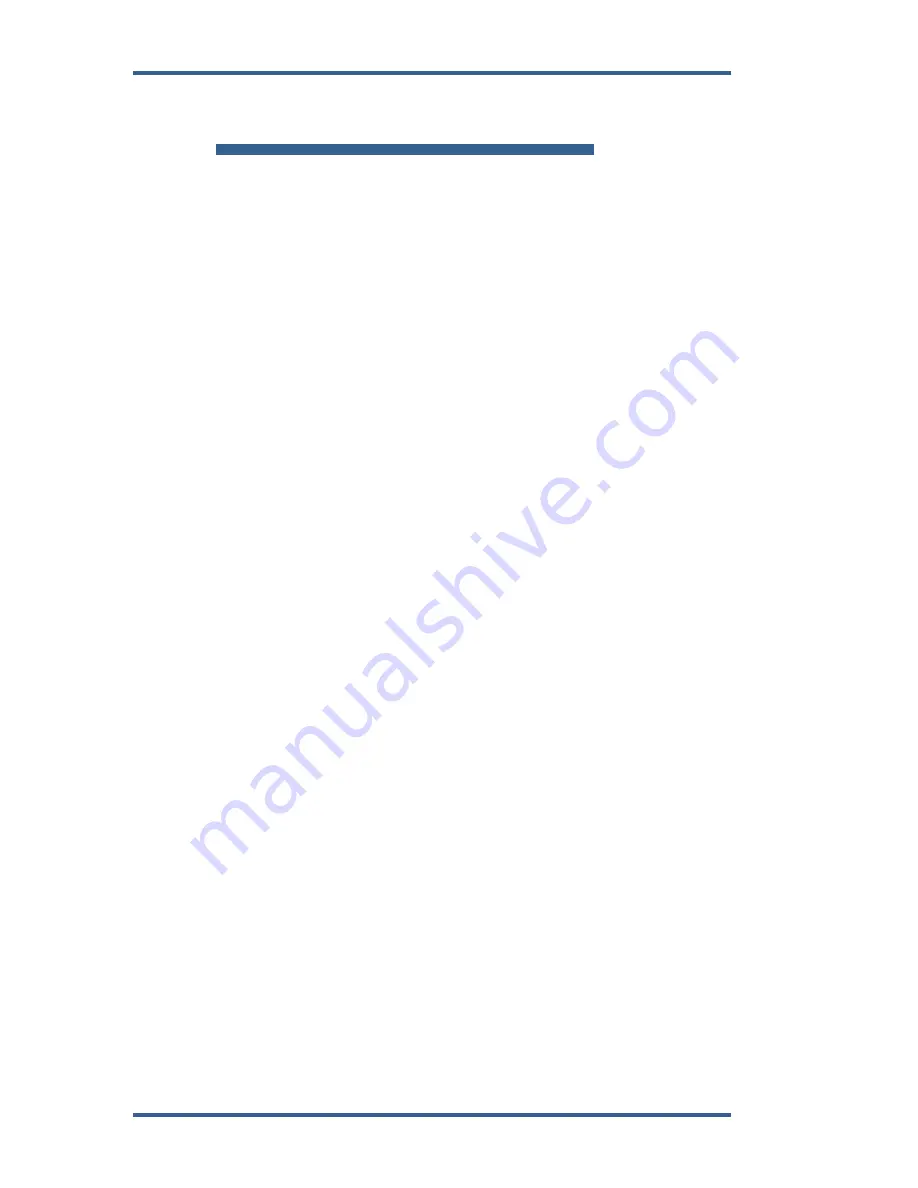
2301D/2301D-EC Digital Control
Manual 26247
72
Woodward
Chapter 5.
Alternative Dynamic Adjustments
Introduction
This procedure, based on the Zeigler-Nichols Method, is an empirical method to
find first-pass settings for gain, reset, and actuator compensation in a PID
controller. First, the controller is set up to act as a proportional-only controller by
removing the effect of the reset and actuator compensation terms. The system is
then bumped and the resulting response is examined. Gain is slowly increased
until the point of marginal stability is found. Once that point is found, some
calculations are done using the period of oscillation and the gain value. The
results of the calculations are gain, reset, and actuator compensation that can be
plugged into the control. This procedure has been used to find a good set of
initial settings for the PID controller. This section also describes adjusting some
other parameters to improve on the initial settings.
Adjustment
Setup
1. Complete
the start-up adjustments described in Chapter 4, Initial Control
Settings. The engine should now be somewhat stable. The settings should
also be saved to EEPROM.
2. Copy
the settings you have right now from 1st dynamics to 2nd dynamics.
Save these values to EEPROM. As you go through the following steps, you
will be trying to find the point of marginal stability. That means that you will be
very close to the point of instability. You are likely to adjust the gain a little bit
too far and go into an unstable condition. When that happens, you will see
the engine start to run away and approach overspeed or stall. The reason the
dynamic settings are copied from 1st dynamics to 2nd dynamics is to allow
you to quickly switch to settings that can control the engine and keep it from
running away or dying. We recommend you use either a jumper or a switch
to allow you to quickly select 2nd dynamics as you are performing this
procedure so that you are confident you always have the ability to control the
engine speed.
3. Connect
a chart recorder to record engine speed. Analog output 1 default
configuration provides a 4–20 mA signal proportional to engine speed. If
necessary, set the CFIG ANALOG OUTPUTS to read engine speed on
another configurable analog output if analog output 1 is being used for
something else.
4. Enable
slight Firing Torsional Filtering by setting the SPEED FILTER
frequency at 15.8 Hz. This setting is found in the Dynamics service menu. A
lower setting may be necessary if firing torsionals are exceptionally high due
to combustion instability, etc. However, a setting below 10 Hz is not
recommended.
Gain, Reset, and Actuator Compensation Adjustments
5. The engine should now be running at no load, idle speed. Start the chart
recorder. Remember, when doing any of these adjustments, you can get the
engine back to running stable by switching in the 2nd dynamics. Select 1st
dynamics now. Reduce the gain by 50%.
Содержание 2301D
Страница 12: ...2301D 2301D EC Digital Control Manual 26247 4 Woodward Figure 1 1a 2301D Outline Drawing Ordinary Locations ...
Страница 13: ...Manual 26247 2301D 2301D EC Digital Control Woodward 5 Figure 1 1b 2301D Outline Drawing Hazardous Locations ...
Страница 14: ...2301D 2301D EC Digital Control Manual 26247 6 Woodward Figure 1 2a 2301D Plant Wiring Diagram sheet 1 ...
Страница 16: ...2301D 2301D EC Digital Control Manual 26247 8 Woodward Figure 1 2c 2301D Plant Wiring Diagram notes ...
Страница 51: ...Manual 26247 2301D 2301D EC Digital Control Woodward 43 Figure 3 4 Typical Transient Response Curves ...
Страница 127: ...Manual 26247 2301D 2301D EC Digital Control Woodward 119 ...
Страница 129: ...Declarations ...