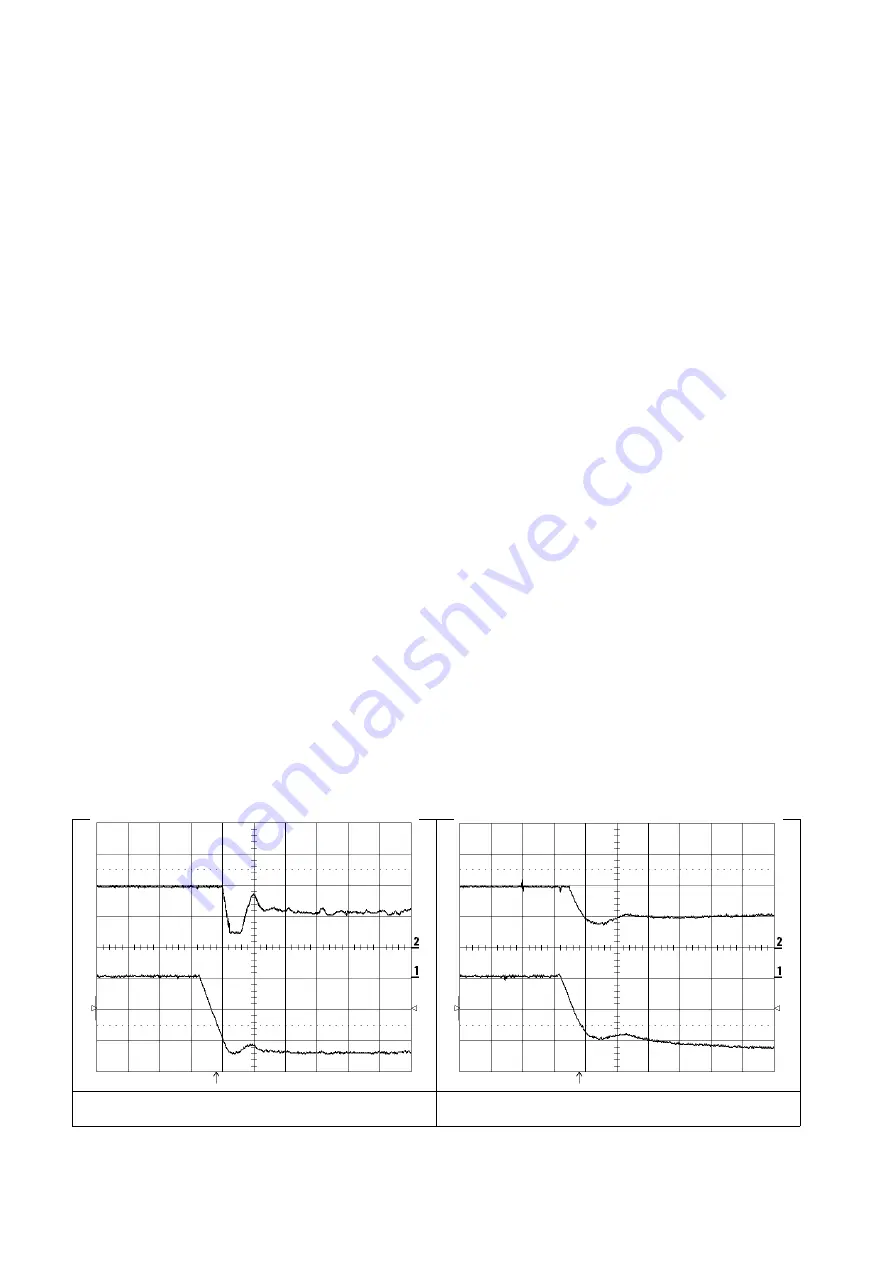
—————— TPD32-EV ——————
130
Voltage regulator in the field converter
n
ote
!
In the most of the cases the DC motors with an independent excitation operate with a direct
field (
Flux reg mode=Constant current
). In this case it is not necessary to optimize the
regulator of the armature voltage.
When a Voltage control occurs, the voltage regulator keeps the armature voltage at a constant level. The most
difficult moment for this regulator is the beginning of the Voltage control, because due to the saturation of the
motor field, the flux variation requires quicker changes of the field current.
Tune the regulator in order to have small changes of the armature voltage.
n
ote
!
All the other converter regulators must be set before the optimization of the voltage regulator.
- Drive disabled = no voltage on terminal 12
- Choose the following settings for the Test generator :
-
Gen access
=
Ramp ref
-
Gen frequency
=
0.2 Hz
-
Gen amplitude
=
10 %
-
Gen offset
=
according to the changing point from the armature regulation
to the field one. Example:
Motor max speed
= 2000 rpm,
the Voltage control starts at 1500 rpm.
Gen offset
= 75 %
- Measure the field current and the armature voltage on an analog output. The “Flux current” and the “Output
voltage” variables must be set on two different analog outputs (see Programming “Inputs/Outputs).
- Enable the drive and give the Start command (voltage on the terminals 12 and 13)
- Check the armature voltage. After a possible short jump, the voltage should remain constant. See figures
5.3.6.8 ... 5.3.6.10. In the REG PARAMETER /... menu, it is possible to change the P and I section with
the
Voltage P
and
Voltage I
parameters.
- Stop and disable the drive.
- Gen access = Not connected
- Save the settings.
Figure 5.3.6.8: Above: Flux; Below: Output voltage. After a speed change the
field current (Flux) has some jumps. Voltage P = 10%, Voltage I = 80%.
Figure 5.3.6.9: Above: Flux; Below: Output voltage. The gain is too low. The
armature voltage increases. Voltage P = 3%, Voltage I = 5%.
Summary of Contents for TPD32-EV-...-2B
Page 1: ... Instruction manual Industrial Application DC drives TPD32 EV ...
Page 372: ... TPD32 EV 372 9 BLOCK DIAGRAM 9 1 CONTROL BLOCK DIAGRAMS ...
Page 373: ... Instruction manual 373 ...
Page 374: ... TPD32 EV 374 ...
Page 375: ... Instruction manual 375 ...
Page 376: ... TPD32 EV 376 ...
Page 377: ... Instruction manual 377 ...
Page 378: ... TPD32 EV 378 ...
Page 379: ... Instruction manual 379 ...
Page 380: ... TPD32 EV 380 ...
Page 381: ... Instruction manual 381 ...
Page 382: ... TPD32 EV 382 ...
Page 383: ... Instruction manual 383 ...
Page 384: ... TPD32 EV 384 ...
Page 385: ... Instruction manual 385 ...
Page 386: ... TPD32 EV 386 ...
Page 387: ... Instruction manual 387 ...
Page 388: ... TPD32 EV 388 ...
Page 389: ... Instruction manual 389 ...
Page 390: ... TPD32 EV 390 ...
Page 391: ... Instruction manual 391 ...
Page 392: ... TPD32 EV 392 ...
Page 393: ... Instruction manual 393 ...
Page 394: ... TPD32 EV 394 ...
Page 395: ... Instruction manual 395 ...
Page 396: ... TPD32 EV 396 ...
Page 397: ... Instruction manual 397 ...
Page 398: ... TPD32 EV 398 ...
Page 399: ... Instruction manual 399 ...
Page 400: ... TPD32 EV 400 ...
Page 401: ... Instruction manual 401 ...
Page 402: ... TPD32 EV 402 ...
Page 501: ... Instruction manual 501 APPENDIX 3 ACCESSORIES A3 1 EAM Adapter Kit EAM1579 EAM1580 ...
Page 503: ......