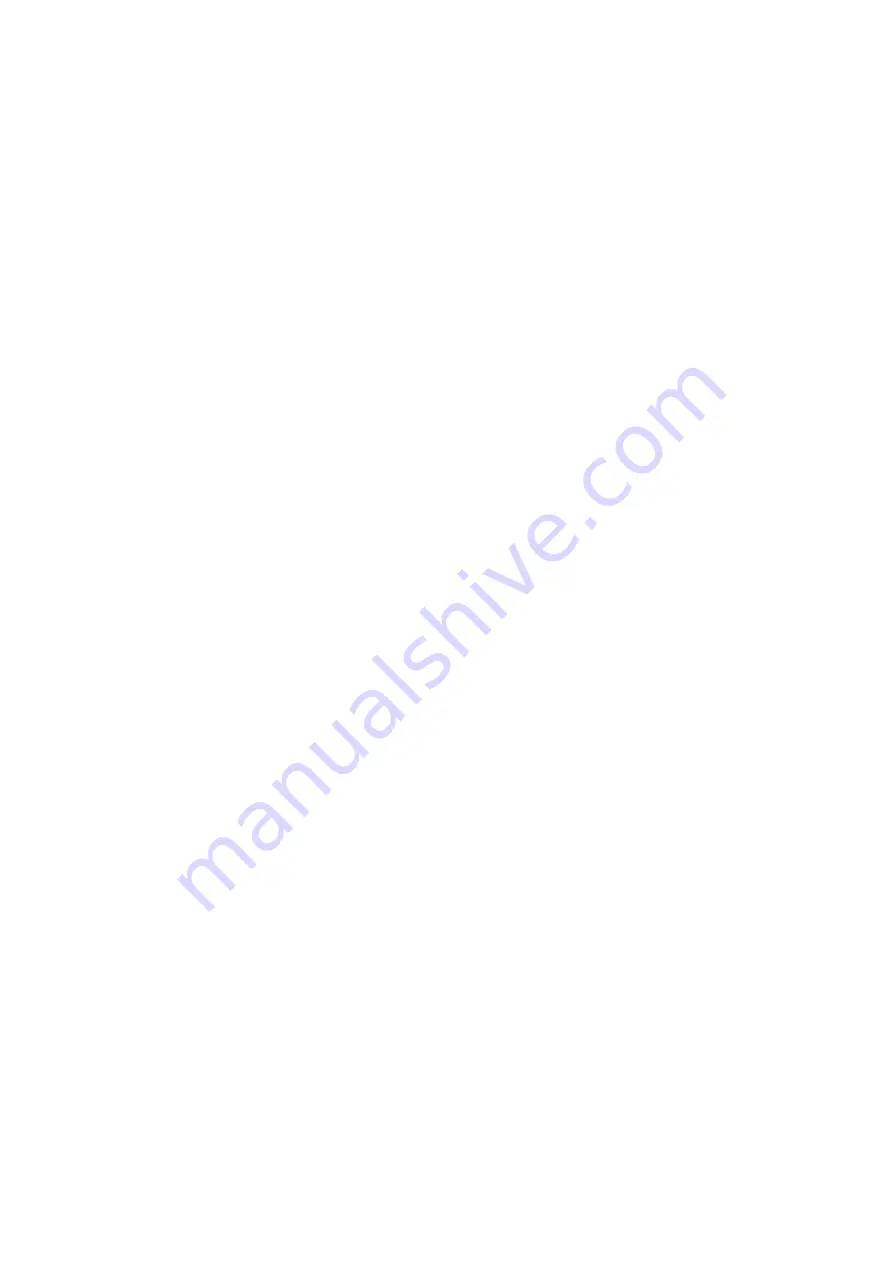
—————— Instruction manual ——————
305
Set
PID out scale
so that, along with the max. analog value on
Analog input 2
(
Feed-fwd PID
= 8500) and
with
Enable PI PID
e
Enable PD PID
= disable,
Speed ref 1
is the same at 2550rpm.
