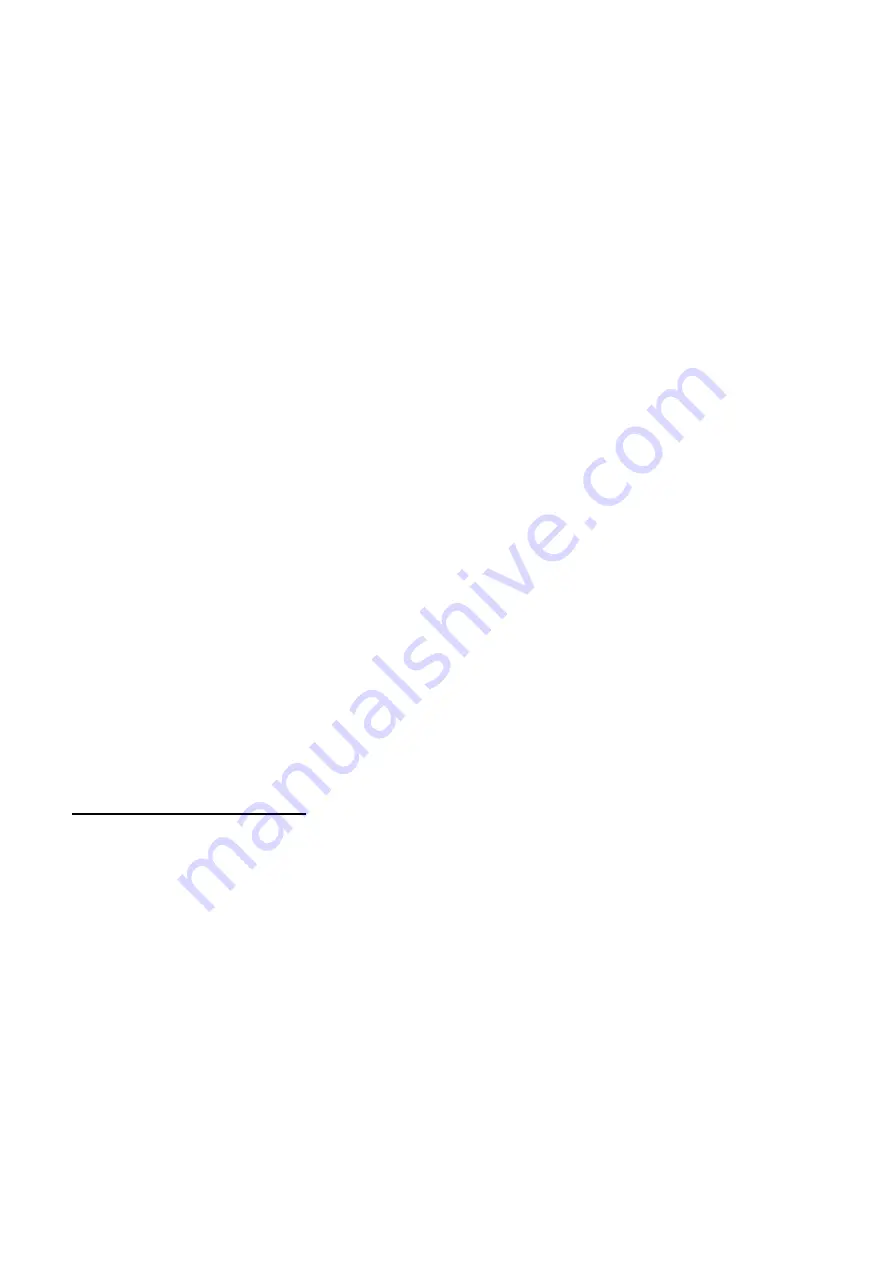
—————— TPD32-EV ——————
230
Motor potentiometer function can be activated (
Enable motor pot
) by selecting “
Config1
” or “
Config2
” . They
act as indicated in the figure 6.14.1.1 and 6.14.1.2 . The actual motorpot output value is shown in the
Motor
pot
submenu of the keypad. When controlled via the keypad, the drive can be accelerated by pressing the “+”
key and decelerated by pressing the “-” key. This corresponds to the commands
Motor pot u
p and
Motor pot
down
. Select the menu point
Motor pot oper
for this purpose.
The motor potentiometer output can be adjusted between 0 to 100 % by setting the command
Motor pot up
.
The motor potentiometer output can be reduced between 100 and 0 % by setting the command
Motor pot down
.
If the command is given when the drive is already at a stop, it will not cause the reverse running of the drive.
