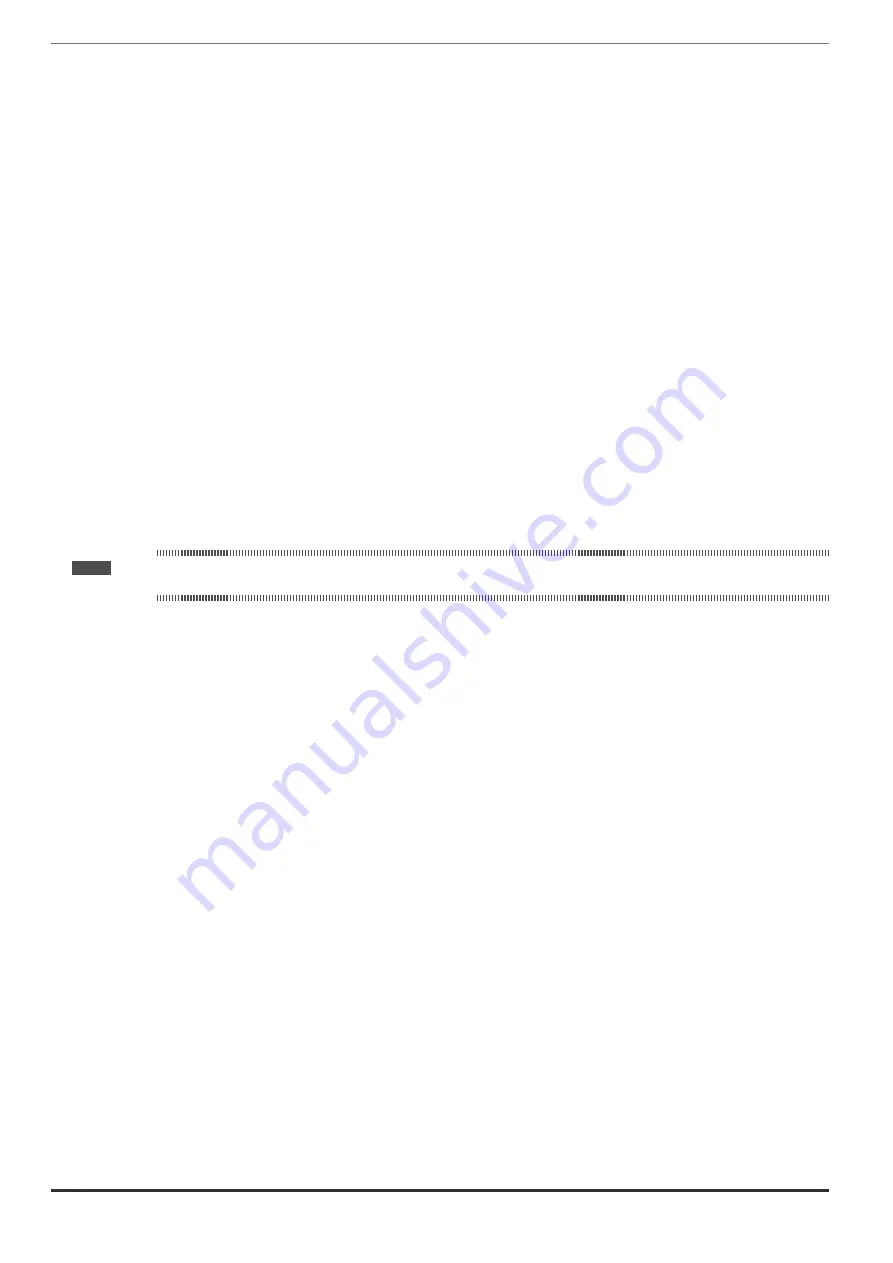
90
ADP200 • Quick installation guide - Specifications and connection
A.3.2 Phasing
In order for the ADP200 Brushless regulation algorithm to function correctly, it is necessary to know the position of
the rotor with respect to the stator power phases. Therefore the 0° position provided by the absolute encoder must
be known with respect to the position of a motor pole and the encoder count direction must match the motor power
phases.
This is called phasing. Phasing can be performed manually, directly by means of the mechanical encoder assembly
position on the motor shaft and on the phases, or using the automatic procedures available in the drive.
Phasing must always be repeated whenever:
- the encoder assembly position is changed
- the phase sequence of the motor power supply connection is changed
- the encoder incremental signal connection is changed
- the encoder absolute signal connection is changed
- the value of the PAR 2008
Pole pairs
parameter is changed
- the value of the PAR 2100
Encoder 1 pulses
parameter is changed
- the drive is replaced (alternatively, download parameters taken from previous drive)
There are two different procedures that can be launched by writing two different parameters:
•
PAR 2190
Autophase rotation
-> rotation phasing:
this procedure must be performed with the motor free to turn and with no load applied.
•
PAR 2192
Autophase still
-> static phasing:
this procedure must be performed with the motor still and brake applied.
Rotation phasing
This procedure is based on the possibility of moving the motor, by a maximum angle of two pole pairs, to find correct
encoder phasing, cross-check the available encoder and motor data and, if the encoder count direction does not match
the phase sequence of the motor power supply, correct it by automatically modifying PAR 2130
Encoder 1 direction
.
Note!
In the case described above, a positive speed reference could generate a rotation in reverse with respect to that defined as positive for the encoder (usually
clockwise), while still ensuring good motor control.
The encoder direction defined as positive can be stored as the positive reference direction by inverting two motor
power phases and repeating the rotation phasing procedure.
If the procedure is terminated without any errors, code 0 is shown on the keypad, otherwise if any differences have
been detected that cannot be corrected by the drive, one of the codes listed in Autotune (phasing),
see chapter 10.3
Messages
, is shown.
Possible faults:
- faults in electric signals not detected with a "
Speed fbk loss [22]
" alarm
- error in the PAR 2008
Pole pairs
parameter setting
- error in the PAR 2100
Encoder 1 pulses
parameter setting.
Static phasing
Using this method, in which the motor cannot move, the encoder and motor data cannot be cross-checked to verify the
matching of parameters or count direction.
This condition must therefore be checked before launching the procedure.