Speed ref 1
will be set in
RPM
x 4, so:
PID out scale
= (2550 x 4) / 8500 = 1.2
Set
PI central v sel
= 1.
Set
PI central v 1
= 1
In the absence of a correction carried out from the PI block of the regulator, the line speed reference (Feed-
forward) must be multiplied by 1 and sent directly to the speed regulator of the drive.
This application operates by using proportional control. The correction will be indicated in percentage according
to the line speed, from 0 to the maximum.
Program
PI top limit
and
PI bottom limit
so that the max. correction of PI block corresponds at 20% of line
speed.
PI top limit
and
PI bottom limit
parameters are the maximum and minimum multiplier factor of Feed forward
value.
At the max. line speed it will correspond 2550rpm of the motor (max. feed-forward).
Max. correction = 2550 x 20% = 510rpm
2550 + 510 = 3060rpm ——>
PI top limit
= 3060 / 2550 = 1.2
2550 - 510 = 2040rpm ——>
PI bottom limit
= 2040 / 2550 = 0.80
which will to multiply the setting of
PI central v 1
(= 1) by + 20% (1.2) and - 20% (0.80).
With this configuration, having a correction proportional to the line speed, the PI block is not able to apply ten
-
sion at speed = 0. In order to apply tension in stop conditions, it is necessary to use on the PD block.
The gains of the single components have to be set with loaded machine; it is possible to start tests with values
below indicated (default values):
Set
PI P gain PID
= 10%
Set
PI I gain PID
= 10%
Set
PD P gain PID
= 10%
In case use the derivative component for forcing the regulator output during velocity changes of the system,
programming for example:
PD D gain PID
= 5%
PD D filter PID
= 20ms
If not necessary, keep these parameters = 0.
In case it is necessary to carry out a references cascade for another drive, set
PID output
on an analog output,
for example:
Analog output 1 / Select output 1= PID output
(with
Real FF PID
= 10000 count,
Analog output 1
= 10V).
n
ote
:
If it is necessary, a system with the integral regulation enabled, with feed-forward = 0, and
the need to apply tension of the system with null error also when the machine is stopped,
please refer to the paragraph “Generic PID”.
Summary of Contents for TPD32-EV-...-2B
Page 1: ... Instruction manual Industrial Application DC drives TPD32 EV ...
Page 372: ... TPD32 EV 372 9 BLOCK DIAGRAM 9 1 CONTROL BLOCK DIAGRAMS ...
Page 373: ... Instruction manual 373 ...
Page 374: ... TPD32 EV 374 ...
Page 375: ... Instruction manual 375 ...
Page 376: ... TPD32 EV 376 ...
Page 377: ... Instruction manual 377 ...
Page 378: ... TPD32 EV 378 ...
Page 379: ... Instruction manual 379 ...
Page 380: ... TPD32 EV 380 ...
Page 381: ... Instruction manual 381 ...
Page 382: ... TPD32 EV 382 ...
Page 383: ... Instruction manual 383 ...
Page 384: ... TPD32 EV 384 ...
Page 385: ... Instruction manual 385 ...
Page 386: ... TPD32 EV 386 ...
Page 387: ... Instruction manual 387 ...
Page 388: ... TPD32 EV 388 ...
Page 389: ... Instruction manual 389 ...
Page 390: ... TPD32 EV 390 ...
Page 391: ... Instruction manual 391 ...
Page 392: ... TPD32 EV 392 ...
Page 393: ... Instruction manual 393 ...
Page 394: ... TPD32 EV 394 ...
Page 395: ... Instruction manual 395 ...
Page 396: ... TPD32 EV 396 ...
Page 397: ... Instruction manual 397 ...
Page 398: ... TPD32 EV 398 ...
Page 399: ... Instruction manual 399 ...
Page 400: ... TPD32 EV 400 ...
Page 401: ... Instruction manual 401 ...
Page 402: ... TPD32 EV 402 ...
Page 501: ... Instruction manual 501 APPENDIX 3 ACCESSORIES A3 1 EAM Adapter Kit EAM1579 EAM1580 ...
Page 503: ......