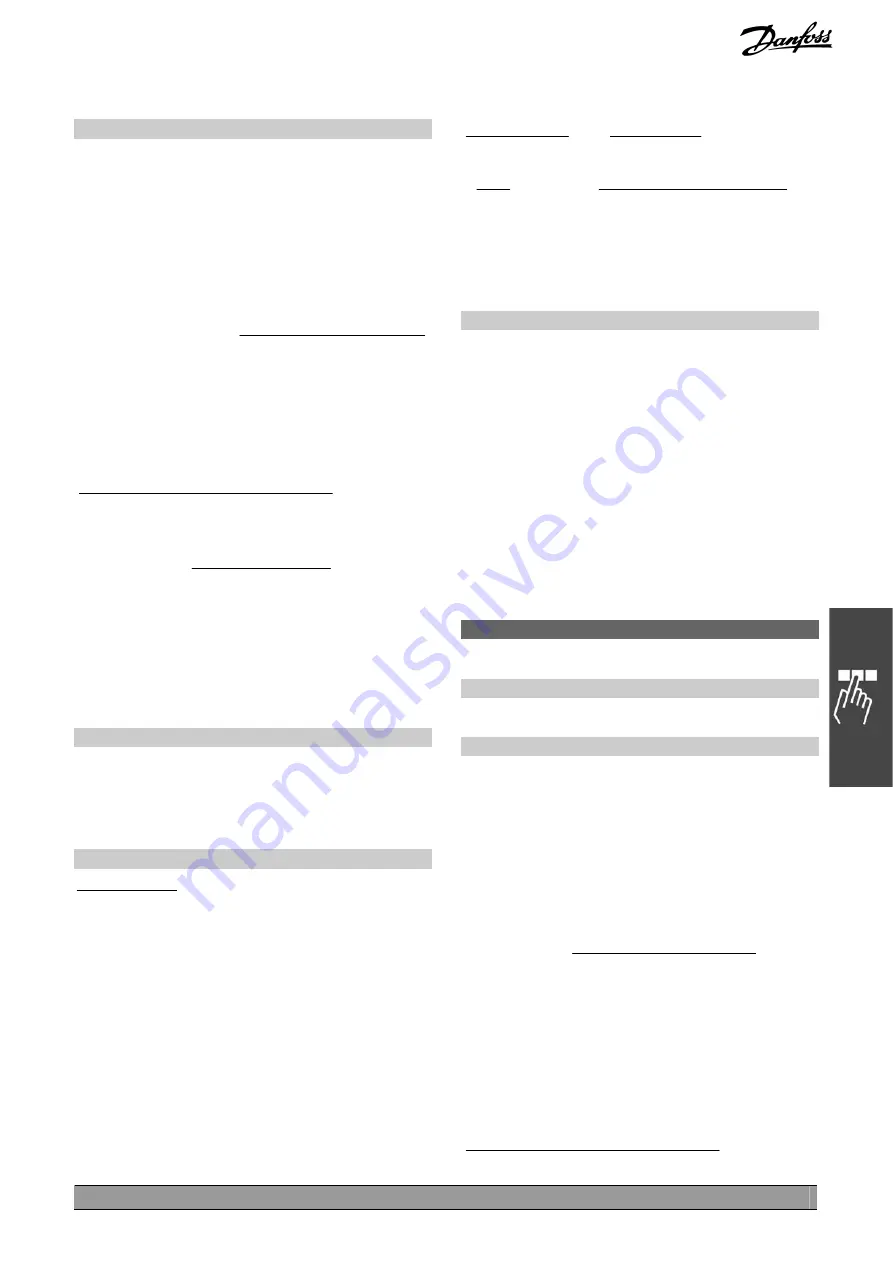
MCO 305 Design Guide
__ Parameter Reference __
¾
default setting
[ ]
value for use in communication via serial communication port
MG.33.L4.02 – VLT
®
is a registered Danfoss trademark
195
Function
The synchronization is described with a ratio of qc
(Master : Slave); SYNCFACTM determines the syn-
chronization factor for the master.
Syncfactor Master
and par. 33-11
Syncfactor Slave
make the compensation of different drive factors
possible or the adaptation of the slave speed in
relation to the master speed set.
Master
yncfactor
10
-
33
par.
Slave
yncfactor
11
-
33
par.
Velocity
ster
a
M
Velocity
Slave
S
S
In conjunction with curve synchronization the para-
meters SYNCFACTM and SYNCFACTS are used to
transform qc into MU units.
This allows the user to work with meaningful units
in the CAM-Editor. See example 2 below.
MU
1
qc
Factor
Scaling
4
Resolution
Encoder
Factor
Gearing
provided that:
Output
on
s
Revolution
s
Revolution
Motor
Factor
Gearing
Encoder =
Incremental encoder (the multiplier
4 is omitted in the case of absolute
encoders)
Scaling factor = Number of user units UU (qc) that
correspond to one revolution at the
drive.
Example 1
If the master is to run twice as fast as the slave,
then the ratio is 2 : 1
par.
33-10
Syncfactor Master
=
2
par.
33-11
Syncfactor Slave
=
1
Example 2
Conveyor belt:
The input should be possible in 1/10 mm
resolution.
The drive is connected to the conveyor belt with a
gearing of 25:11; this means that the motor makes
25 revolutions and the drive pulley 11.
Gear factor = 25/11
Incremental encoder directly on the master drive;
encoder resolution = 4096
The drive pulley has 20 teeth/revolution, 2 teeth
correspond to 10 mm; thus, 1 revolution = 100
mm conveyor belt feed.
Thus, the scaling factor is 1000
Slave
Syncfactor
Master
Syncfactor
11
-
33
par.
10
-
33
par.
MU
1
qc
55
2048
MU
1
qc
11
1000
4
4096
25
qc
1000
4
4096
25/11
u
u
Set the following parameters in order to work with
1/10 degree division
par.
33-10
Syncfactor Master
=
2048
par.
33-11
Syncfactor Slave
=
55
Example 3
Calculation of the scaling factor for a friction drive:
Assume that the output is equipped with a friction
wheel (radius 60 mm); we want to work with a
resolution of 1/10 mm:
One revolution on the output is thus calculated as
follows:
Scaling factor
= 2
3
r * 10 = 2
3
* 60 * 10
=
3969.91
Scaling factor
= 3970
Since an error will occur in any case due to the
rounding, a marker adjustment must be performed
after each full revolution.
33-11 Synchronization Factor Slave (M:S)
SYNCFACTS
Range
–MLONG
–
MLONG
¾
1
Function
The synchronization is described with a ratio of qc
(Master : Slave);
Syncfactor Slave
determines the
synchronization factor for the slave.
Parameters 33-10
Synchronizing Factor Master
and
33-11
Syncfactor Slave
make the compensation of
different drive factors possible or the adaptation of
the slave speed in relation to the master speed set.
Master
Syncfactor
10
-
33
par.
Slave
Syncfactor
11
-
33
par.
Velocity
Master
Velocity
Slave
In conjunction with CAM synchronization the para-
meters
Synchronizing Factor Master
and
Slave
are
used to transform qc into MU. This allows the user
to work with meaningful units in the CAM-Editor.
See example 2 in par. 33-10.
See prerequisites of the formula in par. 33-10
Synchronizing Factor Master
.
MU
1
qc
Factor
Scaling
4
Resolution
Encoder
Factor
Gearing
Summary of Contents for MCO 305
Page 4: ......