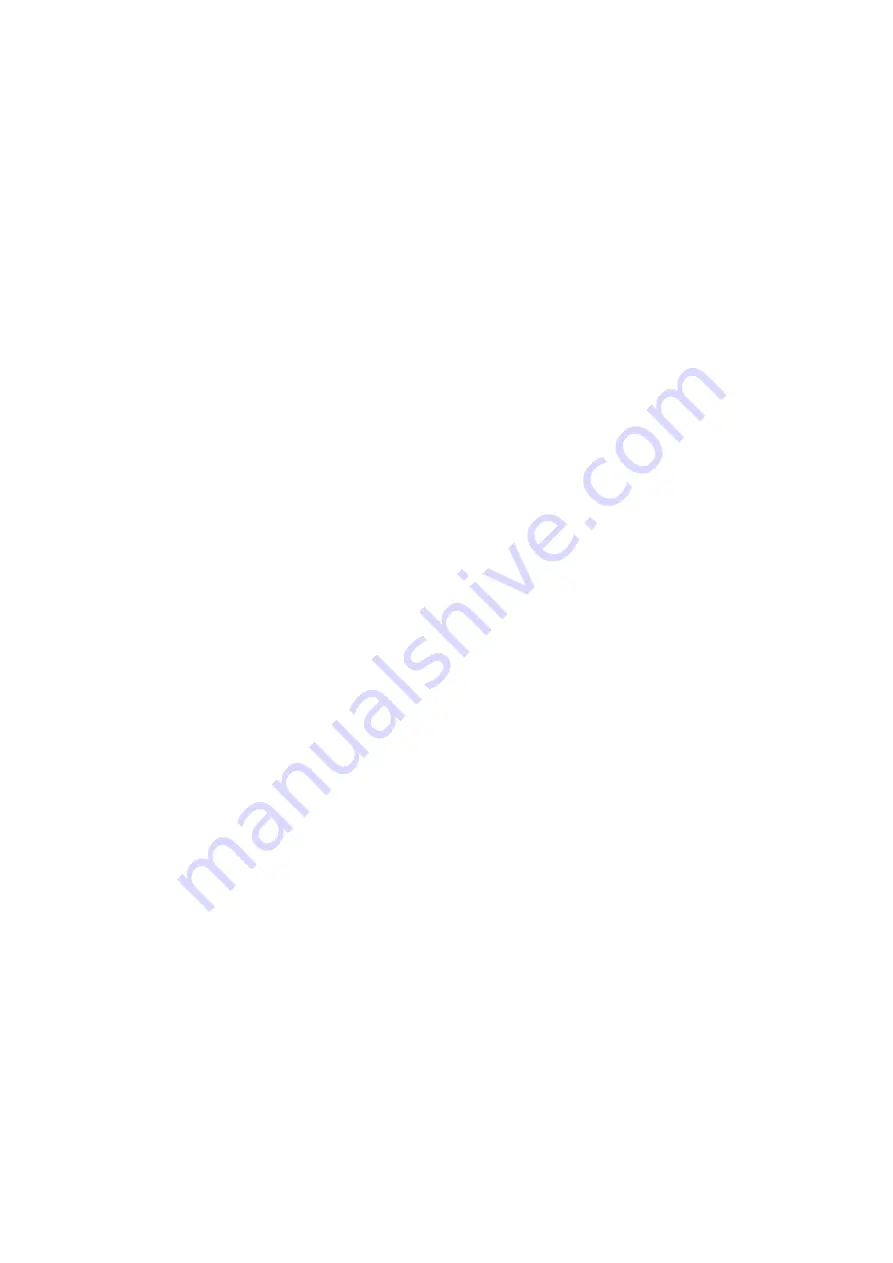
—————— Instruction manual ——————
117
5.3 COMMISSIONING
W
arning
!
The safety instructions, danger warnings and technical data in Section 1 and 2 of this manual
must be observed!
