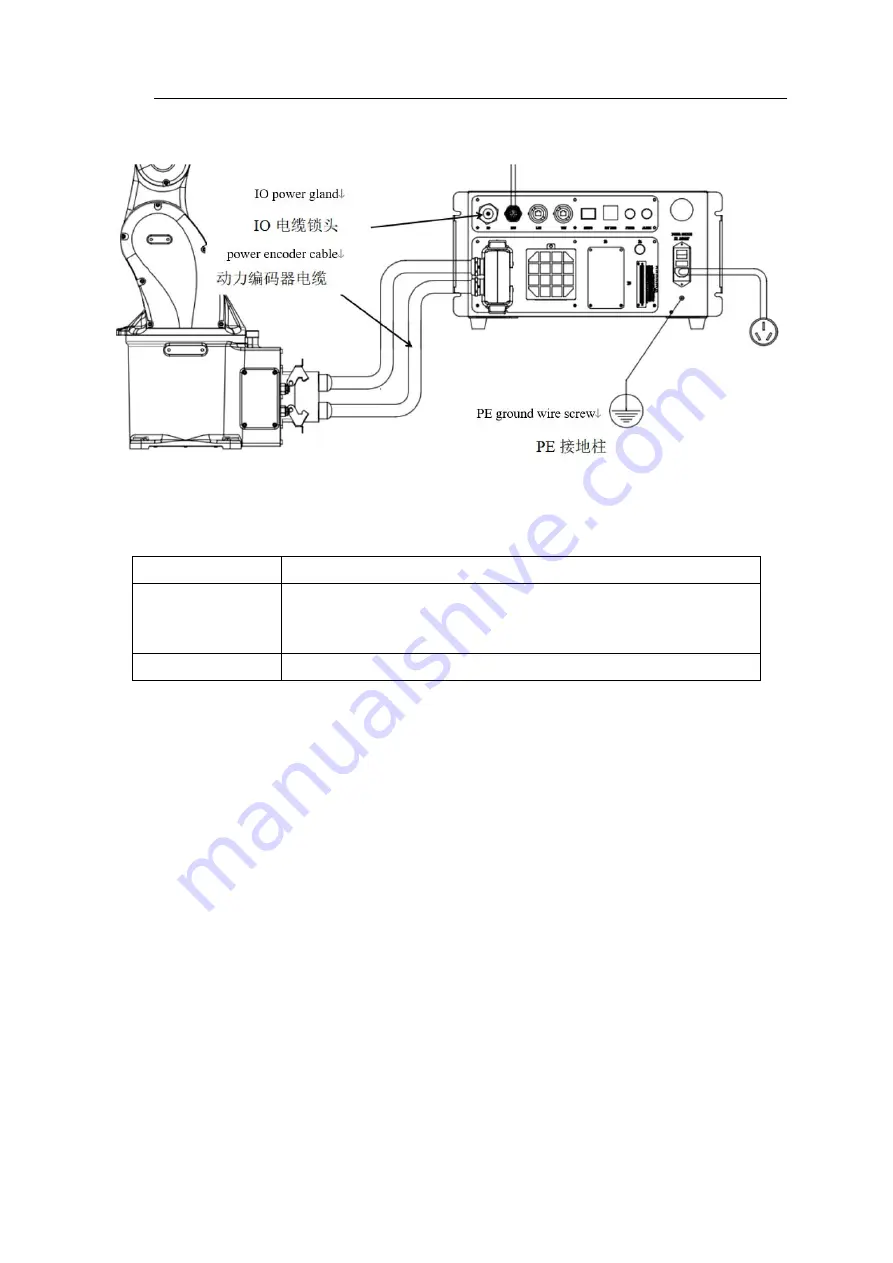
EFORT INTELLIGENT EQUIPMENT CO.,LTD
20
Fig. 2-5 Location of Connectors
Table 2-6 Cable Description
Cable Type
Description
power encoder cable Transfer drive power from the drive device in the control cabinet to the
motor of the robot.
Transmit the encoder data to the serial measurement circuit board.
ground wire
Connect robot body to control cabinet.
The left side of the control cabinet is equipped with one M25*1.5 cable gland, which has been blocked
with a sealing plug before leaving the factory. Users must ensure its airtightness, or the overall airtightness
of the control cabinet will be damaged.
2.4.3 Emergency Stop
Emergency stop buttons are spread on the teach pendant, control cabinet and external devices. They
function to cut off the output of the driver quickly and stop the robot’s movement immediately. Turn the
emergency button clockwise to release it.
Emergency stop prioritizes all control operations and calls stops for all controllable dangers. It cuts the
power supply of the motor from the robot starter and remains effective until being reset, which can only be
activated manually. It also means to disconnect robot from all power supplies except for releasing circuit by
manual brake. To resume normal operation, restoration procedures must be performed, which include
resetting the emergency button and clearing the alarm. Emergency stop can generate any of the following
effects:
• 0 stop, stop the robot operation immediately by cutting off the power supply of the motor.
• 1 stop, stop the robot operation while keeping the motor powered in order to maintain the robot
routing until it is completed.
Содержание EC2-S
Страница 2: ......
Страница 4: ......
Страница 10: ......
Страница 34: ...EFORT INTELLIGENT EQUIPMENT CO LTD 24 15 19 21 front left side panel bottom plate 16 17 20 18...
Страница 84: ...EFORT INTELLIGENT EQUIPMENT CO LTD 74...
Страница 85: ...Electrical Operation and Maintenance Manual for Control Cabinet of EC2 S Industrial Robot 75...
Страница 86: ...EFORT INTELLIGENT EQUIPMENT CO LTD 76...
Страница 87: ...Electrical Operation and Maintenance Manual for Control Cabinet of EC2 S Industrial Robot 77...
Страница 88: ...EFORT INTELLIGENT EQUIPMENT CO LTD 78...
Страница 89: ...Electrical Operation and Maintenance Manual for Control Cabinet of EC2 S Industrial Robot 79...
Страница 90: ...EFORT INTELLIGENT EQUIPMENT CO LTD 80...
Страница 91: ...Electrical Operation and Maintenance Manual for Control Cabinet of EC2 S Industrial Robot 81...
Страница 92: ...EFORT INTELLIGENT EQUIPMENT CO LTD 82...
Страница 120: ......