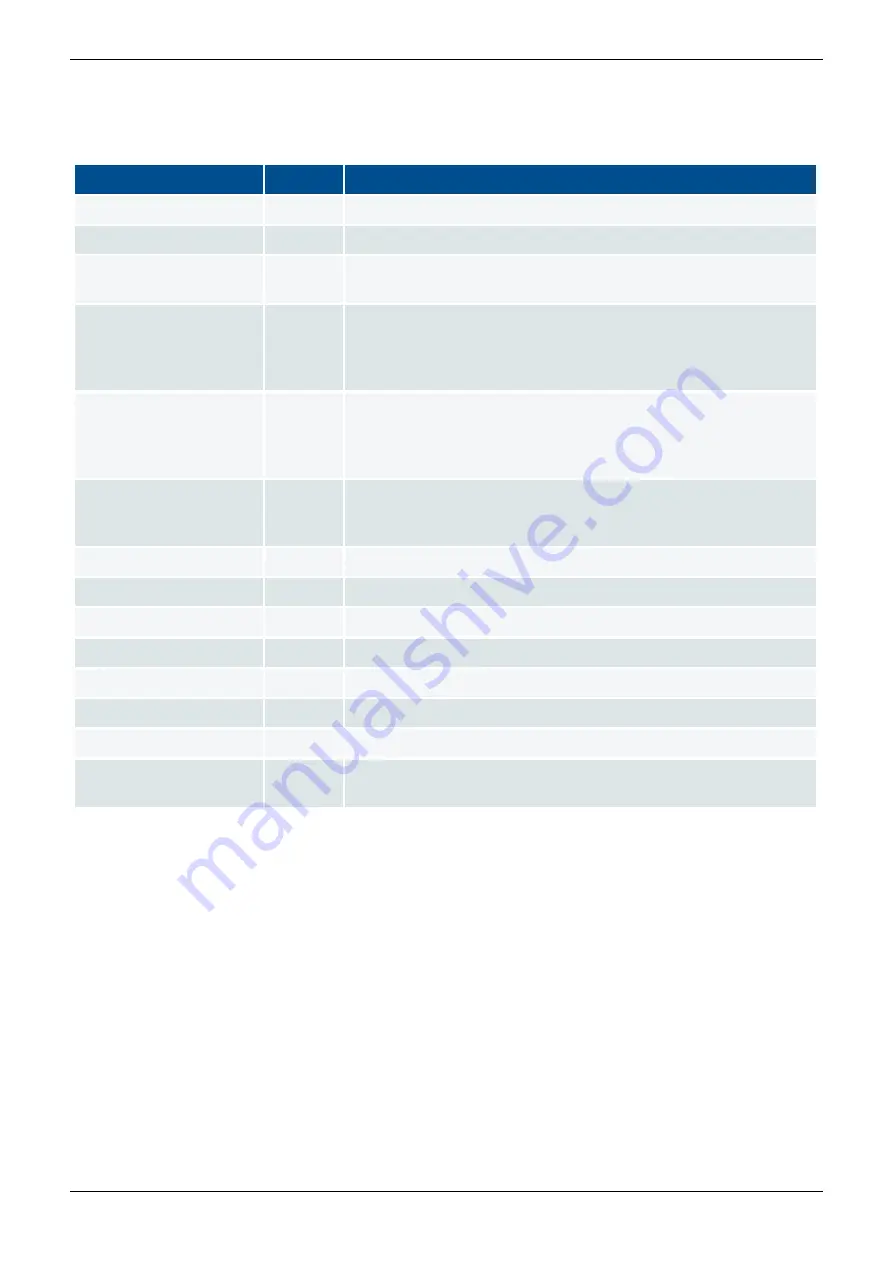
IMD 100 Integration manual 4189360015 Rev. G
IMD configuration
Page 85 of 243
8.4.1.1 Example of Servo configuration
The following example show configuration when five ultra-cap modules of 90 V DC are used as safe
energy, and 3 x 400 V AC is used as the mains input.
Parameter
Value
Description
Axis label
BL-1
Identifying name for the IMD. Here BL(ade)-1 is used.
Mains voltage
400
Standard 3 x 400 V AC is used
DC-link Vmax
789
Default DC-link Vmax is used since the mains voltage is not
above 440 V AC.
DC-link Vlow
300
If the DC-link voltage is down to 300 V DC, it means that the
ultra-caps are also at 300 V DC which is far under their
nominal 450 V DC. Therefore, a safety run should be started,
and the mains connected if it is disconnected.
DC-link Vmin
150
The ultra-cap modules can tolerate depletion to a
comparatively low point. Under this voltage, output current will
be too high, and for IMDs with internal power supply, a risk
that the power supply will shut down.
SE Vlow
400
This threshold is used to give a warning that something in the
safe energy system is not as it is supposed to be (under
normal circumstances).
LVRT timer
Disabled No automatic safety run is performed after a mains failure
Ballast-P
300
The standard built-in ballast resistor is used.
Ballast-R
20
The standard built-in ballast resistor is used.
Motor PWM frequency
4 kHz
4 kHz is selected in order to minimize switching losses
I max extended
Disable
There is no need for the extra current
SSI encoder type
Multi-t.
Multi-turn encoder is used
Pt100 filter
Stand.
No extra cycle time is needed
Char. err. trip S-chain
Enable
Charger error will be escalated to IMD error after Charger
timeout, causing safety-chain trip and safety run.