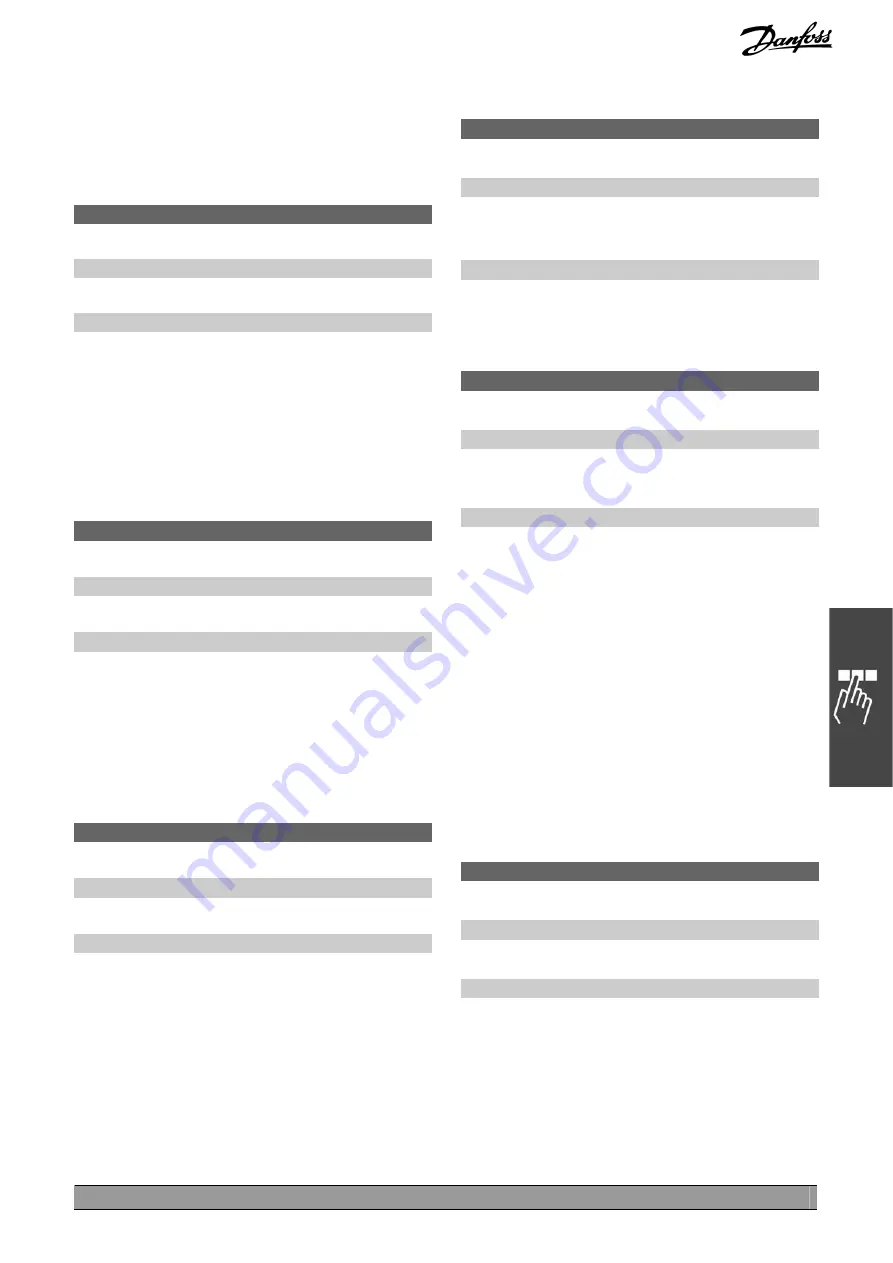
MCO 305 Design Guide
__ Parameter Reference __
¾
default setting
[ ]
value for use in communication via serial communication port
MG.33.L4.02 – VLT
®
is a registered Danfoss trademark
189
32-6* PID-Controller
Optimize the controller using the following control
parameters:
32-60 Proportional Factor
KPROP
Range
0 – 100000
¾
30
Function
The
Proportional Factor
KPROP indicates the linear
correction factor with which the deviation between
the current set and actual position is evaluated and
a corresponding correction of the motor speed is
made.
Rule of Thumb:
KPROP greater = Drive will become 'stiffer'
KPROP too high = Tendency to overswing
32-61 Derivative Value for PID Control
KDER
Range
0 – 100000
¾
0
Function
The
Derivative Value
is the correction factor with
which the changing speed of a motor position error
is evaluated.
The
Derivative Value
works against the tendency to
overswing due to a high P-share and 'dampens' the
system. However, if the
Derivative Value
selected is
too large this will lead to a 'nervous' drive.
32-62 Integral Factor
KINT
Range
0 – 100000
¾
0
Function
The
Integral Factor
KINT is the weighting factor,
with which at time n the sum of all motor position
errors are evaluated.
The
Integral Factor
of the PID filter causes a cor-
responding corrective motor torque which increases
over time. Through the integral share a static posi-
tion error is reduced to zero, even if a constant
load is affecting the motor.
However, an
Integral Factor
which is too large
leads to a 'nervous' drive.
32-63 Limit Value for Integral Sum
KILIM
Range
0 – 1000
¾
1000
0 = Integral off
Function
This parameter limits the integral sum in order to
avoid instability and PID wind-up in case of feed-
back error.
32-64 PID Bandwidth
BANDWIDTH
Range [unit]
0 – 1000 [1/10 %]
0 = PID off
¾
1000
Function
The value 1000 means that the PID filter can out-
put the full command value. For a
Bandwidth
of
500 only 50 % of the set value is output. Thus,
values less than 1000 limit the P-share accordingly.
The bandwidth in which the PID controller should
function can be limited, for example to avoid the
built-up of a vibration in case of a system which
could be jeopardized by vibrations.
However, then it is necessary to enter considerably
higher values for the parameters 32-65
Velocity
and 32-66
Acceleration Feed-forward
in order to
achieve the corresponding control. A system
adjusted in such a manner is not as dynamic as it
could be, but is considerably more stable and tends
to experience less uncontrolled vibrations.
32-65 Velocity Feed-forward
FFVEL
Range
0 – 100000
¾
0
Function
When a control has a limited
Bandwidth
then a
base velocity must be set so that it can be ruled
out that the control will entirely prevent the drive
from running due to the limit set.
Velocity Feed-forward
indicates the value with
which the velocity forward feed is completed.
Summary of Contents for MCO 305
Page 4: ......