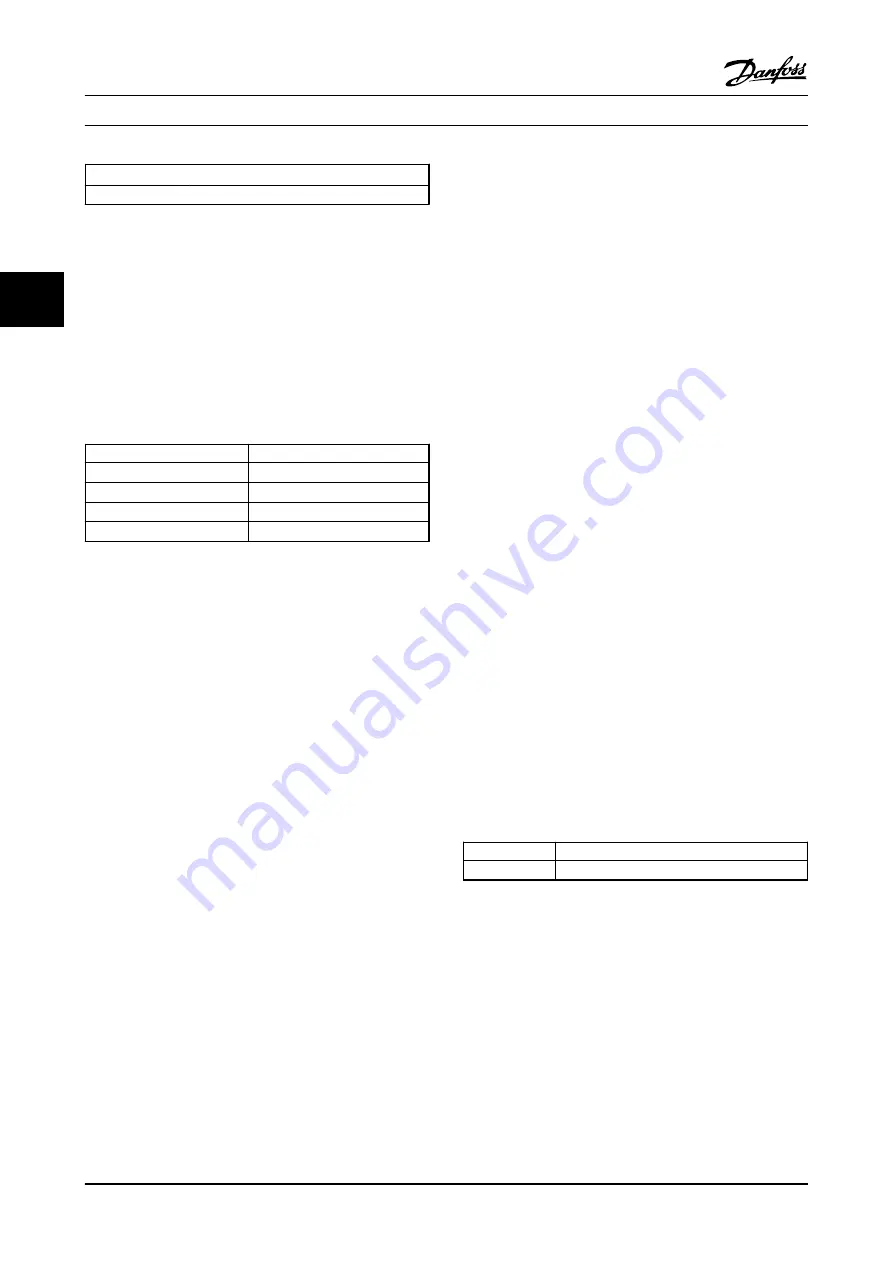
Unit Sizes
Bussmann PN*
Rating
F8-F13
GMC-800MA
800mA, 250V
Table 4.10 NAMUR Fuse
4.1.12 Motor Insulation
For motor cable lengths
≤
than the maximum cable length
listed in the General Specifications tables, the following
motor insulation ratings are recommended because the
peak voltage can be up to twice the DC link voltage, 2.8
times the AC line voltage due to transmission line effects
in the motor cable. If a motor has lower insulation rating,
it is recommended to use a du/dt or sine-wave filter.
Nominal AC Line Voltage
Motor Insulation
U
N
≤
420 V
Standard U
LL
= 1300V
420V < U
N
≤ 500 V
Reinforced U
LL
= 1600V
500V < U
N
≤ 600 V
Reinforced U
LL
= 1800V
600V < U
N
≤ 690 V
Reinforced U
LL
= 2000V
4.1.13 Motor Bearing Currents
All motors installed with 425 hp [315 kW] or higher power
drives should have NDE (Non-Drive End) insulated bearings
installed to eliminate circulating bearing currents. To
minimize DE (Drive End) bearing and shaft currents proper
grounding of the drive, motor, driven machine, and motor
to the driven machine is required.
Standard Mitigation Strategies:
1.
Use an insulated bearing
2.
Apply rigorous installation procedures
-
Ensure the motor and load motor are
aligned
-
Strictly follow the EMC Installation
guideline
-
Reinforce the PE so the high frequency
impedance is lower in the PE than the
input power leads.
-
Provide a good high frequency
connection between the motor and the
adjustable frequency drive for instance
by shielded cable which has a 360°
connection in the motor and the
adjustable frequency drive
-
Make sure that the impedance from
adjustable frequency drive to building
ground is lower that the grounding
impedance of the machine. This can be
difficult for pumps.
-
Make a direct ground connection
between the motor and load motor.
3.
Lower the IGBT switching frequency
4.
Modify the inverter waveform, 60° AVM vs.
SFAVM
5.
Install a shaft grounding system or use an
isolating coupling.
6.
Apply conductive lubrication
7.
Use minimum speed settings, if possible.
8.
Try to ensure the line voltage is balanced to
ground. This can be difficult for IT, TT, TN-CS or
Grounded leg systems
9.
Use a dU/dt or sinus filter
4.1.14 Control Cable Routing
Tie down all control wires to the designated control cable
routing as shown in the picture. Remember to connect the
shields in a proper way to ensure optimum electrical
immunity.
Field Installed Network Module options connection
Connections are made to the network options on the
control card. For details, see the relevant network
instructions. The cable must be placed in the provided
path inside the adjustable frequency drive and tied down
together with other control wires.
Installation of field-installed 24 volt external DC supply
option module (OPC24VPS)
Torque: 0.5–0.6Nm (5in-lbs)
Screw size: M3
No.
Function
35 (-), 36 (+)
24V external DC supply
24 V DC external supply can be used as low-voltage supply
to the control card and any I/O or network option cards
installed. This enables full operation of the LCP (including
parameter setting) without connection to line power.
Please note that a warning of low voltage will be given
when 24 V DC has been connected; however, there will be
no tripping.
How to Install
VLT AQUA 12-Pulse High Power Instruction Manual
4-14
MG.20.Y1.22 - VLT
®
is a registered Danfoss trademark
4
4