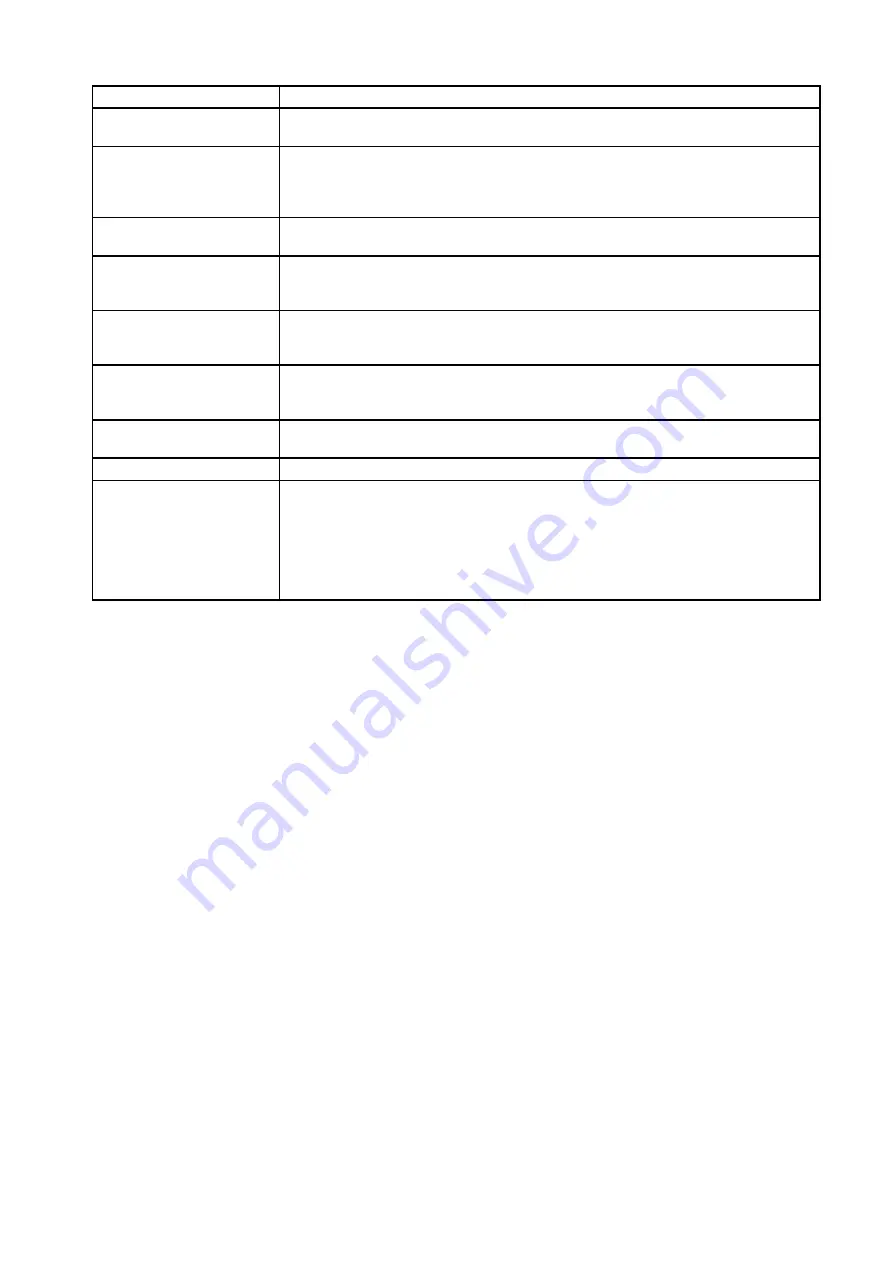
—————— Instruction manual ——————
371
FAILURE
POSSIBLE CAUSES
The speed during acceleration
with max. current is not linear
• Reduce the
Speed I
and
Speed P
proportionally. If this does not lead to an improvement, optimize
the regulator (see chapter 5.3.6).
Speed oscillating
• Check
Speed P
and
Speed I
parameter
• If the operating point is in the field weak range, check the
Fld reg P gain
and
Fld reg I gain
parameters and eventually
Voltage P
and
Voltage I
parameters.
• Remedy: Optimize the regulator as previously described
Drive not reacting to adaptive
speed regulation
• Adaptive speed regulation not enabled.
Enable spd adap
= Enabled
Motor potentiometer function
not executed
• Function not enabled.
Enable motor pot
= Enabled
• With operation via the terminal strip:
Motor pot up
and/or
Motor pot down
were not assigned to
a digital input
Jog operation not possible
• A start command is still present
• Function not enabled.
Enable jog
= Enabled
• With operation via terminal strip:
Jog +
and/or
Jog -
were not assigned to a digital input.
Internal speed reference values
not carried out
• Function not enabled.
Enab multi spd
= Enabled
• With operation via terminal strip:
Speed sel 0, Speed sel 1
and
Speed sel 2
were not assigned
to a digital input.
Multi-Ramp function not
reacting
• Function not enabled.
Enab multi rmp
= Enabled
• With operation via terminal strip:
Ramp sel 0
and
Ramp sel 1
were not assigned to a digital input
Overload not possible
• Function not enabled.
Enable overload
= Enabled
The Current regulator selftune
procedure never finishes and
continues over and over again.
• Because of the motor inductance value, the routine is executing an endless loop. The inductance
value is cycling between two values without an evolution of the
algorithm.
• Solution procedure:
1) verify the two displayed inductance values
2) insert the average value as motor inductance during the autotuning.
If the procedure does not end, repeat step 1) and 2).
Summary of Contents for TPD32-EV-...-2B
Page 1: ... Instruction manual Industrial Application DC drives TPD32 EV ...
Page 372: ... TPD32 EV 372 9 BLOCK DIAGRAM 9 1 CONTROL BLOCK DIAGRAMS ...
Page 373: ... Instruction manual 373 ...
Page 374: ... TPD32 EV 374 ...
Page 375: ... Instruction manual 375 ...
Page 376: ... TPD32 EV 376 ...
Page 377: ... Instruction manual 377 ...
Page 378: ... TPD32 EV 378 ...
Page 379: ... Instruction manual 379 ...
Page 380: ... TPD32 EV 380 ...
Page 381: ... Instruction manual 381 ...
Page 382: ... TPD32 EV 382 ...
Page 383: ... Instruction manual 383 ...
Page 384: ... TPD32 EV 384 ...
Page 385: ... Instruction manual 385 ...
Page 386: ... TPD32 EV 386 ...
Page 387: ... Instruction manual 387 ...
Page 388: ... TPD32 EV 388 ...
Page 389: ... Instruction manual 389 ...
Page 390: ... TPD32 EV 390 ...
Page 391: ... Instruction manual 391 ...
Page 392: ... TPD32 EV 392 ...
Page 393: ... Instruction manual 393 ...
Page 394: ... TPD32 EV 394 ...
Page 395: ... Instruction manual 395 ...
Page 396: ... TPD32 EV 396 ...
Page 397: ... Instruction manual 397 ...
Page 398: ... TPD32 EV 398 ...
Page 399: ... Instruction manual 399 ...
Page 400: ... TPD32 EV 400 ...
Page 401: ... Instruction manual 401 ...
Page 402: ... TPD32 EV 402 ...
Page 501: ... Instruction manual 501 APPENDIX 3 ACCESSORIES A3 1 EAM Adapter Kit EAM1579 EAM1580 ...
Page 503: ......