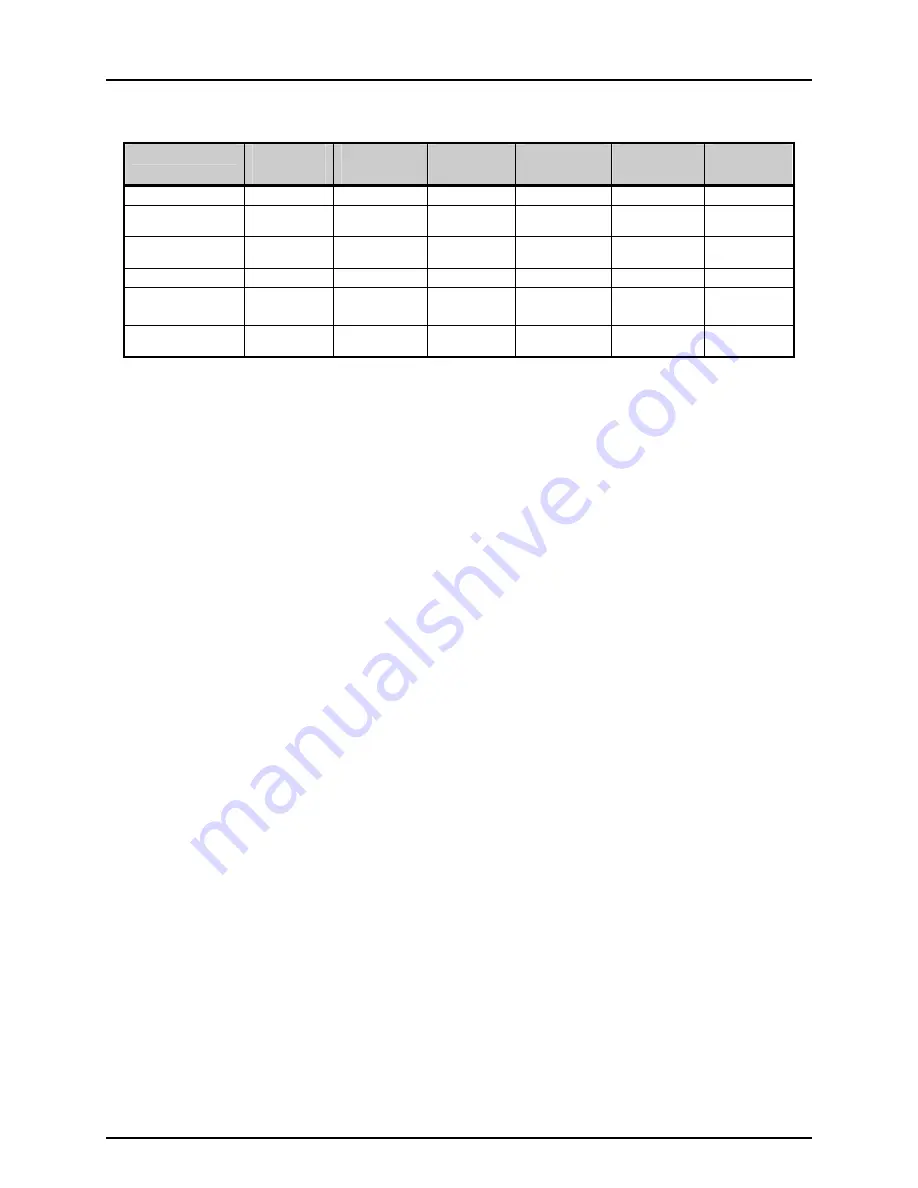
PG7000™ OPERATION AND MAINTENANCE MANUAL
© 1998-2008 DH Instruments, a Fluke Company
Page 22
Table 13.
PC-7300 Piston-Cylinder Modules Parts List
100 kPa
PC-7300-100
200 kPa
PC-7300-200
500 kPa
PC-7300-500
1 MPa
PC-7300-1
2 MPa
PC-7300-2
5 MPa
PC-7300-5
Piston-Cylinder
Kit 401552 401553 401554 401555 401556 401557
Piston-Cylinder
Module
401413 401414 401415 401559 401416 401417
Hermetic
Acetal
Bullet
Case
402400 402400 402400 402400 402400 402400
Accessory
Kit 401545 401545 401545 401544 401544 401544
O-rings
103990
101100
103990
101100
103990
101100
101096
(5) 101294
101096
(5) 101294
101096
(5) 101294
Calibration
Reports
550100 550100 550100 550100 550100 550100
2.2
SITE REQUIREMENTS
The exact PG7000 system installation is affected by the elements other than the PG7000 Platform that
make up the PG7000 system.
When selecting and preparing a site to set up the PG7000 system, the following should be considered:
•
Ambient conditions:
To achieve optimum metrological performance, ambient conditions should be
controlled and maintained within the following:
♦
Temperature:
19 to 23 °C, minimize rate of change of temperature.
♦
Relative Humidity:
10 to 60 %RH (non-condensing).
♦
Ambient Pressure:
Minimize external influences that will cause barometric instability.
♦
Air Currents:
Do not install the PG7000 Platform under a source of vertical air currents such as an
overhead air conditioning duct. These can blow on the mass load and add unquantified forces.
♦
Vibration:
Minimize local vibration. Excessive vibration will reduce the stability of the pressures
defined by PG7000 (vibration affects the floating piston). Excessive high frequency vibration, for
example from a vacuum pump on the same table as the PG7000, may affect piston sensitivity.
•
Bench stability:
Up to 100 kg may be loaded and unloaded onto the PG7000 Platform. The bench
on which the PG7000 sits should not deflect significantly under the mass load changes. This can be
verified by setting the PG7000 Platform on the bench, leveling it, loading and unloading the complete
mass set while observing whether the level setting changes.
•
Location of other components:
Plan the space required and a convenient layout for the complete
PG7000 system including the PG Terminal, mass set, pressure generation/control component(s), test
instrument connection and computer (if present). If using a
DHI
PPC, MPC, GPC or OPG to
generate/control pressure, see its Operation and Maintenance Manual for information on installing it.
If a
DHI
interconnections kit is being used to interconnect the components, see its instruction sheet.
•
Electrical and pressure supplies:
Plan the supply of electrical power to the PG Terminal and to the
pressure generation/control component(s), if needed. If using a
DHI
PPC, MPC, GPC or OPG to
generate/control pressure, see its Operation and Maintenance Manual for information on the
pressures source(s) it needs and how to connect them. Gas supplied to a PC-7100/7600
piston-cylinder module must be clean and dry (instrument grade minimum, high purity preferred) to
avoid contaminating the piston-cylinder gap.
•
Reference vacuum supply (PG7601 only):
Plan for the vacuum connection to the platform or the
optional AMH automated mass handler and the location of the reference vacuum pump.
•
Bell jar placement (PG7601 only):
Plan a location for the bell jar when it is removed from the
platform to load and unload masses. A small shelf is often used for this purpose.