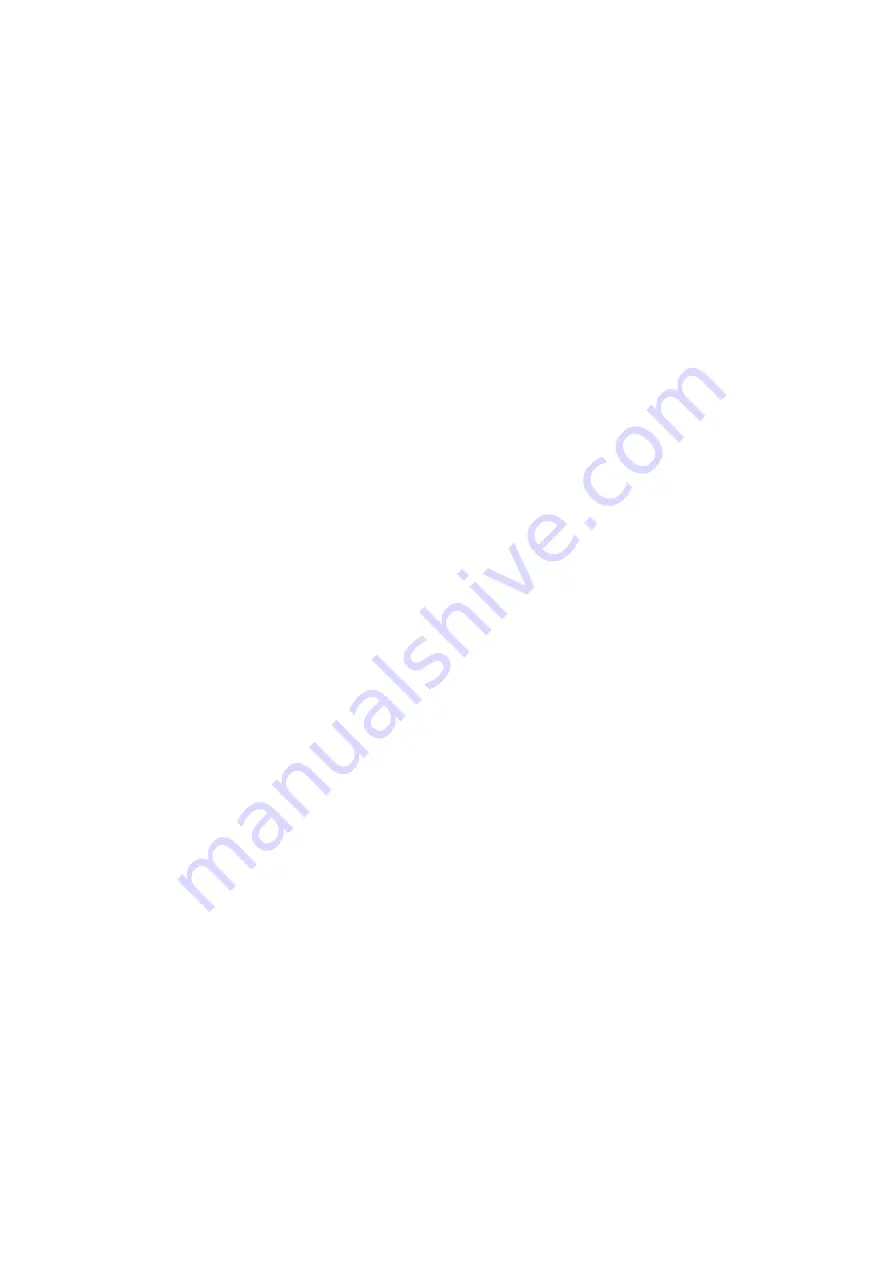
—————— TPD32-EV ——————
348
W reference
:
It is possible to use it as a monitor for the speed reference.
Setting of the parameters in the COMP CALCULATION menu
OPTION Menu
————> Torque winder
————> torque calculation
————> comp calculation
Static f
:
Compensation of the static frictions as a percentage of the drive rated current
· Check that the parameters
Static f and Dinamic f
=0
· Set the tension (tension ref)=0
· The diameter calculation function is blocked (enable the programmed digital input
as Dis diam calc)
· Operations to be carried out without line reference, jog function and materials on
the machine (the compensation of the static frictions is completely entered only
when the line speed is higher than 1.5%).