If the
Motor pot up
and
Motor pot down
commands are given at the same time, they will not change the motor
pot output value. When
Config2
is selected the last motor pot output value is saved when the drive is switched
off or if there is a fault. When the drive is restarted, it accelerates to this speed according to the ramp set. If the
command
Motor pot reset
is given with the drive switched off when
Config1
is selected, the motor pot output
value is deleted and the drive starts at zero speed, when
Config2
is selected the behaviour is configured through
parameter
Reset cfg
. If the status of the
Motor pot sign
command is changed while the drive is running, the
drive will reverse according to the specified ramp times. Using
Config1
, If both
Motor pot sign+
and
Motor pot
sign-
commands are ON or OFF, the motor pot output will be set to zero. Using
Config2
, the motor pot output
will not be set to zero. Using
Config2
, the output of the motor potentiometer can be active also when the drive
is disabled or the ramp block is not enabled. In those case, it will not have any effect on the speed of the motor
until the drive and the ramp block is enabled.
When
Config1
is selected the ramp must be enabled and the Start command must be present in order to use the
motor potentiometer function. When
Config2
is selected the function can be used also when the ramp is not
enabled or the Start command is not present, but of course the motor potentiometer output will not affect the
drive behaviour in these cases, except for the fact that if an analog output is configured as
Motor pot out
it will
change according to the internal motor pot output.
Three different motorpot configuration mode can be selected.
Enable motor pot
Disabled
The reference value of potentiometer function is disabled.
Config1
The motor potentiometer “
Config1
” function mode is enabled.
The ramp block receives its reference value directly from the
motor potentiometer function.
Config2
The motor potentiometer “
Config2
” function mode is enabled.
The reference from the motor potentiometer function is added
to the
Ramp ref1
+
Ramp Ref2
block.
Default configuration = Disabled.
Motor pot oper
By pressing the “+” and “-” keys of the keypad the drive can be accelerated or deceler
-
ated.
+ Accelerate - Decelerate
Motor pot sign
This parameter is only accessible via the keypad and via the serial interface or Bus.
When the drive is operated via the terminal strip, the parameters
Motor pot sign +
and
Motor pot sign -
must be used. As for TPD32-EV...2B... converters the “Positive”
function must be selected.
Positive
“Clockwise” rotation selected.
Negative
“Counterclockwise” rotation selected.
Motor pot sign +
Selection of the “Clockwise” rotation direction when the selection is carried out via
the terminal strip. The
Motor pot sign +
parameter is linked with the
Motor pot sign
-
parameter via an XOR function. This means that the command (+24V) must be given
only to one of the two terminals
High
“Clockwise” rotation direction selected.
Low
“Clockwise” rotation direction not selected.
Summary of Contents for TPD32-EV-...-2B
Page 1: ... Instruction manual Industrial Application DC drives TPD32 EV ...
Page 372: ... TPD32 EV 372 9 BLOCK DIAGRAM 9 1 CONTROL BLOCK DIAGRAMS ...
Page 373: ... Instruction manual 373 ...
Page 374: ... TPD32 EV 374 ...
Page 375: ... Instruction manual 375 ...
Page 376: ... TPD32 EV 376 ...
Page 377: ... Instruction manual 377 ...
Page 378: ... TPD32 EV 378 ...
Page 379: ... Instruction manual 379 ...
Page 380: ... TPD32 EV 380 ...
Page 381: ... Instruction manual 381 ...
Page 382: ... TPD32 EV 382 ...
Page 383: ... Instruction manual 383 ...
Page 384: ... TPD32 EV 384 ...
Page 385: ... Instruction manual 385 ...
Page 386: ... TPD32 EV 386 ...
Page 387: ... Instruction manual 387 ...
Page 388: ... TPD32 EV 388 ...
Page 389: ... Instruction manual 389 ...
Page 390: ... TPD32 EV 390 ...
Page 391: ... Instruction manual 391 ...
Page 392: ... TPD32 EV 392 ...
Page 393: ... Instruction manual 393 ...
Page 394: ... TPD32 EV 394 ...
Page 395: ... Instruction manual 395 ...
Page 396: ... TPD32 EV 396 ...
Page 397: ... Instruction manual 397 ...
Page 398: ... TPD32 EV 398 ...
Page 399: ... Instruction manual 399 ...
Page 400: ... TPD32 EV 400 ...
Page 401: ... Instruction manual 401 ...
Page 402: ... TPD32 EV 402 ...
Page 501: ... Instruction manual 501 APPENDIX 3 ACCESSORIES A3 1 EAM Adapter Kit EAM1579 EAM1580 ...
Page 503: ......