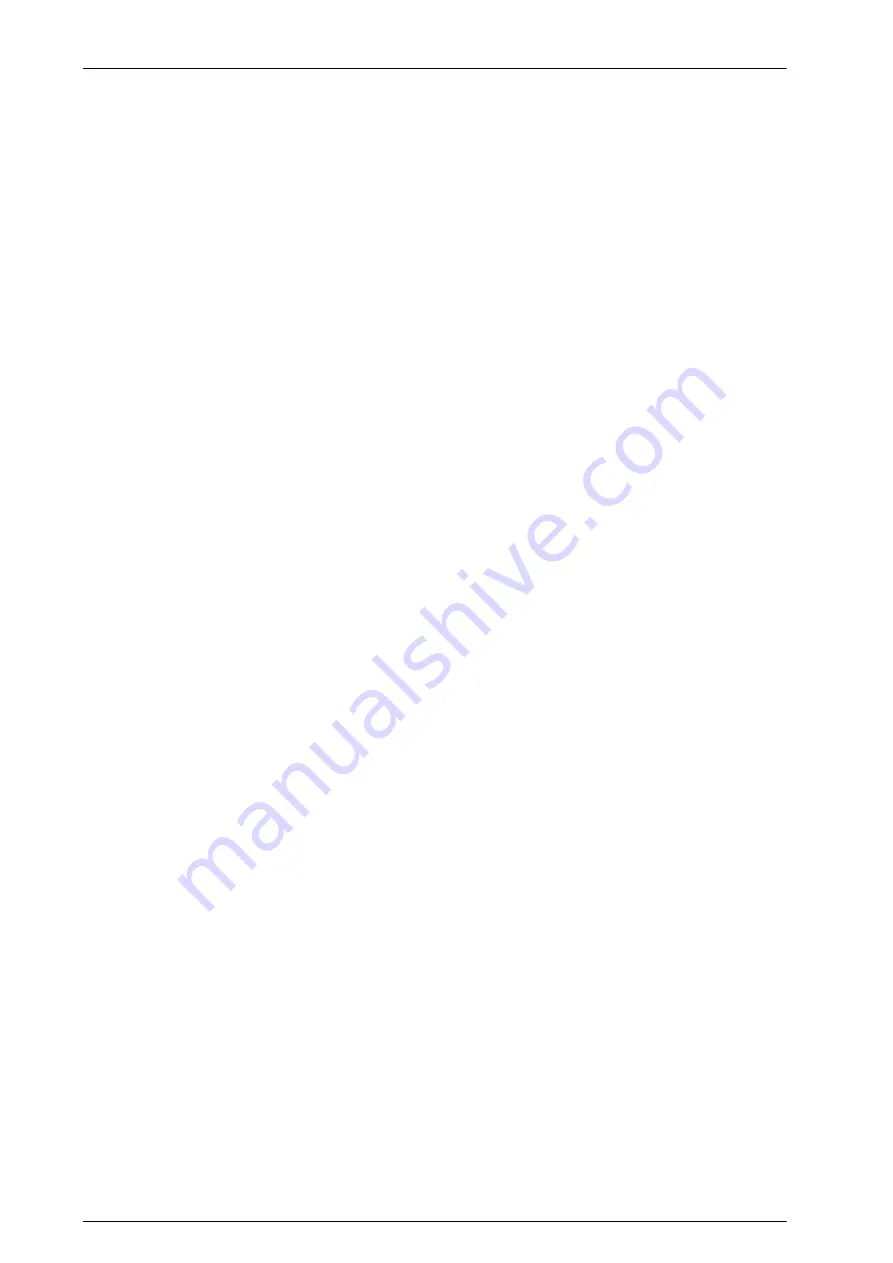
Chapter 1
:
Safety
6
SE505 Hardware Manual
Indicator Lights
In both the Teach and Solder Paste Inspection software applications, you can specify the
conditions that turn on the indicator lights on the SE505 light pole. Refer to the
Teach Online
Help or Solder Paste Inspection Online Help
for these procedures. Refer to
Safety of Machinery
EN 60204-1:1998, section 10.3 Indicator lights and displays, Table 3 for standard indicator light
definitions.
The lights also indicate that the power up sequence for the system is complete. Refer to “
Summary of Contents for SE505
Page 1: ...SE505 Hardware Manual ...
Page 6: ...Contents vi SE505 Hardware Manual ...
Page 10: ...x SE505 Hardware Manual ...
Page 72: ...Chapter 3 Installation 62 SE505 Hardware Manual ...
Page 168: ...Chapter 4 Replacing Components and Preventive Maintenance 158 SE505 Hardware Manual ...
Page 180: ...Index 170 SE505 Hardware Manual ...