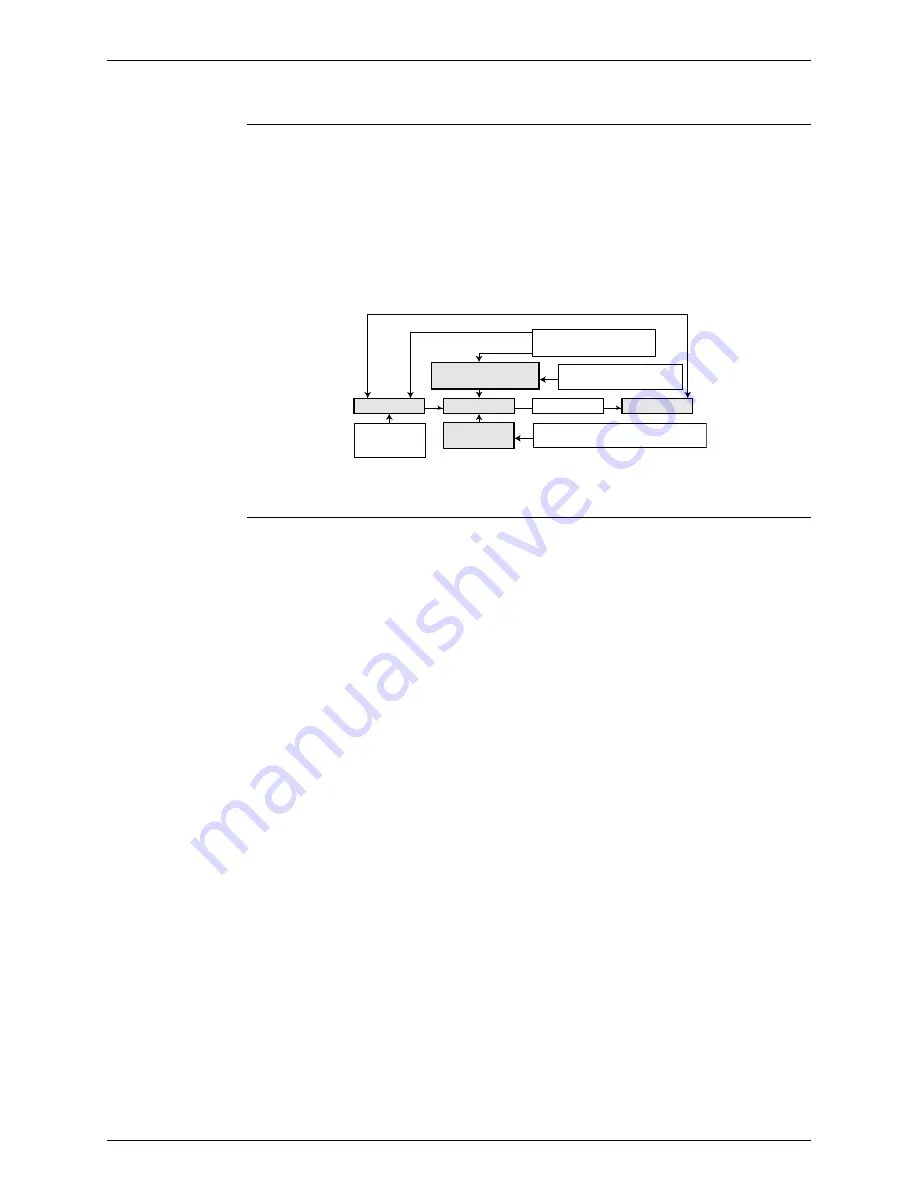
Control Specification
SiBE12-908
41
Function and Control
3.3
Frequency Control
Outline
Frequency that corresponds to each room’s capacity is determined according to the difference
in the temperature of each room and the temperature that is set by the remote controller.
The function is explained as follows.
1. How to determine frequency.
2. Frequency command from an indoor unit. (The difference between a room temperature and
the temperature set by the remote controller.)
3. Frequency command from an indoor unit. (The ranked capacity of the operating room).
4. Frequency initial setting.
5. PI control.
Detail
How to Determine Frequency
The compressor frequency is determined by taking the following steps.
For Heat Pump Model
1. Determine command frequency
Command frequency is determined in the following order of priority.
1.1 Limiting defrost control time
1.2 Forced cooling
1.3 Indoor frequency command
2. Determine upper limit frequency
Set a minimum value as an upper limit frequency among the frequency upper limits of the
following functions:
Compressor protection, input current, discharge pipe temperature, low Hz high pressure
limit, heating peak-cut, freeze-up protection, defrost.
3. Determine lower limit frequency
Set a maximum value as an lower limit frequency among the frequency lower limits of the
following functions:
Four way valve operation compensation, draft prevention, pressure difference upkeep.
4. Determine prohibited frequency
There is a certain prohibited frequency such as a power supply frequency.
(R1375)
Frequency changes by PI control < repeats when frequency becomes lower
Command frequency X repeats when frequency becomes lower
Each drooping function
Input current control, etc.
Each upper limit function
Compressor protection function
Skip control
Each lower limit function
Four way valve operating compensation, etc. (*)
Command frequency
Initial frequency
PI control
Defrost control (*)
*; only for heat pump model
Upper limit frequency
FMAX
Limit frequency
Lower limit frequency
FMIN
Target frequency