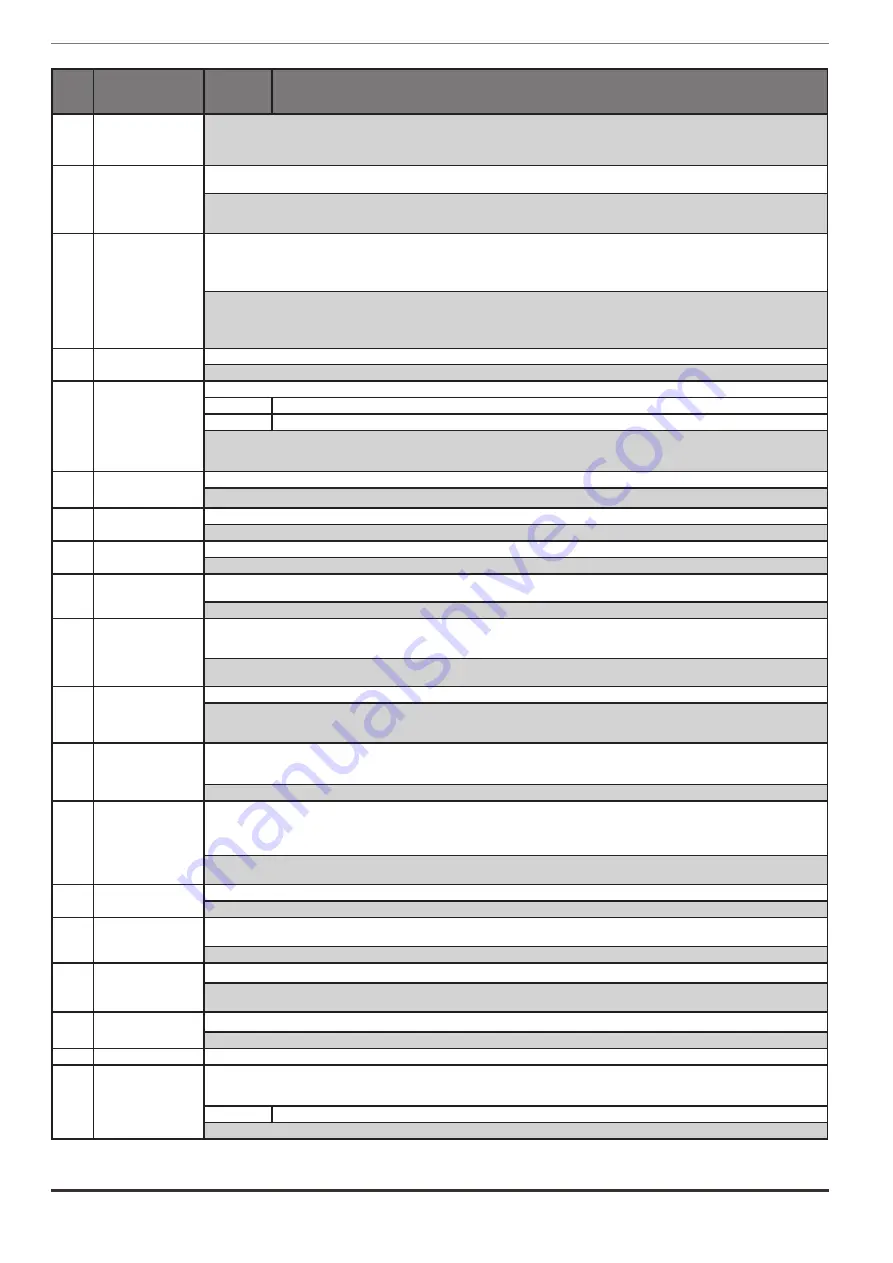
74
ADP200 • Quick installation guide - Specifications and connection
Code
Error message shown
on the display [on the
integrated keypad]
Sub-code
Description
Solution:
- Check that the load is not excessive.
- Check that accelerations are not excessive.
- Check that the overload cycle is within allowed limits.
14
Motor overload [MOL]
Condition:
Motor overload alarm.
The current absorbed during operation is greater than that specified on the motor data plate.
Solution:
- Reduce the motor load.
- Increase the size of the motor.
15
Bres overload [BOL]
Condition:
Braking resistor overload alarm.
The current absorbed by the resistor is greater than the rated current.
