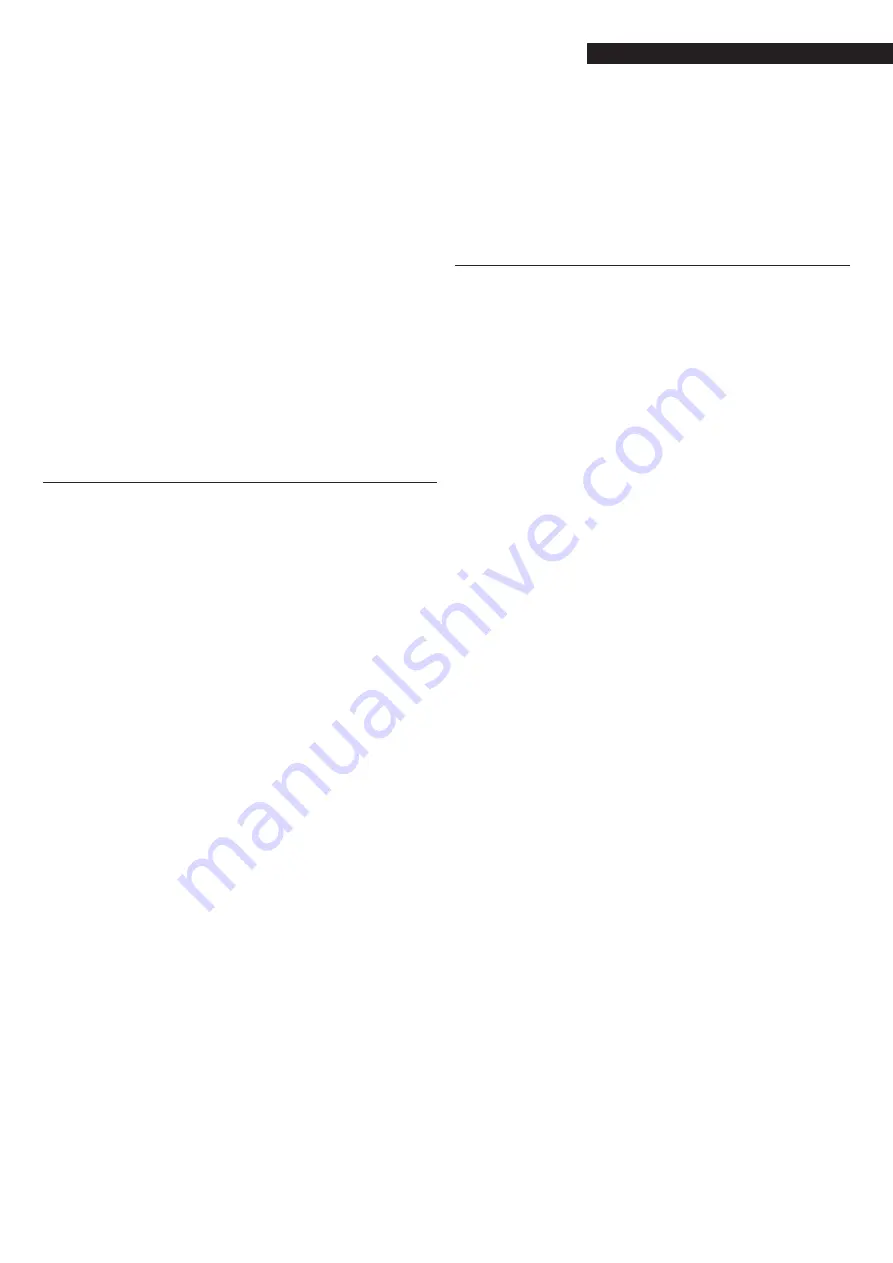
97
GENERAL INFORMATION
0
If a leak occurs or if the refrigerant becomes contaminated
(e.g. by a motor short circuit or BPHE freeze-up), and
before any intervention, remove the complete charge
using a recovery unit and store the refrigerant in mobile
containers. The compressors cannot transfer the whole
refrigerant charge and can be damaged if used to pump-
down. The refrigerant charge should not be transferred to
the high-pressure side.
0
The standard NF E29-795 describes the regulations
permitting conditioning and recovery of halogenated
hydrocarbons under optimum quality conditions for
the products and optimum safety conditions for people,
property and the environment. If any damage is caused
to the equipment, the refrigerant must be changed in
accordance with this standard, or any analysis of the fluid
must be performed by a specialist laboratory.
0
Before any start-up verify that the heat exchange fluid
is compatible with the water circuit materials. Where
additives or other fluids than those recommended by
the manufacturer are used, ensure that these are not
considered gases, and that they are class2, as defined in
directive 97/23EC.
1.2.1
Manufacturer’s recommendations
concerning heat transfer fluids:
− No NH4+ ammonium ions in the water – these are very
harmful to copper. This is one of the most important
factors for the operating life of copper. A content of
several tenths of mg/l will badly corrode the copper over
time.
− Cl-Chloride ions are also harmful to copper with a risk
of perforating corrosion. Keep at a level below 125 mg/l.
