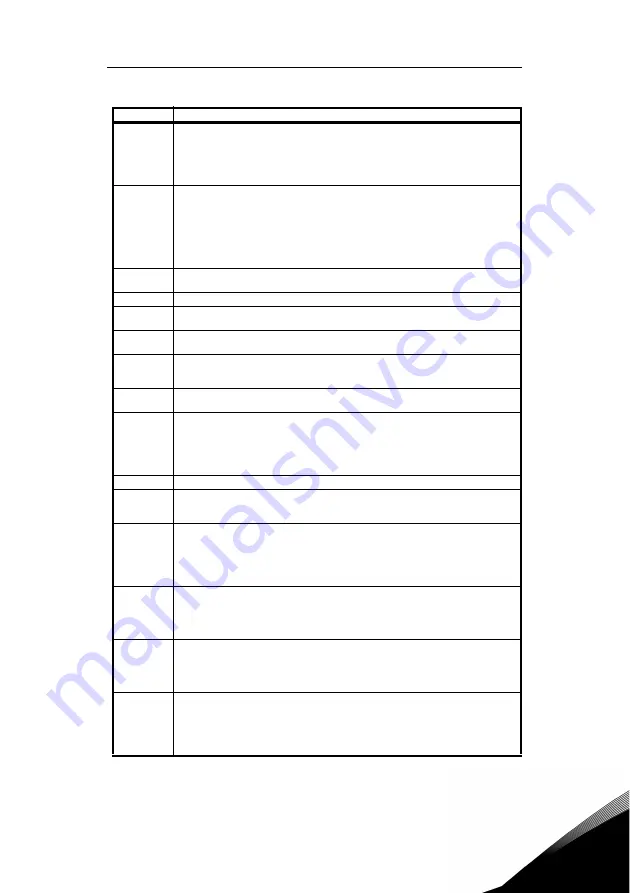
connections
vacon
34
24-hour s358 (0)40 837 1150 • Email: [email protected]
4
Cin+ / Cin–
Current Input.
The default input signal is 4–20 mA, although this range may be adjusted by using parameters
209 (Cin Offset) (which configures an offset for the range) and 210 (Cin Span) (to reduce or
enlarge the range – for example, setting this parameter to 50% results in a range of 4–12 mA).
See page 65 for more information on these parameters.
The burden for this terminal is 50
Ω
.
Vin2
Voltage Input 2, which is used to provide speed references.
The default input signal is 0 to 10 Vdc (the type of input signal is selected with parameter 211
(Vin2 Config); see page 65). Parameters 212 (Vin2 Offset) and 213 (Vin2 Span) may be used to
offset the starting value of the range and the size of the range, respectively; see page 65 for
more information.
If a 0 to 20 mAdc input signal is configured, the burden is 250
Ω
. If a 0 to 10 Vdc input signal is
configured, the input impedance is 475 k
Ω
.
A potentiometer with a range of 1 to 2 k
Ω
is suggested for this input.
Acom
Common for the Analog Inputs and Outputs. Note that while there are three Acom (common)
terminals, they connect to the same electrical point.
+24
A source for positive nominal 24 Vdc voltage, and has a source capacity of 150 mA.
FWD
Forward Direction Selection terminal. This may be connected for two-wire maintained or
three wire momentary operation.
REV
Reverse Direction Selection Terminal. This may be connected for two-wire maintained or
threewire momentary operation.
R/J
Run/Jog Selector. When this terminal is connected to +24 or common (depending upon Active
Logic setting), momentarily connecting either FWD or REV to +24 results in a latched run mode
(3-wire operation).
MOL
Motor Overload input terminal. This requires a N/O or N/C contact for operation, referenced to
+24 or COM, depending on Active Logic setting.
EN
Enable terminal. A jumper is placed between this terminal and the +24 terminal at the factory.
You may replace this with a contact, if desired. The circuit from EN to +24 must be closed for
the drive to operate.
Note that unlike all other terminals, this terminal cannot be configured for “pull-down logic.”
That is, a high input to this terminal is always regarded as true, and must be present for the
drive to operate.
Dcom
Digital Common for use with digital inputs and +24 internal power.
DI1–DI5
Digital inputs.
The function of a digital input is configured by the parameter with the same name as the digital
input (for example, DI2 is configured by parameter 722 (DI2 Configure); see page 81.
NC1
NO1
RC1
The first auxiliary relay.
The function of the relay is set by parameter 705 (Relay 1 Select) (see page 80); the default
setting is for the relay to activate when the motor is at speed.
Terminal NO1 is the normally-open contact, which closes when the relay is activated. Terminal
NC1 is the normally-closed contact, which opens when the relay is activated. Terminal RC1 is
the common terminal.
NC2
NO2
RC2
The second auxiliary relay.
The function of the relay is set by parameter 706 (Relay 2 Select) (see page 80); the default
setting is for the relay to activate when a fault occurs.
Terminal NO2 is the normally-open contact; it will close when the relay is activated. RC2 is
the common terminal.
DO1
DO2
Digital Outputs 1 and 2.
The function of the outputs is set by parameters 707 (DO1 Select) and 708 (DO2 Select).
The default setting for DO1 is Drive Ready; for DO2 it is At Speed. See page 80.
Note that if you are using a high-impedance meter to this terminal, the pull-up resistor value
may need to change. Please consult the factory for more information.
DOP
Open collector transistor output that supplies a pulse train proportional to speed. The
frequency of the output is set by parameter 812 (Freq Ref Output) to either 6x or 48x the running
frequency. The output has a maximum rating of 28 Vdc and requires a pull-up resistor
(4.7 kOhms) if using the drive’s internal supply.
Note that if you are using a high-impedance meter to this terminal, the pull-up resistor value
may need to change. Please consult the factory for more information.
Terminal
Description
Table 10:Description of Vacon 50X Control Terminals
Содержание 50X
Страница 1: ......
Страница 5: ...introduction vacon 4 24 hour support 358 0 40 837 1150 Email vacon vacon com 1 ...
Страница 23: ...receiving and installation vacon 22 24 hour support 358 0 40 837 1150 Email vacon vacon com 3 ...
Страница 30: ...29 vacon connections Tel 358 0 201 2121 Fax 358 0 201 212205 4 Figure 11 Power Terminals Size 4 and 5 ...
Страница 39: ...connections vacon 38 24 hour support 358 0 40 837 1150 Email vacon vacon com 4 ...
Страница 49: ...keypad operation and programming vacon 48 24 hour support 358 0 40 837 1150 Email vacon vacon com 5 ...
Страница 59: ...using macro mode and getting a quick start vacon 58 24 hour support 358 0 40 837 1150 Email vacon vacon com 6 ...
Страница 101: ...vacon 50x parameters vacon 100 24 hour support 358 0 40 837 1150 Email vacon vacon com 7 ...
Страница 107: ...hexadecimal to binary conversion vacon 106 24 hour support 358 0 40 837 1150 Email vacon vacon com 9 ...
Страница 113: ...eu declaration of conformity vacon 112 24 hour support 358 0 40 837 1150 Email vacon vacon com 11 ...
Страница 131: ...summary of vacon 50x parameters vacon 130 24 hour support 358 0 40 837 1150 Email vacon vacon com 12 ...
Страница 132: ......