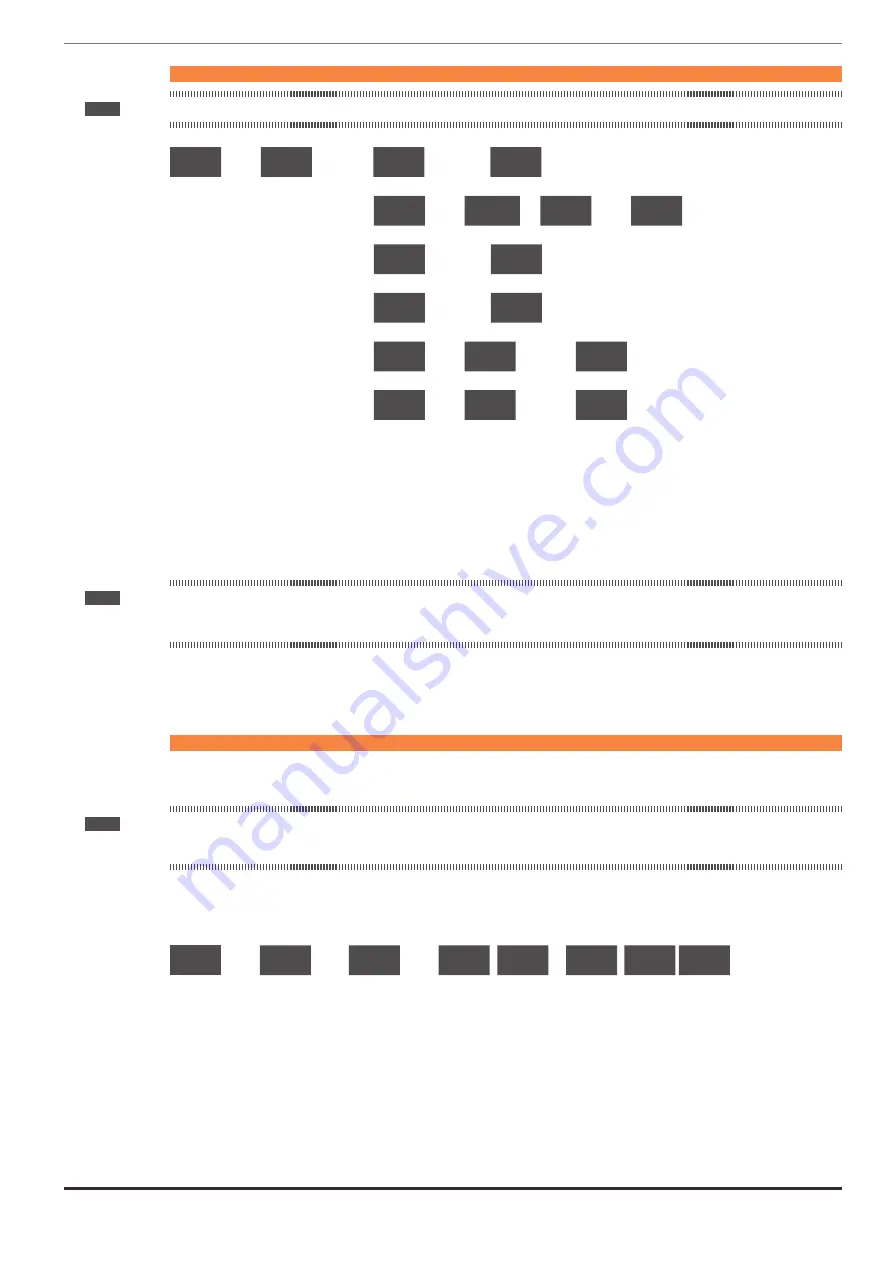
ADP200 • Quick installation guide - Specifications and connection
63
Step 2 - Setting motor parameters
Note!
Def:
The factory (default) setting depends on the size of the drive that is connected. These values refer to the ADP200-2110-...
03.
88.
Enter
Πo
.
t
8.
Enter
20
.
00
.
Enter (x2)
01
.
7
.5
▲
176 v
▼
174 v
Enter
(x3s)
Prg
20
.
02
.
Enter
88
.
8
9 .
6
8
.
88
.
Enter
6
8
.
8
.
8
.
▲
9.7 A
▼
9.5 A
Enter
(x3s)
Prg
20
.
04
.
Enter (x2)
30
.
0
.0
▲
3001 rpm
▼
2999 rpm
Enter
(x3s)
Prg
20
.
08
.
Enter (x2)
00 0
.4
▲
5
▼
4
Enter
(x3s)
Prg
20
.
10
.
Enter
88
.
8
1.
Enter
29
.
8
.
8
▲
1.30Nm/A
▼
1.28Nm/A
Enter
(x3s)
Prg
20
.
12
.
Enter
88
.
8
0
.
Enter
7
4
.
8
.
8
▲
0.75 Wb
▼
0.73 Wb
Enter
(x3s)
Prg
Set the plate data of the motor connected, following the instructions.
Rated voltage [V]:
the rated voltage of the motor indicated on the data plate.
Rated current [A]:
motor rated current; approximately, the value should not be less than 0.3 times the rated current of the drive, output current
class 1 @ 400 V on the data plate of the drive.
Rated speed [rpm]:
motor rated speed; see data plate.
Pole pairs:
Number of motor pole pairs; see data plate.
Torque constant (KT):
(KT) Ratio between the torque generated by the motor and the current required to supply it.
EMF constant:
(KE = KT / √3) Electromotive force constant, which represents the ratio between motor voltage and motor rated speed.
Note!
When data entry is complete the
Take parameters
command is executed automatically (menu 16 MOTOR DATA, PAR: 2020). The motor data entered during
the STARTUP WIZARD procedure are saved in a RAM memory to enable the drive to perform the necessary calculations.
These data are lost if the device is switched off. To save the motor data follow the procedure described in step 9.
At the end of the procedure proceed to step 3. Press the
Prg
and
keys.
Step 3 - Autotune of the motor
The drive carries out the motor autotune procedure (real measurement of motor parameters).
Autotuning may take a few minutes.
Note!
If this operation generates an error message (e.g. Error code 1), check the connections of the power and control circuits (see
step 1
- Connections), check
the motor data settings (see
step 2
- Setting motor parameters) and then repeat the guided Autotune procedure (or, alternatively, select a different type of
procedure (Rotation or Still).
Step 3A - Self-tuning with rotating motor (Autotune rotation)
Use this procedure when the motor is not coupled or the transmission does not represent more than 5% of the load.
This procedure obtains the most accurate data.
rot
.
Enter
20
.
22
Enter
8
E
.
nt
.
Enter
do
.
nE
.
88.8.
0
...
8
6 5
.
ˉ
8
1
.
00
.
do
.
nE
.
(1)
(2)(3)
(4)
(5)
(1) Press the
Enter
key to proceed to the autotune procedure.
(2) Press the
Enter
key to start the autotune procedure.
(3) Enable the drive by connecting terminal 9 (Enable) to terminal 12 (+24 V). To abort this operation, press the
Prg
key.
(4) Once the drive is enabled the autotune procedure starts. This may take a few minutes, depending on the type of
motor being used.
(5) At the end of the procedure the following screen is displayed. After opening the Enable contact, proceed to step 4.
Press the
Prg
x2 and
keys.