· Stopped winder/unwinder motor within the current limit (In use t curr lim+/-=0)
· Gradually increase the value of
Static f
. The motor will start rotating. Set a suit
-
able value so that the winder/unwinder can rotate with a speed near to the zero (it
must always be within the current limit. The led Ilim on the keypad is lighted)
Dynamic f
:
Compensation of the dynamic frictions as a percentage of the drive rated current
·
Set the maximum line speed reference, check that the minimum diameter has been
set in
roll diameter
(if not carry out a
Diam reset
on the minimum diameter)
·
Set temporarily the parameter
Static f
: with a value of 10-20%. The motor speed
will increase reaching the speed
Base omega
(the converter in this phase has to
overcome the current limit ) .
·
When the motor reaches its rated speed, set the parameter
Static f
with its previ
-
ously tuned value. The speed will start decreasing.
·
Increase gradually the parameter
Dynamic f
till the speed ends its decreasing phase
and the motor rotates at a constant speed.
·
Increase the speed by increasing temporarily the parameter
Static f
. Reset the
parameter
Static f
with its right value. The motor must keep the reached speed.
·
In a negative case, reset the parameter
Dynamic f
and repeat the tests till the re
-
quired conditions have been reached.
Static f Zero
By setting the parameter on “Enabled”, the friction compensation is completely inserted
for all speed values. When it set as “Disabled”, the static friction compensation is com
-
pletely inserted with Ref line speed = 1.5%.
Int acc calc En
Enabling of the calculation for the coil acceleration.
If enabled, this function calculates the angular acceleration inside the drive. In this case
it is necessary to set just the value of
Time acc/dec min
. If disabled, the parameters
Line acc % - dec % - fast stop %
and
Time acc/dec min
have to be set and the digital
inputs have to be supplied with the suitable indications.
Time acc/dec min
Set the time in [s] corresponding to the lowest acceleration, deceleration and fast de
-
celeration time.
Set time acc/dec min =15sec (time required for a fast deceleration)
Summary of Contents for TPD32-EV-...-2B
Page 1: ... Instruction manual Industrial Application DC drives TPD32 EV ...
Page 372: ... TPD32 EV 372 9 BLOCK DIAGRAM 9 1 CONTROL BLOCK DIAGRAMS ...
Page 373: ... Instruction manual 373 ...
Page 374: ... TPD32 EV 374 ...
Page 375: ... Instruction manual 375 ...
Page 376: ... TPD32 EV 376 ...
Page 377: ... Instruction manual 377 ...
Page 378: ... TPD32 EV 378 ...
Page 379: ... Instruction manual 379 ...
Page 380: ... TPD32 EV 380 ...
Page 381: ... Instruction manual 381 ...
Page 382: ... TPD32 EV 382 ...
Page 383: ... Instruction manual 383 ...
Page 384: ... TPD32 EV 384 ...
Page 385: ... Instruction manual 385 ...
Page 386: ... TPD32 EV 386 ...
Page 387: ... Instruction manual 387 ...
Page 388: ... TPD32 EV 388 ...
Page 389: ... Instruction manual 389 ...
Page 390: ... TPD32 EV 390 ...
Page 391: ... Instruction manual 391 ...
Page 392: ... TPD32 EV 392 ...
Page 393: ... Instruction manual 393 ...
Page 394: ... TPD32 EV 394 ...
Page 395: ... Instruction manual 395 ...
Page 396: ... TPD32 EV 396 ...
Page 397: ... Instruction manual 397 ...
Page 398: ... TPD32 EV 398 ...
Page 399: ... Instruction manual 399 ...
Page 400: ... TPD32 EV 400 ...
Page 401: ... Instruction manual 401 ...
Page 402: ... TPD32 EV 402 ...
Page 501: ... Instruction manual 501 APPENDIX 3 ACCESSORIES A3 1 EAM Adapter Kit EAM1579 EAM1580 ...
Page 503: ......