D
efinitions
:
Positive speed
is clockwise rotation seen from the motor shaft end side.
Negative Speed
is counter-clockwise rotation seen from the motor shaft end side.
Positive torque
is torque in clockwise directionseen from the motor shaft end side.
Negative torque
is torque in counter-clockwise direction seen from the motor shaft end side.
5.3.1 Setting jumpers and switch
The hardware configuration set via the jumpers and switches on the R-TPD32 regulator card must be adapted
to the application at hand and checked
before switching on the device
.
- Analog inputs 1/2/3
Voltage input 0... 10V
Jumper S9/S10/S11 = OFF
Current voltage 0...20 mA / 4...20 mA
Jumper S9/S10/S11 = ON
Mixed possible configuration
- Adaptation for the speed feedback type
Sinusoidal Encoder
Jumper S5/S6 in position A
Digital Encoder
Jumper S5/S6 any position
Analog tachometer generator
Jumper S5/S6 in position B
Armature reaction
Jumper S5/S6 any position
- Adaptation for the digital encoder voltage
Voltage = 5 V
Jumper S21/S22/S23 = ON
Voltage = 15...30 V
Jumper S21/S22/S23 = OFF
- Control of a digital encoder connected to the connector XE2
Channel C controlled
Jumper S20 = ON
Channel C not controlled
Jumper S20 = OFF
- Adaptation of the max voltage using a tachometer generator:
22.7 / 45.4 / 90.7 / 181.6 / 302.9 V,
depending on the dip switch S4 setting (see chapter 4.4.3)
- Serial interface RS485
On the first and last drop of a line:
Jumper S12 / S13 = ON
On the other converters
Jumper S12 / S13 = OFF
- RS485 serial interface
- divided from the regulation
Jumper S18 / S19 in position OFF
(An external 5 V power supply is needed
on the PINs 5 and 9) see section 4.5.2
- with a common potential 0 V of the regulation
Jumper S18 / S19 in position ON
(Internal power supply)
For further information see section 4.4, “Regulation section”.
Summary of Contents for TPD32-EV-...-2B
Page 1: ... Instruction manual Industrial Application DC drives TPD32 EV ...
Page 372: ... TPD32 EV 372 9 BLOCK DIAGRAM 9 1 CONTROL BLOCK DIAGRAMS ...
Page 373: ... Instruction manual 373 ...
Page 374: ... TPD32 EV 374 ...
Page 375: ... Instruction manual 375 ...
Page 376: ... TPD32 EV 376 ...
Page 377: ... Instruction manual 377 ...
Page 378: ... TPD32 EV 378 ...
Page 379: ... Instruction manual 379 ...
Page 380: ... TPD32 EV 380 ...
Page 381: ... Instruction manual 381 ...
Page 382: ... TPD32 EV 382 ...
Page 383: ... Instruction manual 383 ...
Page 384: ... TPD32 EV 384 ...
Page 385: ... Instruction manual 385 ...
Page 386: ... TPD32 EV 386 ...
Page 387: ... Instruction manual 387 ...
Page 388: ... TPD32 EV 388 ...
Page 389: ... Instruction manual 389 ...
Page 390: ... TPD32 EV 390 ...
Page 391: ... Instruction manual 391 ...
Page 392: ... TPD32 EV 392 ...
Page 393: ... Instruction manual 393 ...
Page 394: ... TPD32 EV 394 ...
Page 395: ... Instruction manual 395 ...
Page 396: ... TPD32 EV 396 ...
Page 397: ... Instruction manual 397 ...
Page 398: ... TPD32 EV 398 ...
Page 399: ... Instruction manual 399 ...
Page 400: ... TPD32 EV 400 ...
Page 401: ... Instruction manual 401 ...
Page 402: ... TPD32 EV 402 ...
Page 501: ... Instruction manual 501 APPENDIX 3 ACCESSORIES A3 1 EAM Adapter Kit EAM1579 EAM1580 ...
Page 503: ......