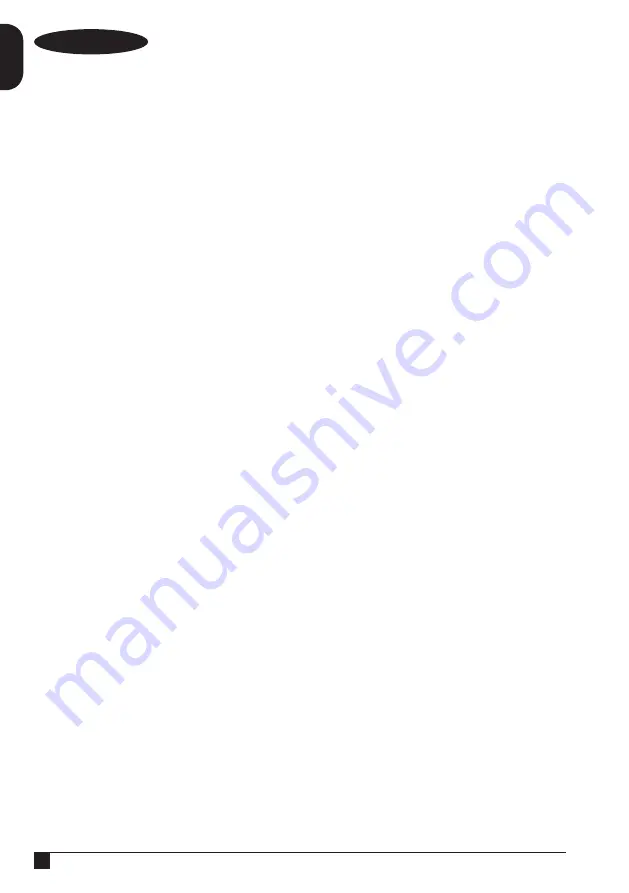
ENGLISH
(Original instructions)
14
repair procedures is required when equipment with flam
-
mable refrigerants is affected.
In many countries, this training is carried out by national
training organisations that are accredited to teach the
relevant national competency standards that may be set
in legislation.
The achieved competence should be documented by a
certificate.
Training
The training should include the substance of the following:
Information about the explosion potential of flammable
refrigerants to show that flammables may be dangerous
when handled without care.
Information about potential ignition sources, especially
those that are not obvious, such as lighters, light switches,
vacuum cleaners, electric heaters.
Information about the different safety concepts:
Unventilated – (see Clause GG.2) Safety of the appliance
does not depend on ventilation of
the housing. Switching off the appliance or opening of the
housing has no significant effect on the safety. Neverthe
-
less, it is possible that leaking refrigerant may accumulate
inside the enclosure and flammable atmosphere will be
released when the enclosure is opened.
Ventilated enclosure – (see Clause GG.4) Safety of the
appliance depends on ventilation of
the housing. Switching off the appliance or opening of the
enclosure has a significant effect
on the safety. Care should be taken to ensure a sufficient
ventilation before.
Ventilated room – (see Clause GG.5) Safety of the appli-
ance depends on the ventilation of
the room. Switching off the appliance or opening of the
housing has no significant effect on
the safety. The ventilation of the room shall not be
switched off during repair procedures.
Information about the concept of sealed components and
sealed enclosures according to IEC 6007915:2010.
Information about the correct working procedures:
Commissioning
Ensure that the floor area is sufficient for the refrigerant
charge or that the ventilation duct is assembled in a
correct manner.
Connect the pipes and carry out a leak test before charg-
ing with refrigerant.
Check safety equipment before putting into service.
Maintenance
Portable equipment shall be repaired outside or in a work-
shop specially equipped for servicing units with flammable
refrigerants.
Ensure sufficient ventilation at the repair place.
Be aware that malfunction of the equipment may be
caused by refrigerant loss and a refrigerant leak is
possible.
Discharge capacitors in a way that won’t cause any spark.
The standard procedure to short circuit the capacitor
terminals usually creates sparks.
Reassemble sealed enclosures accurately. If seals are
worn, replace them.
Check safety equipment before putting into service.
Repair
Portable equipment shall be repaired outside or in a work-
shop specially equipped for servicing units with flammable
refrigerants.
