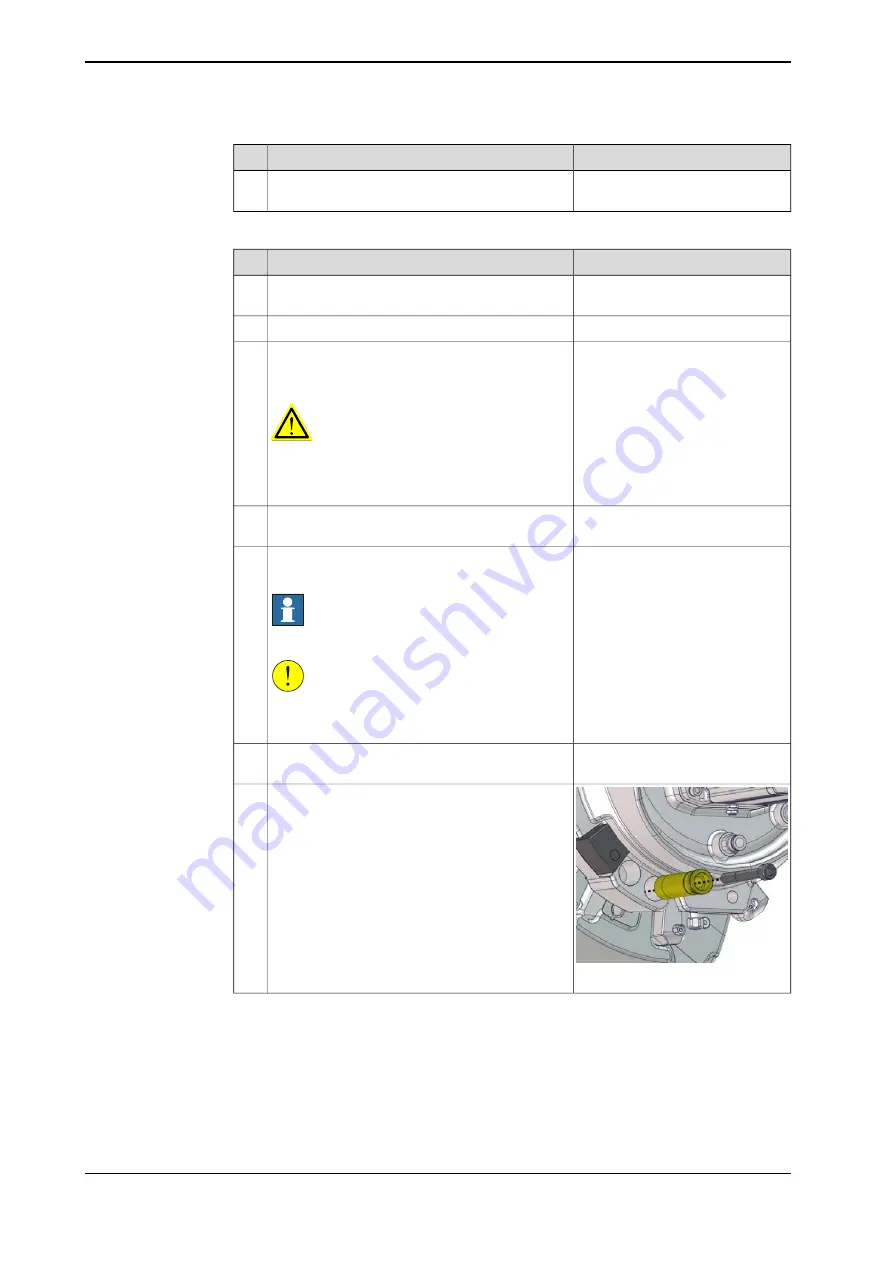
Note
Action
Remove the bolts securing the robot to the
foundation.
4
Orienting and securing the robot
Note
Action
See user instructions enclosed with
the fork lift accessory.
Lift the robot using the fork lift accessory.
1
Move the robot close to its installation location.
2
See user instructions enclosed with
the turning tool.
Rotate the robot into inverted position using the
turning tool or using a fork lift truck with a rotator
attachment.
DANGER
Make sure that there is enough space underneath
the robot. See user instructions for the turning
tool.
3
Guide the robot using two M24 screws while lifting
it into its mounting position.
4
Suitable screws, lightly lubricated:
M24x100 (8 pcs), 8.8.
Fit the bolts and washers in the base attachment
holes.
Note
Lightly lubricate screws before assembly.
5
Suitable washer: 4 mm flat washer.
Screw tightening yield point utiliza-
tion factor (v) (according to
VDI2230): 90% (v=0.9).
Tightening torque:
CAUTION
If high stress on screws are suspected, replace
used screws with new ones.
550 Nm (screws lubricated with
Molykote 1000)
600-725 Nm, typical 650 Nm
(screws none or lightly lubricated)
Tighten bolts in a crosswise pattern to ensure that
the base is not distorted.
6
xx1700000269
Remove the yellow sleeve and transportation lock
screw from the transportation and turning position.
7
Continues on next page
448
Product manual - IRB 6700Inv
3HAC058254-001 Revision: L
© Copyright 2017 - 2020 ABB. All rights reserved.
4 Repair
4.6.3 Replacing the rear bearings on the balancing device
Continued
Summary of Contents for IRB 6700I
Page 1: ...ROBOTICS Product manual IRB 6700Inv ...
Page 16: ...This page is intentionally left blank ...
Page 40: ...This page is intentionally left blank ...
Page 182: ...This page is intentionally left blank ...
Page 672: ...This page is intentionally left blank ...
Page 704: ...This page is intentionally left blank ...
Page 720: ...This page is intentionally left blank ...
Page 722: ...This page is intentionally left blank ...
Page 729: ......