374 ...
Page 375: ... Instruction manual 375 ...
Page 376: ... TPD32 EV 376 ...
Page 377: ... Instruction manual 377 ...
Page 378: ... TPD32 EV 378 ...
Page 379: ... Instruction manual 379 ...
Page 380: ... TPD32 EV 380 ...
Page 381: ... Instruction manual 381 ...
Page 382: ... TPD32 EV 382 ...
Page 383: ... Instruction manual 383 ...
Page 384: ... TPD32 EV 384 ...
Page 385: ... Instruction manual 385 ...
Page 386: ... TPD32 EV 386 ...
Page 387: ... Instruction manual 387 ...
Page 388: ... TPD32 EV 388 ...
Page 389: ... Instruction manual 389 ...
Page 390: ... TPD32 EV 390 ...
Page 391: ... Instruction manual 391 ...
Page 392: ... TPD32 EV 392 ...
Page 393: ... Instruction manual 393 ...
Page 394: ... TPD32 EV 394 ...
Page 395: ... Instruction manual 395 ...
Page 396: ... TPD32 EV 396 ...
Page 397: ... Instruction manual 397 ...
Page 398: ... TPD32 EV 398 ...
Page 399: ... Instruction manual 399 ...
Page 400: ... TPD32 EV 400 ...
Page 401: ... Instruction manual 401 ...
Page 402: ... TPD32 EV 402 ...
Page 501: ... Instruction manual 501 APPENDIX 3 ACCESSORIES A3 1 EAM Adapter Kit EAM1579 EAM1580 ...
Page 503: ......