The overload threshold of the accumulator of the I²t braking resistor thermal image has been exceeded.
For standard external braking resistor the Max overload (factory set) is 1” service 10% (see Table 5.4.1 on ADP200 QS manual).
Solution:
- Check the size of the braking resistor.
- Check the condition of the braking resistor
Use braking resistor with higher energy value and change the parameters on 22.5 - FUNCTIONS/BRES OVERLOAD menu.
16
Phase loss [PHL]
Condition:
Power phase loss alarm.
Solution:
Check the mains voltage and whether any protections upstream of the drive have been tripped.
17
Opt Bus fault [OPTB]
Condition:
Error in the configuration stage or communication error.
XXX0H-X
If the first digit to the left of “H” in the alarm sub-code is equal to 0, the error relates to a communication problem.
XXXXH-X
If the first digit to the left of “H” in the alarm sub-code is other than 0, the error relates to a configuration problem.
Solution:
For configuration errors, check the configuration of the Bus communication, Bus type, Baudrate, address. parameter setting
For communication errors verify wiring, resistance of terminations, interference immunity, timeout settings.
For further details, please refer to the user guide for the specific bus.
18
Opt 1 IO fault [OPT1]
Condition:
Error in the communication between Regulation and I/O expansion card in slot 1.
Solution:
Check that it has been inserted correctly, see
Appendix section A.1
.
19
Opt 2 IO fault [OPT2]
Condition:
Error in the communication between Regulation and encoder expansion card in slot 2.
Solution:
Check that it has been inserted correctly, see
Appendix section A.1
.
20
Opt Enc fault [OPTE]
Condition:
Error in the communication between Regulation and Encoder feedback card.
Solution:
Check that it has been inserted correctly, see
Appendix section A.1
.
21
External fault [EF]
Condition:
External alarm present.
A digital input has been programmed as an external alarm, but the +24V voltage is not available on the terminal.
Solution:
Check that the terminal screws are tight
22
Speed fbk loss [SFL]
Condition:
Speed feedback loss alarm.
The encoder is not connected, not connected properly or not powered: verify encoder operation by selecting the
PAR 260 Motor speed
parameter in the
MONITOR menu.
Solution:
See parameter 2172
SpdFbkLoss code
for information about the cause of the alarm and chapter 10.2
Speed fbk loss
[22] alarm
23
Overspeed [OS]
Condition:
Motor overspeed alarm. The motor speed exceeds the limits set in the
PAR 4540
parameter.
Solution:
- Limit the speed reference.
- Check that the motor is not driven in overspeed during rotation.
24
Speed ref loss [SRL]
Condition: Speed reference loss alarm;
occurs if the difference between the speed regulator reference and the actual motor speed is more than
100 rpm. This condition occurs because the drive is in the current limit condition. It is only available in the Flux Vect OL and Flux Vect CL mode (see PAR
4550).
Solution:
Check that the load is not excessive.
25
Emg_stop_alarm
[EMGS]
Condition:
Emergency stop alarm.
The Stop key on the keypad was pressed with the PAR 1008
Stop key mode
parameter set to
EmgStop&Alarm.
Active in remote control mode (PAR 1012=1) both by using “Terminals” command or “Digital” commands and, in local control mode (PAR 1012=0) by
using “Terminals” command.
Solution:
Eliminate the reason for which the Stop key on the keypad was pressed and reset the drive.
26
Power down [PD]
Condition:
The drive was enabled with no supply voltage at the power section.
Solution:
Check the drive power supply
27-28-
29
Not Used
30
Motor pre OT [PROT]
Condition:
Motor overtemperature prealarm. % value of threshold compared to PAR 4532
MotorOT thr,
Solution:
Value set too low for duty cycle
31
Mot phase loss [PHLO]
Condition: Output phase loss.
Solution:
Check Drive/motor connection.
32
Not Used
33 ... 40
Plc1 fault [PL01]
...
Plc8 fault [PL08]
Condition:
Enabled application developed in the IEC 61131-3 environment has found the conditions for generating this specific alarm to be true. The mean-
ing of the alarm depends on the type of application. For more information, refer to the documentation concerning the specific application..
XXXXH-X
The XXXXH-X code indicates the reason for the error: make a note of this to discuss it with the service centre.
Solution:
Refer to the documentation concerning the enabled application.