− SO4- sulphate ions can cause perforating corrosion if
their content is above 30 mg/l.
− No fluoride ions (<0,1 mg/l)
− No Fe2+ and Fe3+ ions if non—negligible levels of
dissolved oxygen are present. Dissolved iron < 5mg/l
with dissolved oxygen < 5 mg/l.
− Dissolved silicon: Silicon is an acid element of water and
can also lead to corrosion risks. Content < 1mg/l.
− Water hardness: >0,5 mmol/l. Values between 1,0 and
2,5 mmol/l are recommended. This will facilitate scale
deposit that can limit corrosion of copper. Values that
are too high can cause piping blockage over time. A total
alkalimetric titre /TAC) below 100 mg/l is desirable.
− Dissolved oxygen: Avoid any sudden change in
water oxygenation conditions. It is as detrimental to
deoxygenate the water by mixing it with inert gas as
it is to over oxygenate it by mixing it with pure oxygen.
The disturbance of oxygenate conditions encourages
destabilisation of copper hydroxides and enlargement
of particles.
− Electric conductivity 10-600 µS/cm.
− pH: Ideal case pH neutral at 20-25°C (7,5<pH<9).
− To prevent corrosion due to different aeration, if the
system is to be empty for more than 1 month, the heat
transfer fluid circuit should be protected with a blanket
of dry, inert gas (0,5 bar maximum). If the heat transfer
fluid does not meet the recommendations, a nitrogen
blanket must be applied immediately.
− Check the anti-corrosion coatings.
− Must be approved by the original manufactured. Repairs
and modifications which involve a permanent assembly
(welding, soldering, expansion of tubes, etc.) must be
performed by qualified operators following operating
procedures.
9
The units must never be modified to add refrigerants and
oil charging, removal and purging device. These units have
the required openings. Refer to the certified dimensional
drawings.
9
When the unit is subjected to fire, a safety device prevents
rupture due to over-pressure by releasing the refrigerant.
The fluid can then break down into toxic residues when in
contact with flames:
− Stay away from the unit
− Ensure the personnel in charge of extinguishing the
fire are duly warned ad issued with recommendations
− Fire extinguishers appropriate to the system and the
refrigerant type must be easily accessible.
1.2.2
Refrigerants safety considerations
Use safety goggles and safety gloves.
All precautions concerning handing of refrigerant must be
observed in accordance with local regulations.
If a leak occurs or if the refrigerant becomes contaminated (e.g.
by a motor short circuit or BPHE freeze-up), and before any
intervention, remove the complete charge using a recovery unit
and store the refrigerant in mobile containers. The compressors
cannot transfer the whole refrigerant charge and can be
damaged if used to pump-down. The refrigerant charge should
not be transferred to the high-pressure side.
Repair the leak, detect and check the type of refrigerant in the
machine and then recharge the machine/circuit with the total
charges, as indicated on the unit nameplate. Do not top up the
refrigerant charge. Only charge the liquid refrigerant given on
the nameplate ate the liquid line.
Charging any refrigerant other than the original type will impair
machine operation and can even cause irreparable damage
to the compressors. The compressors operating with this
refrigerant type are lubricated with a synthetic polyolester oil.
Do not unweld the refrigerant ductwork or any refrigerant
circuit component or cut these with a torch until all refrigerant
(liquid and vapours) as well as the oil have been removed
from the unit. Traces of vapour should be displaced with dry
nitrogen. Refrigerant in contact with an open flame produces
toxic gases.
Do not siphon refrigerant.
Any accidental release of refrigerant, whether this is caused
by a small leak or significant discharges following the rupture
of a pipe or an unexpected release from a safety valve, may
cause any personnel exposed to experience heart palpitations,
faintness, frostbite and burns. Always take any such event
seriously.
Installer, owners and especially service engineers for these
units must:
− Create a procedure to ensure medical attention is sought
before treating any symptoms;
− Provide first aid equipment, flush the eyes and skin
immediately if splashed with refrigerant and seek
medical attention.
We recommend applying standard EN 378-3 Appendix 3.
Ensure there is sufficient ventilation if the unit is installed in an
enclosed area. In gas from, refrigerant is heavier than air and,
if allowed to accumulate in a confined area, it can reduce the
quantity of oxygen in the air, causing respiratory issues.
The refrigerant used in units in this range is R410A, a high-
pressure fluid (the operating pressure of the unit is greater
than 40 bar).
Special equipment must be used when working on the
refrigerant circuit (pressure gauge, charge transfer equipment,
etc.).
Do not clean the unit with hot water or steam. This could
pressurise the refrigerant.
During any handling, maintenance or service operations, the
technicians involved must be equipped with safety gloves,
glasses, shoes and insulating clothing.
Содержание 20120391
Страница 93: ...93 PANORAMICA DEI PARAMETRI INSTALLAZIONE ...
Страница 169: ...169 ALARM CODES INSTALLATION ...
Страница 185: ...185 OVERVIEW OF THE PARAMETERS INSTALLATION ...
Страница 186: ......
Страница 187: ......