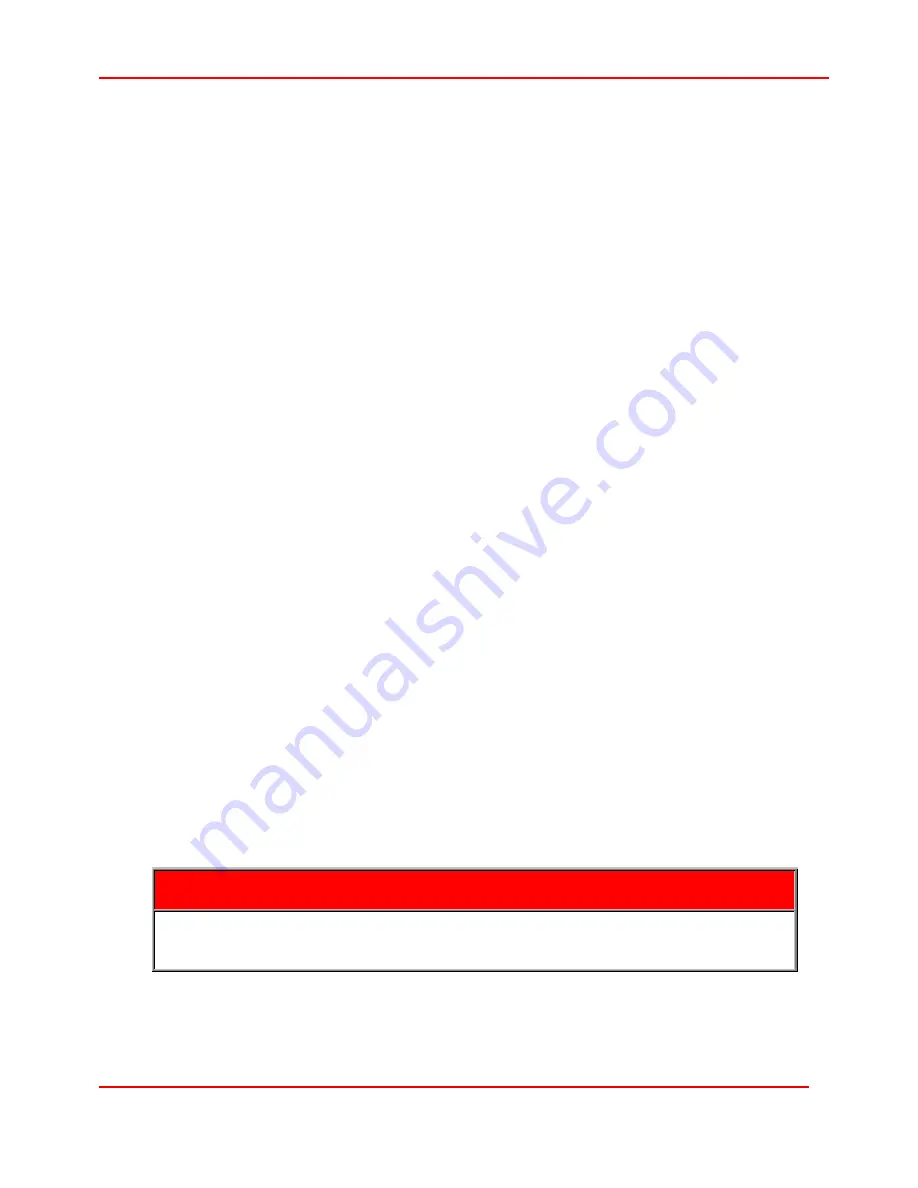
76
CMC TECHNICAL REFERENCE MANUAL
1X36003 Version 2.52
1996-1999 Ingersoll-Rand Company
Date of Issue: 18-Oct-1999
post run timer is also included in the Auto Hot Start logic to de-energize the water solenoid
valves twenty minutes after a compressor stop or trip to allow the oil to cool.
Auto-Cold Start
This option is very similar to Auto-Hot Start with the exception that the compressor starts
with no initial panel power. An additional timer is added to simulate the start button being
pressed and another timer is added to bypass the low oil temperature function on start-up.
One additional solenoid valve is included for instrument air supply. The CONTROL POWER
OFF/ON selector switch label is modified to CONTROL POWER LOCAL/OFF/COLD
START. When in the COLD START position, the compressor is OFF and can be started
through the Auto-Cold Start function. As a safety precaution, an optional strobe light can be
provided to indicate that an automatic start is about to begin.
Remote 4-20 mA Pressure Setpoint
When the REMOTE FUNCTIONS DISABLED/ENABLED selector switch is in the ENABLED
position, the CMC will monitor the specified analog input for pressure setpoint. If this analog
input’s value minus the Pressure Setpoint (from the display) is greater than or equal to the
display’s Pressure Setpoint step value (default 0.1 psi), a remote setpoint change will be
requested. This request will be initiated, as long as there are no analog input error faults for
this channel, and the change made will rounded to the nearest step value (0.1) size. This
methodology prevents the control system from chasing an ever-changing analog input
value.
Steam and Gas Turbine Driven Compressors
The following describes the differences between the motor and turbine driven compressor
logic.
Performance Control
Motor Current, MinLoad and MaxLoad
Steam and gas turbines do not have motor current, MinLoad and MaxLoad operate
differently form the normal motor driven compressor. MinLoad uses an inlet valve position,
instead of amps, to determine when to transition from Inlet Valve Pressure control to Bypass
Valve Pressure control. When in MinLoad, the controller uses this valve position as the
setpoint for the Inlet Valve MinLoad PID loop. Since the controlled variable and the setpoint
variable are identical, the goal of tuning this loop is to get a steady output. The default
parameters will satisfy most all applications. The procedure for determining the MinLoad
point is the same for both motor and turbine driven units, except inlet valve position is
recorded instead of motor amps.
CAUTION
Improperly tuning MinLoad PID values will result in unpredictable compressor
operation. If this situation arises, reset the PID values to the default values.
MaxLoad situations are detected on turbine driven compressors by low speed. The MaxLoad
setpoint is a speed below the rated speed and above the low speed alarm. This speed is
determined by adding an offset to the low speed alarm. This offset is the speed that the
governor can accurately control.