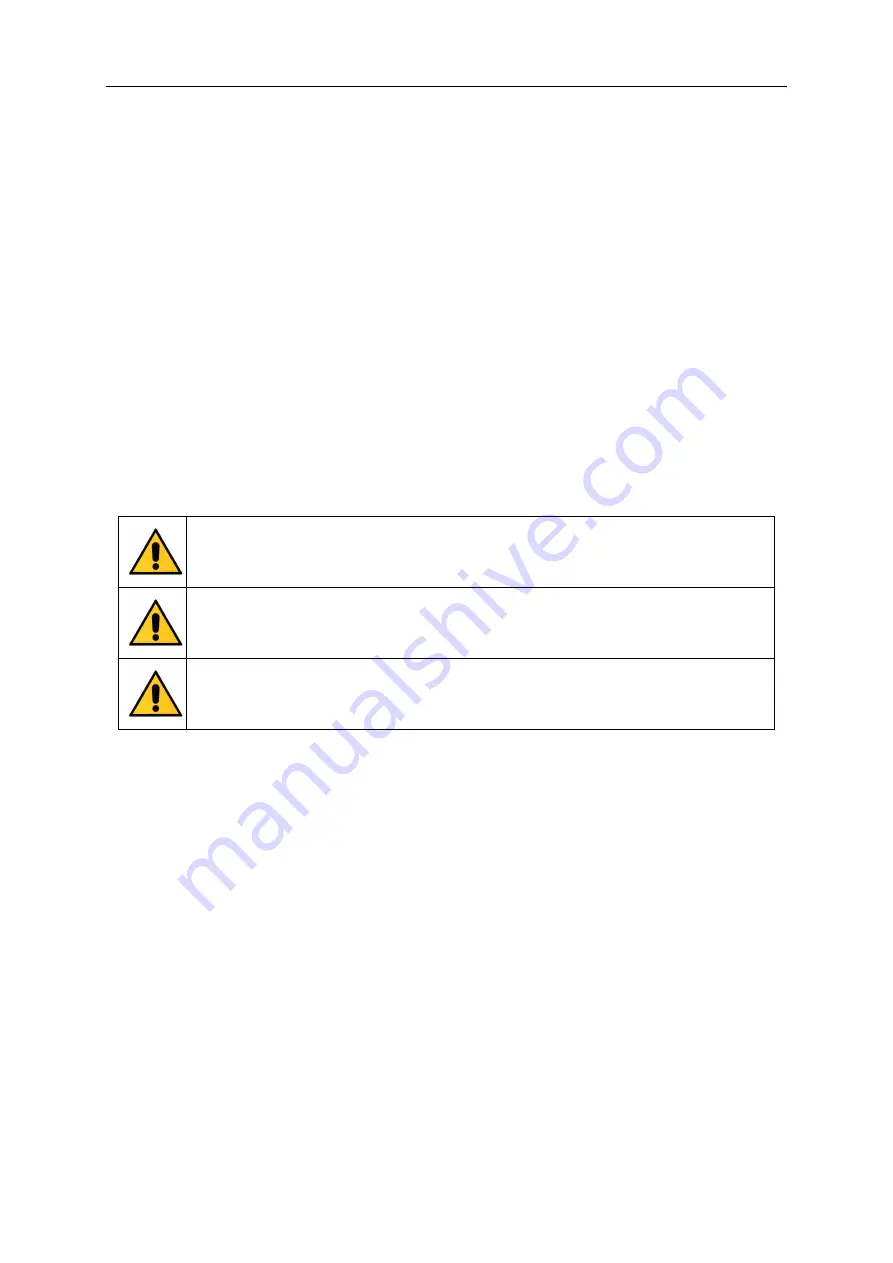
Electrical Operation and Maintenance Manual for Control Cabinet of EC2-S Industrial Robot
41
stop button of the control cabinet, and the external emergency stop button. The function of the emergency
stop button is to quickly cut off the output of the driver and make the robot stop moving immediately. Turn
the emergency stop button clockwise to release the emergency stop button.
Emergency stop is a state that takes precedence over all other robot control operations and will cause
all controlled danger stops. The motor power supply is removed from the robot starter and remains
effective until reset, and can only be reset by manual operation. The emergency stop state means that all
power supplies except for the manual brake release circuit are disconnected from the robot. You must
perform the restoration procedure, which is to reset the emergency stop button and clear the alarm to
resume normal operation. The robot system can be configured to cause an emergency stop to produce any
of the following effects:
• 0 stop, which stops the robot operation immediately by stopping the motor power supply.
• 1 stop, which stops the robot operation while keeping the motor powered in order to maintain the
robot path. After completion, the motor power supply stops.
The default setting is 0 stop. However, since 1 stop can avoid unnecessary wear of the robot and the
additional operations required to restore the system to production, it is recommended to choose 1 stop.
Attention
The emergency stop function can only be used for its specific purpose and
established conditions.
Attention
The emergency stop function is used to stop the equipment immediately in case of an
emergency.
Attention
Emergency stop should not be used for normal program stop because it may cause
additional unnecessary wear and tear on the robot.
When you need to connect an external emergency stop, refer to the emergency stop interface definition
table to pull out the factory-preconnected short wire from the X13 port of the external emergency stop
terminal on the panel, and crimp the external emergency stop wiring harness that needs to be connected and
insert it into the corresponding port. Yes; EMG-AP, EMG-AM and EMG-BP, EMG-BM are a pair of
dual-loop external emergency stop channels.
When the emergency stop of the robot is triggered, the safety signal of the robot can be output to the
peripheral equipment through the X13 external safety signal terminal. The emergency stop terminal block
outside the control cabinet is EMGO-AP and EMGO-AM, EMGO-BP and EMGO-BM. They are a pair of
double-circuit output contacts in emergency stop state. Users can wire according to their needs (It is
recommended that the wire diameter is 0.3mm²or more).
Содержание EC2-S
Страница 2: ......
Страница 4: ......
Страница 10: ......
Страница 34: ...EFORT INTELLIGENT EQUIPMENT CO LTD 24 15 19 21 front left side panel bottom plate 16 17 20 18...
Страница 84: ...EFORT INTELLIGENT EQUIPMENT CO LTD 74...
Страница 85: ...Electrical Operation and Maintenance Manual for Control Cabinet of EC2 S Industrial Robot 75...
Страница 86: ...EFORT INTELLIGENT EQUIPMENT CO LTD 76...
Страница 87: ...Electrical Operation and Maintenance Manual for Control Cabinet of EC2 S Industrial Robot 77...
Страница 88: ...EFORT INTELLIGENT EQUIPMENT CO LTD 78...
Страница 89: ...Electrical Operation and Maintenance Manual for Control Cabinet of EC2 S Industrial Robot 79...
Страница 90: ...EFORT INTELLIGENT EQUIPMENT CO LTD 80...
Страница 91: ...Electrical Operation and Maintenance Manual for Control Cabinet of EC2 S Industrial Robot 81...
Страница 92: ...EFORT INTELLIGENT EQUIPMENT CO LTD 82...
Страница 120: ......