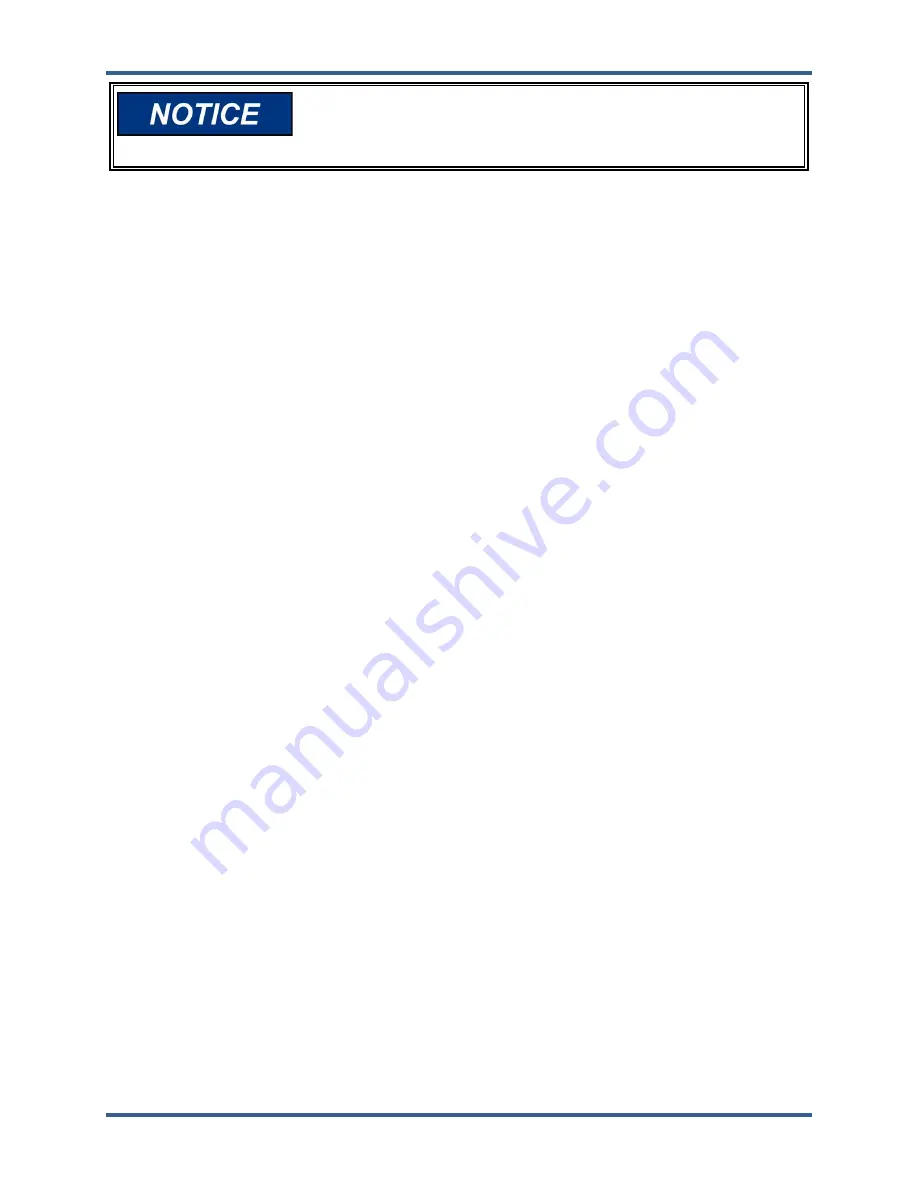
Manual 35116
505HT for Pelton Turbines
Woodward
51
If you are controlling the Pond Level (forebay level), be aware that
increasing your Pond Level set point results in decreasing the Nozzle
position, and vice-versa. Thus, the Raise input will result in moving
the Nozzles in the closing direction.
When Level Control is enabled, the Raise and Lower contact inputs control the Level Set Point. The Level
Set Point “Raise/Lower Rate” controls how fast the set point ramps up and down. The level set point can
also be adjusted using either Modbus or display commands.
A Remote Level Reference can be used as well. There are three ways to enable the Remote Level
Reference: closing a digital input called “Enable Remote Level, or by enabling it via a Modbus Command,
or via display command. The remote level reference comes from a 4–20 mA analog input. In order to
enable Remote Level Reference the Level Control must be enabled previously.
When Level Control is enabled, there are two options. The control can be configured to maintain a preset
level set point, or it can be configured to “follow” actual level and Nozzle position. If the application always
requires the same level set point when in Level Control, the control should be set up to maintain the
preset level set point. Each time the Level Control mode is enabled, the control will use the preset level
set point. The set point can still be adjusted using the Raise and Lower commands. If a bumpless transfer
is needed or desired when Level Control is enabled, the control should be set to “follow” actual level and
Nozzle position. When Level Control is enabled, the Nozzles will stay where they are at that time.
The level transducer range must also be entered into the Control during the initial configuration. The
“Level at 4 mA” and the “Level at 20 mA” refer to the elevation of the water level when the level
transducer is generating 4 and 20 mA. These high and low limits become the limits of the Level set point,
and they are also used to calculate the Remote Reference for Level Control (if used). The elevations can
be in any unit of measurement, but the units must stay consistent for all other values relating to Pond/Tail
Level control (level feedback signal, level set point, and desired accuracy). The “Maximum Nozzle
Position” and “Minimum Nozzle Position” in Level Control mode must also be configured. This can
prevent the unit from motoring or from overloading in Level Control.
The Level Control algorithm is designed so that several units can be controlling pond/tail level together
without any communication between controls and without fighting each other. However, the consequence
of being able to do this is that the control does not integrate out all error between actual level and the
level reference. By design, the only Nozzle position where there won’t be any level error is the midpoint
between “Maximum Nozzle Position” and “Minimum Nozzle Position”. Therefore, the “Desired Control
Accuracy” must be configured. This desired control accuracy has the same units as the elevation levels
discussed above. If the desired control accuracy is 1 foot, the Control will control the level, but there may
be some error (less than 1 foot) remaining during steady state.
For example, assume the control is configured for Pond Level control. The “Maximum Nozzle Position”
has been configured for 100% and the “Minimum Nozzle Position” has been configured for 20%. The
“Desired Control Accuracy” has been configured for 0.5 feet. If the level error (level set point - actual
level) is greater than +0.5, the Nozzles will close to the minimum Nozzle position (20%). If the level error
is less than –0.5, the Nozzles will open to the maximum Nozzle position (100%). As the actual level
approaches the set point and the error is reduced, the Nozzle position will find an equilibrium value along
the curve shown below. The only time the level error will be zero is when the equilibrium point falls on the
midpoint of the “Minimum” and “Maximum” Nozzle position values.
Released
Содержание 505HT
Страница 23: ...Manual 35116 505HT for Pelton Turbines Woodward 21 Figure 2 2 505D Outline Drawing Released...
Страница 196: ...Manual 35116 505HT for Pelton Turbines Woodward 194 Figure F 10 Deflector Logic Released...
Страница 197: ...Manual 35116 505HT for Pelton Turbines Woodward 195 Revision History New Manual Released...
Страница 198: ...Manual 35116 505HT for Pelton Turbines Woodward 196 Declarations Released...