Ensure sufficient ventilation at the repair place.
Be aware that malfunction of the equipment may be
caused by refrigerant loss and a refrigerant leak is
possible.
Discharge capacitors in a way that won’t cause any spark.
When brazing is required, the following procedures shall
be carried out in the right order:
Remove the refrigerant. If the recovery is not required by
national regulations, drain
the refrigerant to the outside. Take care that the drained
refrigerant will not cause any danger. In doubt, one person
should guard the outlet. Take special care that drained
refrigerant will not float back into the building.
Evacuate the refrigerant circuit.
Purge the refrigerant circuit with nitrogen for 5 min.
Evacuate again.
Remove parts to be replaced by cutting, not by flame.
Purge the braze point with nitrogen during the brazing
procedure.
Carry out a leak test before charging with refrigerant.
Reassemble sealed enclosures accurately. If seals are
worn, replace them.
Check safety equipment before putting into service.
Decommissioning
If the safety is affected when the equipment is taken out
of service, the refrigerant charge shall be removed before
decommissioning.
Ensure sufficient ventilation at the equipment location.
Summary of Contents for BXAC12000E
Page 1: ...FR EN DE IT ES PT NL PL EL RU RO BG www blackanddecker eu BXAC12000E...
Page 2: ...A6 A5 A1 A7 A2 A3 A7 A B C D E F G I J K L M P N O 5 M M C C F F 4 3 6 2 1...
Page 3: ...Fig 1 Fig 2...
Page 114: ...114 BXAC12000E Black Decker 14 5 m2 R290 300 R290 R290...
Page 115: ...115 8 50 cm 50 cm T 250VAC 3 15A...
Page 116: ...116 16 30 mA...
Page 119: ...119 BXAC12000E BXAC12000E 3 FL LCD standby 10 on off pH 2...
Page 120: ...120 3 E1 E2 FL...
Page 122: ...122 R290 CO2...
Page 123: ...123 LFL 25...
Page 124: ...124 OFN OFN OFN OFN OFN a b c d e f g h...
Page 125: ...125 80 i j k GG 2 GG 4...
Page 126: ...126 GG 5 IEC 6007915 2010 5 5...
Page 127: ...127 5...
Page 128: ...128 BXAC12000E Black Decker 14 5 2 R290 300 R290 R290...
Page 129: ...129 8 50 50 T 250 3 15...
Page 130: ...130 16 30 H...
Page 131: ...131 A B C D E F G I J K L M N O P A1 On Off A2 A3 A5 A6 A7 1 2 3 4 5 6 50 50 12 32 C...
Page 132: ...132 Fig 1 Fig 2 2 ON OFF 24 C BXAC12000E F1 F2 F3 F1 88 24 00 1 24 16 30 C A2 2 A7 6 A3 3...
Page 133: ...133 BXAC12000E BXAC12000E FL 10 ON OFF 2 A1...
Page 134: ...134 pH 3 E1 E2 FL...
Page 136: ...136 R290 CO 2...
Page 137: ...137...
Page 138: ...138 LFL 25 OFN OFN OFN OFN OFN a b c d e f g h 80...
Page 139: ...139 i j k GG 2...
Page 140: ...140 GG 4 GG 5 IEC 6007915 2010 5...
Page 141: ...141 5 5...
Page 156: ...156 BXAC12000E Black Decker 14 5 m2 R290 300 R290 R290...
Page 157: ...157 8 50 50 250VAC 3 15A...
Page 158: ...158 16 c a pa o a a e c po c a epe c 30 mA...
Page 159: ...159 A B C D E F G I J K L M N O P A1 ON OFF A2 A3 A5 A6 A7 1 2 3 4 5 6 50 50 12 C 32 C...
Page 161: ...161 3 FL Stand by 10 On Off pH 2...
Page 162: ...162 3 E1 E2 FL U...
Page 164: ...164 R290 CO2...
Page 165: ...165...
Page 166: ...166 LFL 25 OFN OFN OFN 0 OFN OFN a b c d e...
Page 167: ...167 f g h 80 i j k...
Page 168: ...168 GG 2 GG 4 GG 5 IEC 60079 15 2010 5...
Page 169: ...169 5 5...