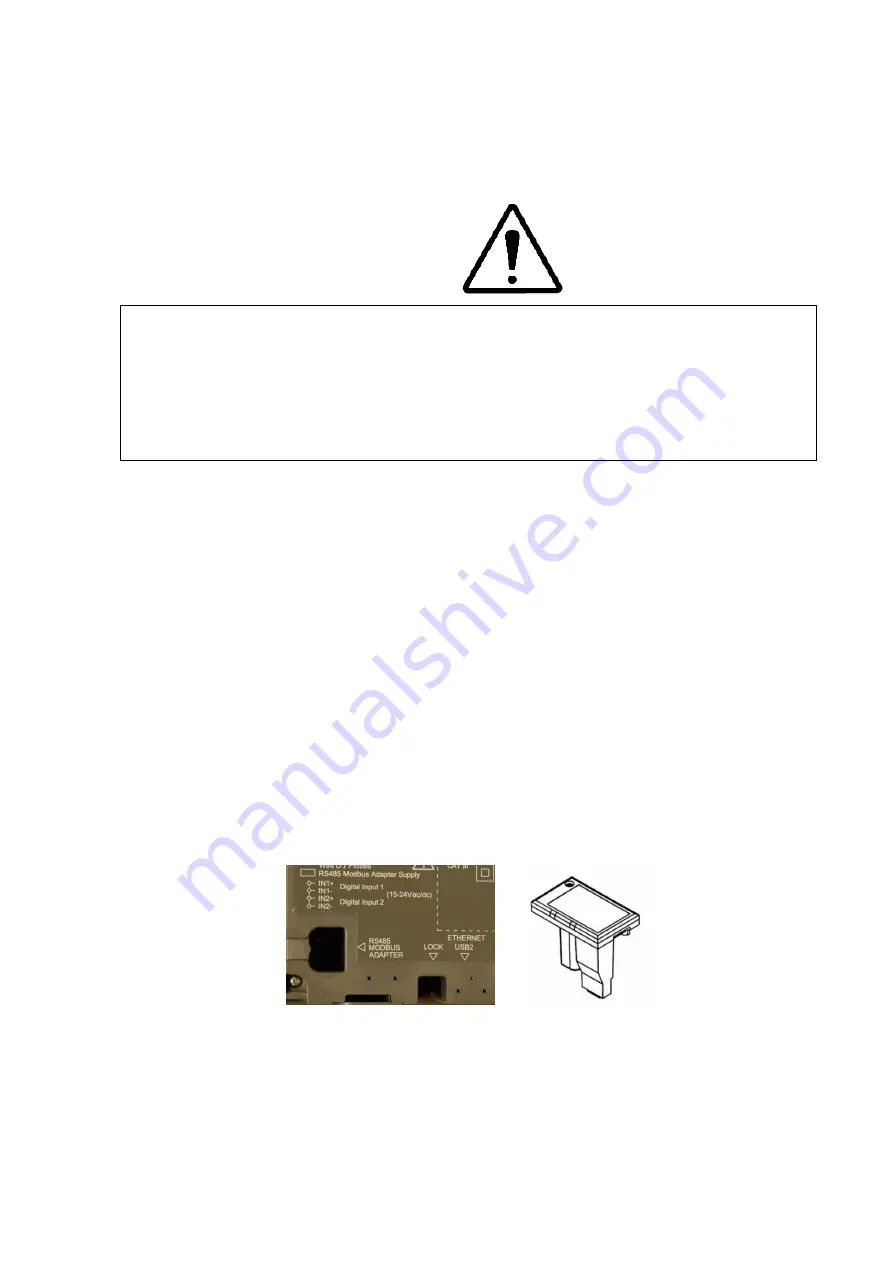
78 Electrical design and installation
Manual Energy Storage Inverter ESI-S
−
The connection of the Ethernet cable used for Modbus TCP communication
(optional)
−
The connection of the RS485 Modbus RTU adapter (optional)
The connections of the aforementioned accessories are discussed next.
WARNING: Before cabling any of the circuits discussed below, switch off the power
supply to the inverter. When the inverter has already been installed on site, this must
be done by opening the protection system located just upstream of the inverter and
opening the auxiliary fuse box present in the inverter. Wait for at least 25 minutes to
allow for the DC capacitors to discharge when the inverter has been connected to the
network before. Failure to do so may result in lethal injury or death.
6.15.1 External communication with ESI
The ESI Inverter communicates with a computer in three possible ways:
−
Using our in-house communication software called PQF-Link (rs232)
−
Using any communication system supporting the Modbus TCP protocol
−
Using any communication system supporting the Modbus RTU protocol
For communication over Modbus TCP, the computer can be connected through the
Ethernet port using standard cable (RJ45).
For communication over Modbus RTU, we need a RS485 Modbus adapter (as shown in
). This adapter has to be connected to the rear side of the ESI-Manager. This is
done by inserting the adapter plug firmly in the dedicated socket.
shows the
location at the rear of the ESI-Manager where the plug has to be inserted. The user can
use custom software where the standard Modbus RTU protocol is implemented or any
other standard software (OPC server, SCADA …).
Figure 58: Location at rear of ESI-Manager where the serial communication
cable has to be inserted
More information on the PQF-Link software or Modbus communication can be found in
the ‘PQF-Link installation and user’s guide’ and ‘2GCS239011A0070_ESI-Manager
communication with Modbus RTU, Modbus TCP and PQF-Link protocols’.