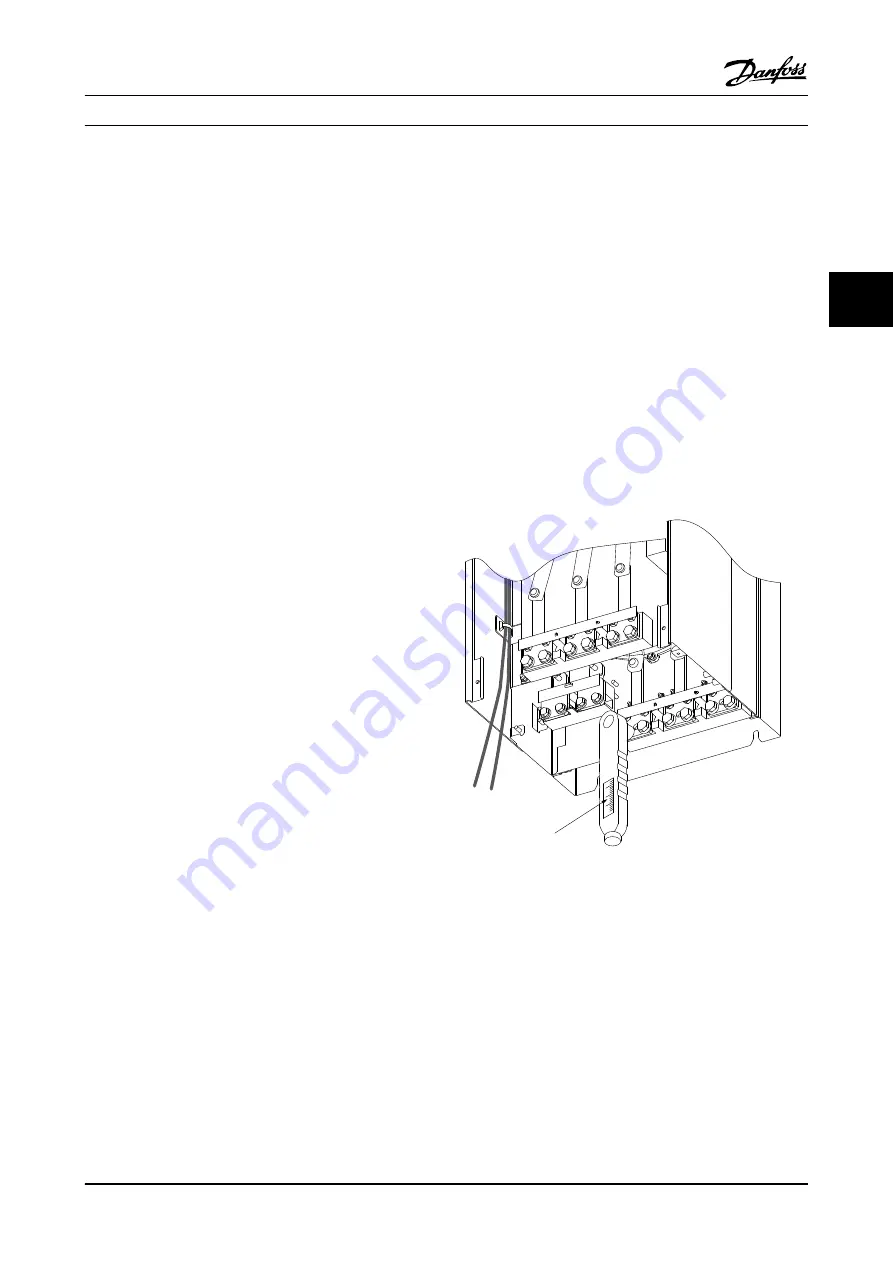
4.1.2 Grounding
The following basic issues need to be considered when
installing an adjustable frequency drive, so as to obtain
electromagnetic compatibility (EMC).
•
Safety grounding: Please note that the adjustable
frequency drive has a high leakage current and
must be grounded appropriately for safety
reasons. Always follow local safety regulations.
•
High-frequency grounding: Keep the ground wire
connections as short as possible.
Connect the different ground systems at the lowest
possible conductor impedance. The lowest possible
conductor impedance is obtained by keeping the
conductor as short as possible and by using the greatest
possible surface area.
The metal cabinets of the different devices are mounted
on the cabinet rear plate using the lowest possible HF
impedance. This prevents having different HF voltages for
the individual devices and prevents the risk of radio
interference currents running in connection cables that
may be used between the devices, as radio interference is
reduced.
In order to obtain a low HF impedance, use the fastening
bolts of the devices as HF connections to the rear plate. It
is necessary to remove insulating paint and the like from
the fastening points.
4.1.3 Extra Protection (RCD)
ELCB relays, multiple protective grounding or grounding
can be used as extra protection, provided that local safety
regulations are complied with.
In the case of a ground fault, a DC component may
develop in the fault current.
If ELCB relays are used, local regulations must be observed.
Relays must be suitable for protection of 3-phase
equipment with a bridge rectifier and for a brief discharge
on power-up.
See also the section
Special Conditions
in the Design Guide.
4.1.4 Drives with Factory-installed A1/B1
RFI Filter Option:
Line power supply isolated from ground
If the adjustable frequency drive is supplied from an
isolated line power source ( IT line power, floating delta
and grounded delta) or TT/TN-S line power with grounded
leg, the RFI switch is recommended to be turned off (OFF)
via
14-50 RFI 1
on the drive and
14-50 RFI 1
on the filter.
For further reference, see IEC 364-3. In case optimum EMC
performance is needed, parallel motors are connected or
the motor cable length is above 82 ft [25 m], it is
recommended to set
14-50 RFI 1
to [ON].
In OFF, the internal RFI capacities (filter capacitors)
between the chassis and the intermediate circuit are cut
off to avoid damage to the intermediate circuit and to
reduce the ground capacity currents (according to IEC
61800-3).
It is important to use isolation monitors that are capable
for use together with power electronics (IEC 61557-8).
4.1.5 Torque
When tightening all electrical connections it is important
to tighten with the correct torque. Too low or too high
torque results in a poor electrical connection. Use a torque
wrench to ensure correct torque.
176F
A247.12
Nm/in-lbs
-DC 88
+DC 89
R/L1 91
S/L2 92
T/L3 93
U/T1 96
V/T2 97
W/T3
Figure 4.7 Always use a torque wrench to tighten the bolts.
4.1.6 Shielded Cables
NOTE!
Danfoss recommends to use shielded cables between the
LCL filter and the AFE unit. Unshielded cables can be used
between transformer and LCL filter input side.
It is important that shielded and armored cables are
connected in a proper way to ensure the high EMC
immunity and low emissions.
How to Install
VLT AQUA 12-Pulse High Power Instruction Manual
MG.20.Y1.22 - VLT
®
is a registered Danfoss trademark
4-9
4
4