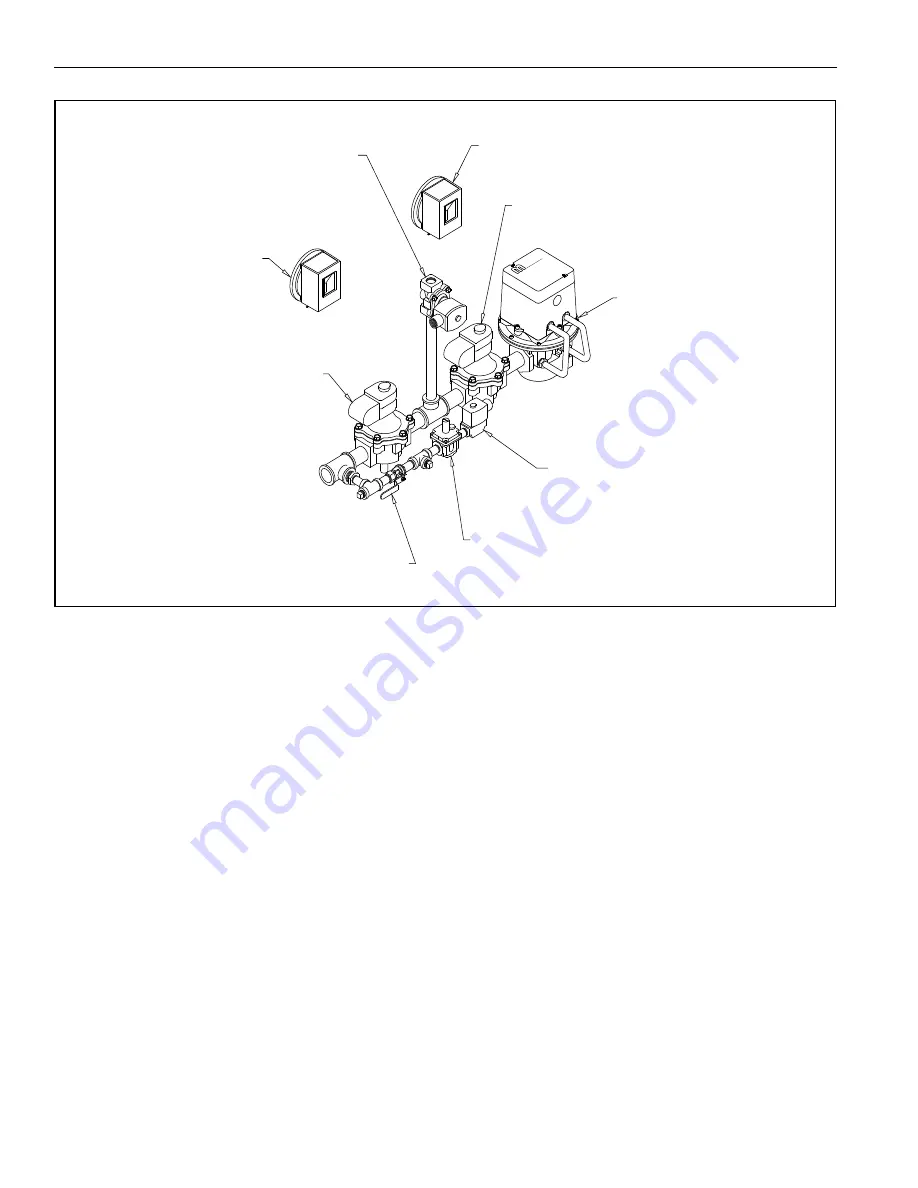
TT-S
ERIES
I
NSTALLATION
, O
PERATION
AND
S
ERVICE
M
ANUAL
82 of 198
FIGURE 69: XL Manifold 1000 - 5000 MBH 1" - 2" NPT
PILOT GAS REGULATOR
CONTROLS THE AMOUNT OF
GAS FLOW TO THE
BURNER'S PILOT TUBE.
POSITION INDICATINGMAIN
GAS SOLENOID VALVE.
OPENS & CLOSES ALLOWING
GAS TO FLOW TO THE BURNER.
PILOT SHUT-OFF COCK
MANUAL SHUT OFF THAT ISOLATES
THE PILOT GAS ASSEMBLY FROM
THE MAIN GAS SUPPLY.
PILOT SOLENOID VALVE.
ALLOWS GAS TO FLOW TO
THE BURNER PILOT.
POSITION INDICATING BLOCK
GAS SOLENOID VALVE.
SECONDARY BACK-UP VALVE TO
PREVENT GAS FROM REACHING
BURNER DURING SHUTDOWN.
METERING VALVE.
CONTROLS THE FLOW OF
GAS TO THE MAIN BURNER
& TO SET THE HIGH & LOW
FIRE ON THE BURNER.
HIGH GAS PRESS. SWITCH
PROTECTS AGAINST EXCESSIVE GAS
PRESSURE
LOW GAS PRESS. SWITCH
PROTECTS AGAINST
INSUFFICIENT GAS
PRESSURE.
VENT VALVE.
VENTS GAS THAT IS TRAPPED
IN THE MANIFOLD BETWEEN
THE MAIN & BLOCK VALVES, ON
SHUTDOWN, TO THE OUTDOORS.
Selec
tra
M
AXITROL
Содержание TT Series
Страница 2: ......
Страница 4: ......
Страница 136: ...TT SERIES INSTALLATION OPERATION AND SERVICE MANUAL 130 of 198 FIGURE 114 Regulator RV61 ...
Страница 167: ...SECTION27 TROUBLESHOOTING 161 of 198 ...
Страница 175: ...SECTION27 TROUBLESHOOTING 169 of 198 ...
Страница 176: ...TT SERIES INSTALLATION OPERATION AND SERVICE MANUAL 170 of 198 27 7 2 Series 94 Field Service Checklist ...
Страница 177: ...SECTION27 TROUBLESHOOTING 171 of 198 ...
Страница 198: ...TT SERIES INSTALLATION OPERATION AND SERVICE MANUAL 192 of 198 ...
Страница 202: ...TT SERIES INSTALLATION OPERATION AND SERVICE MANUAL 196 of 198 ...
Страница 203: ...SECTION 28 THE WEATHER RITE TT SERIES WARRANTY 197 of 198 ...
Страница 204: ...TT SERIES INSTALLATION OPERATION AND SERVICE MANUAL 198 of 198 ...