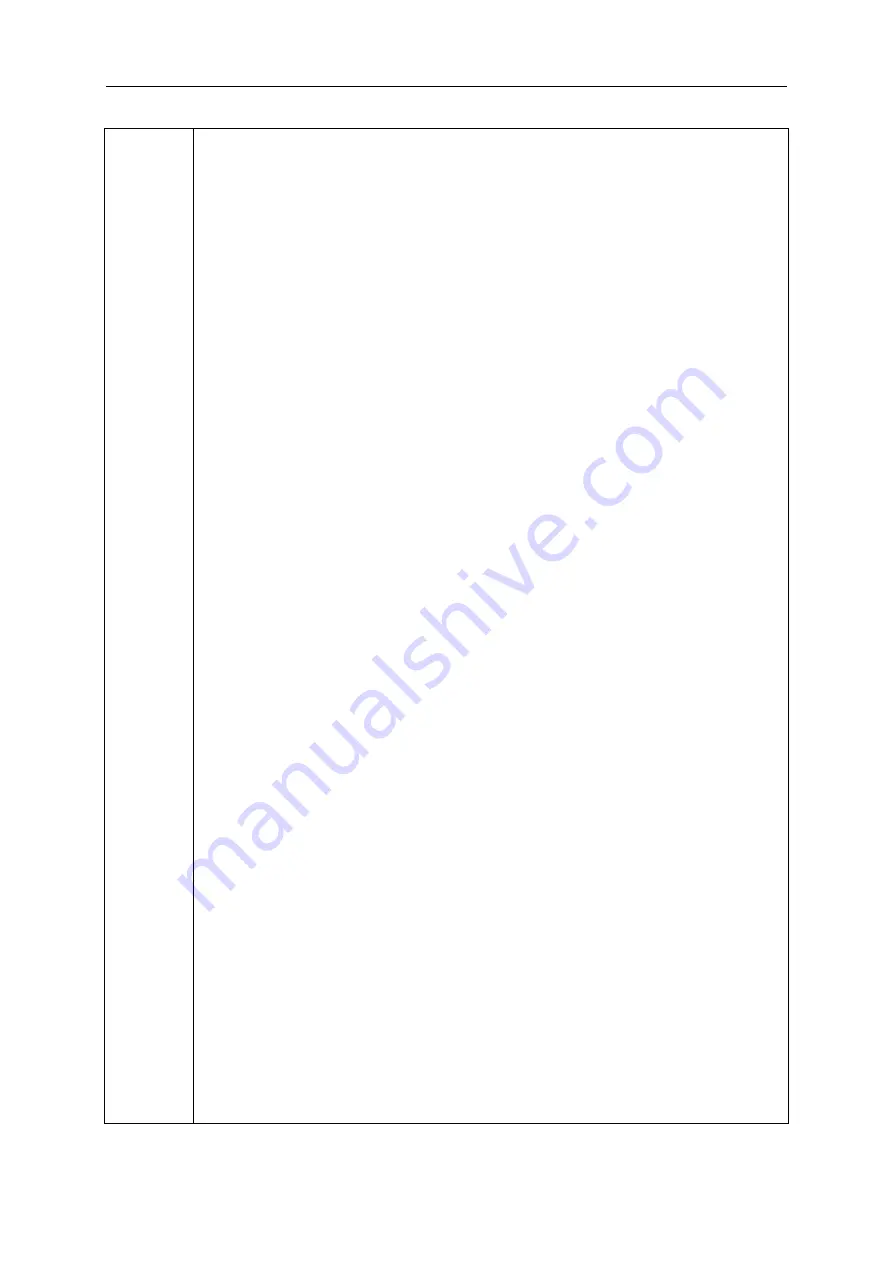
Electrical Operation and Maintenance Manual for Control Cabinet of EC2-S Industrial Robot
7
the robot.
3. Teaching should be administered by one operator and one supervisor, who bears the
responsibility of safety supervision. Confirm signals, such as "start work", before
teaching.
4. Before entering the safety fence, the operator must turn the teaching switch on the
teach pendant to manual to prevent accidental switch of the control cabinet to
automatic mode. Once the robot makes any abnormal movement, the emergency stop
switch must be immediately pressed and robot exits the work area from the preset
evacuation route.
5. Please install an emergency stop switch which enables the supervisor to monitor the
overall robot movement outside the fence. Once the robot makes incorrect movement,
the supervisor must be able to press the switch very conveniently to stop the robot
immediately. In addition, if you need to restart the robot after an emergency stop,
please reset and restart the manual operation outside the safety fence. The operator
and the supervisor must be specially trained and qualified personnel.
6. Please clearly mark teaching is in progress to prevent other people from making
wrong operations on the control cabinet, operation panel, teaching pendant, or any
robot system devices.
7. Before confirming the trajectory and teaching data, please clear all the personnel
and obstacles left within the safety fence and around the robot. The confirmation work
should be done outside the safety fence. The speed of the robot should be equal to or
less than safety speed (250mm/s) until being confirmed normal.
8. If robot needs to be restarted after an emergency stop, please reset and restart
manually outside the safety fence. At the same time, confirm all safety conditions are
met and no humans or obstacles left are around the robot or within the safety fence.
9. During teaching, please confirm the motion range of the robot. Approaching the
underside of the robot is prohibited and may pose risks causing accidents. It’s also
worth noticing that it is forbidden to approach the robot arms to prevent risks of
workpiece falling when robot’s claws grip workpieces.
10. For safety concern, the maximum speed of the robot is limited to 250mm/s (safe
operating speed) in teaching or inspection mode. However, after teaching is completed
or robot is recovered from errors, the operator should set the speed as low as possible
in verifying teaching data.
11. Both the operator and the supervisor should continuously monitor the robot for
abnormal movements, possible collisions and squeezing points on and around the
robot. Meanwhile, please confirm the safe passage for the operator is clear in case of
emergency evacuation.
12. Please set the robot's software limit beyond the robot’s motion range after teaching
is completed. Refer to the EFORT Industrial Robot Operation Manual for the setting.
Содержание EC2-S
Страница 2: ......
Страница 4: ......
Страница 10: ......
Страница 34: ...EFORT INTELLIGENT EQUIPMENT CO LTD 24 15 19 21 front left side panel bottom plate 16 17 20 18...
Страница 84: ...EFORT INTELLIGENT EQUIPMENT CO LTD 74...
Страница 85: ...Electrical Operation and Maintenance Manual for Control Cabinet of EC2 S Industrial Robot 75...
Страница 86: ...EFORT INTELLIGENT EQUIPMENT CO LTD 76...
Страница 87: ...Electrical Operation and Maintenance Manual for Control Cabinet of EC2 S Industrial Robot 77...
Страница 88: ...EFORT INTELLIGENT EQUIPMENT CO LTD 78...
Страница 89: ...Electrical Operation and Maintenance Manual for Control Cabinet of EC2 S Industrial Robot 79...
Страница 90: ...EFORT INTELLIGENT EQUIPMENT CO LTD 80...
Страница 91: ...Electrical Operation and Maintenance Manual for Control Cabinet of EC2 S Industrial Robot 81...
Страница 92: ...EFORT INTELLIGENT EQUIPMENT CO LTD 82...
Страница 120: ......