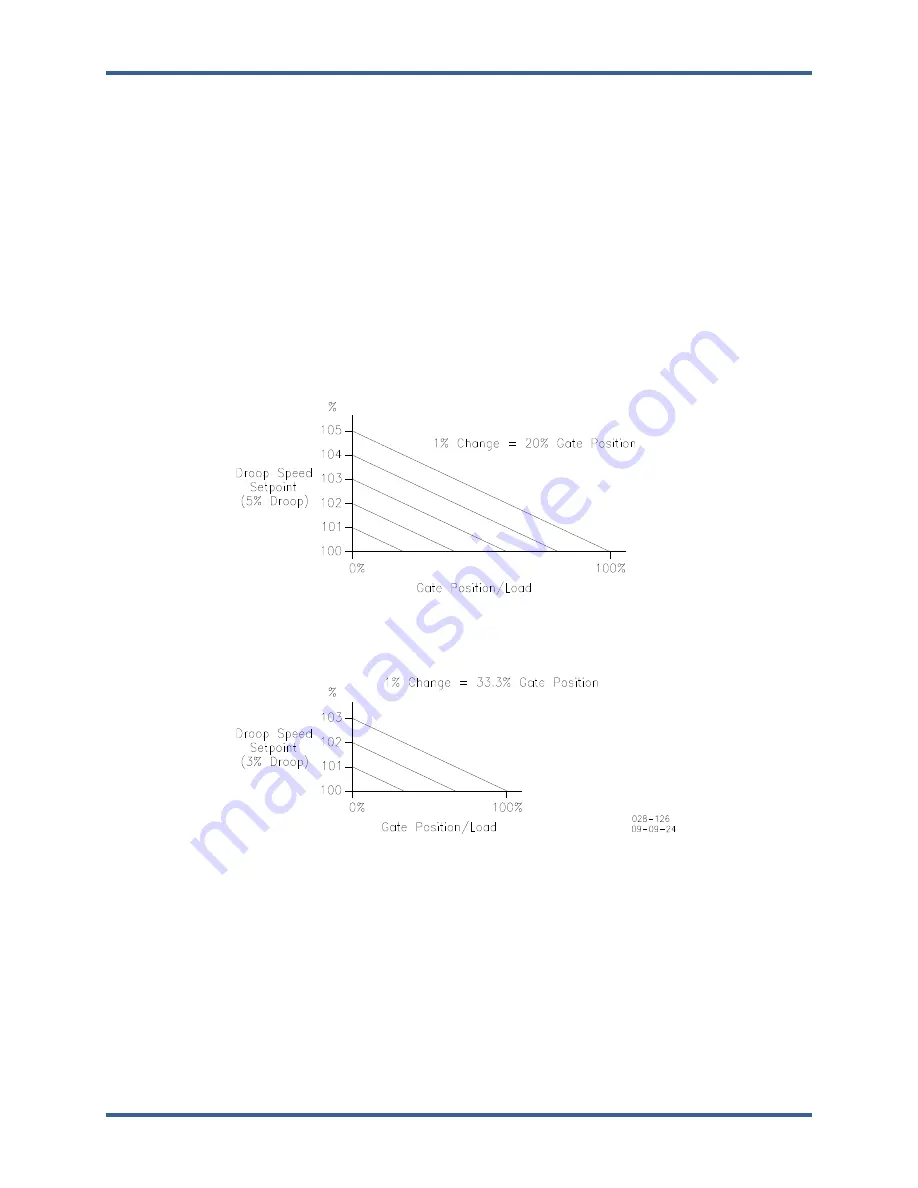
Manual 35116
505HT for Pelton Turbines
Woodward
49
A Remote Speed Reference can be used as well. There are three ways to enable the Remote Speed
Reference: closing a digital input called “Enable Remote Speed”, or by enabling it via a Modbus
Command, or via display command. The remote speed reference comes from a 4–20 mA analog input.
This input is scaled to 0-100% load or actuator position, depending if kW or position droop is enabled. In
order to enable Remote Speed Reference the control must be either in kW or position droop mode
previously. Therefore both Baseload and Level control modes must be disabled in order to put the control
in pure droop mode before enabling remote speed reference. Direct setpoint can also be sent via Modbus
or via display.
For the example below let’s assume that the controller is configured for actuator position droop.
For example, if the speed is fixed at 100% rated speed and the droop is set to 5%, a 1% droop speed set
point change will move the nozzles 20%. If the droop is set to 3%, the nozzles will move 33.3% for a 1%
change in the droop speed set point. The speed is always being monitored and reacted to by the control,
but the control will only respond by an amount determined by the droop setting. For example, at 5% droop
a +0.1% speed change (60.00 Hz to 60.06 Hz) will result in a nozzle position change of 2.0%. At 3%
droop, the same speed fluctuation would result in a nozzle position change of 3.3%.
Figure 3-3. Nozzle Position
The Level Control algorithm calculate a droop speed set point to position the nozzles to a desired
position.
When the generator breaker closes, the default control mode is given by a configurable parameter. The
droop speed set point can be raised and lowered using the Raise/Lower discrete inputs or Modbus. The
Low Limit is 85%, and the High Limit is 100% plus the Droop percentage. For example, at 5% Droop, the
High Limit would be 105%.
When the on-line/Droop PID algorithm is not in control (Manual or Isochronous control), it calculates a
droop speed set point based on the current speed and nozzle position. This provides a bumpless transfer
into On-line/Droop speed control.
Released
Содержание 505HT
Страница 23: ...Manual 35116 505HT for Pelton Turbines Woodward 21 Figure 2 2 505D Outline Drawing Released...
Страница 196: ...Manual 35116 505HT for Pelton Turbines Woodward 194 Figure F 10 Deflector Logic Released...
Страница 197: ...Manual 35116 505HT for Pelton Turbines Woodward 195 Revision History New Manual Released...
Страница 198: ...Manual 35116 505HT for Pelton Turbines Woodward 196 Declarations Released...