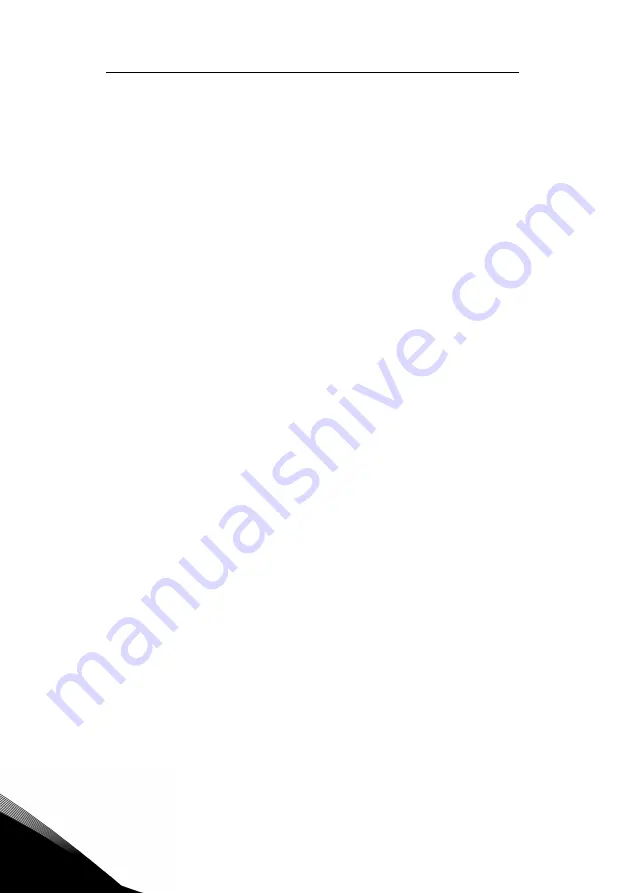
109
vacon
fundamentals of pi control
Tel. +358 (0)201 2121 • Fax +358 (0)201 212205
10
10.2.3 Parameter 852 (PI Prop Gain)
Parameter 852 (PI Prop Gain) is the proportional feedback gain for the process control loop. It determines
the overall effect on the process for an incremental change in the feedback signal.
Generally, when configuring this parameter, you must observe the drive’s response to an incremental
change in the feedback input, and then decide if this response is sufficient.
For example, if the feedback input changes 1 V (or 1 mA), what is the drive’s response? Is it enough or too
much?
10.2.4 Parameter 853 (PI Int Gain)
Parameter 853 (PI Int Gain) is the integral feedback gain for the process control loop. This parameter de-
termines the short-term effects of a change in the feedback signal.
Generally, when configuring this parameter, you must observe the drive’s response to an incremental
change in the feedback input over a certain length of time, and then decide if this response is acceptable.
For example, if the feedback input changed 1 V (or 1 mA) for 5 seconds, what is the drive’s response? Is
it acceptable? Would you prefer to have the drive ignore a change over such a short time period, but still
react to longer time durations (say, 8 to 10 seconds)? (If so, decreasing the integral gain by reducing the
value for parameter 853 would have that effect.)
10.2.5 Parameter 854 (PI Feed Gain)
Parameter 854 (PI Feed Gain) is the feedback scaling factor. It is used to scale the signal supplied by the
transducer — thereby optimizing the effect of the signal on the drive.
10.2.6 Parameter 850 (PI Configure)
Parameter 850 (PI Configure) determines the characteristics of the process control loop – direct-acting
or inverse-acting (also known as reverse-acting), the rate of response (fast or slow), whether feed-for-
ward is enabled, and whether the loop is operated via digital inputs. The following paragraphs discuss
each of these characteristics in more detail:
•
Direct- or inverse-acting loop
In a direct-acting loop, as the process speed increases, the feedback signal will decrease and cause a
corresponding decrease in the process speed as it approaches the regulation point. This type is typically
employed in pump applications where the level control is the process variable.
Conversely, in an inverse-acting loop, as the process speed increases, the feedback signal increases but
causes a corresponding decrease in the process speed as it approaches the regulation point. This type is
typically employed in supply pump applications where the pressure is the process variable.
•
Slow or fast rate of response
A slow rate of response (over 10 s, usually) is most often selected for processes with long time constraints
(for example, thermal and fluid level controls). On the other hand, a fast response rate is utilized for pro-
cesses with short time constraints (such as mechanical systems and pressure loops). Most industrial
systems require a slow rate of response.
•
Whether feed-forward is enabled
Feed-forward is usually enabled when there is very little difference between the process speed and the
feedback signal.
For example, feed-forward is useful in “speed regulation” situations, such as controlling motor speed in
a closed loop. Note that feed-forward should be enabled when attempting to close a speed loop.
Feed-forward is not suited to applications such as pressure regulation systems because generally the
process speed and the process variable are vastly different.
•
Whether PI control is enabled via a digital input
A digital input, when properly configured via the corresponding parameter, may be used to toggle PI con-
trol.
Содержание 50X
Страница 1: ......
Страница 5: ...introduction vacon 4 24 hour support 358 0 40 837 1150 Email vacon vacon com 1 ...
Страница 23: ...receiving and installation vacon 22 24 hour support 358 0 40 837 1150 Email vacon vacon com 3 ...
Страница 30: ...29 vacon connections Tel 358 0 201 2121 Fax 358 0 201 212205 4 Figure 11 Power Terminals Size 4 and 5 ...
Страница 39: ...connections vacon 38 24 hour support 358 0 40 837 1150 Email vacon vacon com 4 ...
Страница 49: ...keypad operation and programming vacon 48 24 hour support 358 0 40 837 1150 Email vacon vacon com 5 ...
Страница 59: ...using macro mode and getting a quick start vacon 58 24 hour support 358 0 40 837 1150 Email vacon vacon com 6 ...
Страница 101: ...vacon 50x parameters vacon 100 24 hour support 358 0 40 837 1150 Email vacon vacon com 7 ...
Страница 107: ...hexadecimal to binary conversion vacon 106 24 hour support 358 0 40 837 1150 Email vacon vacon com 9 ...
Страница 113: ...eu declaration of conformity vacon 112 24 hour support 358 0 40 837 1150 Email vacon vacon com 11 ...
Страница 131: ...summary of vacon 50x parameters vacon 130 24 hour support 358 0 40 837 1150 Email vacon vacon com 12 ...
Страница 132: ......