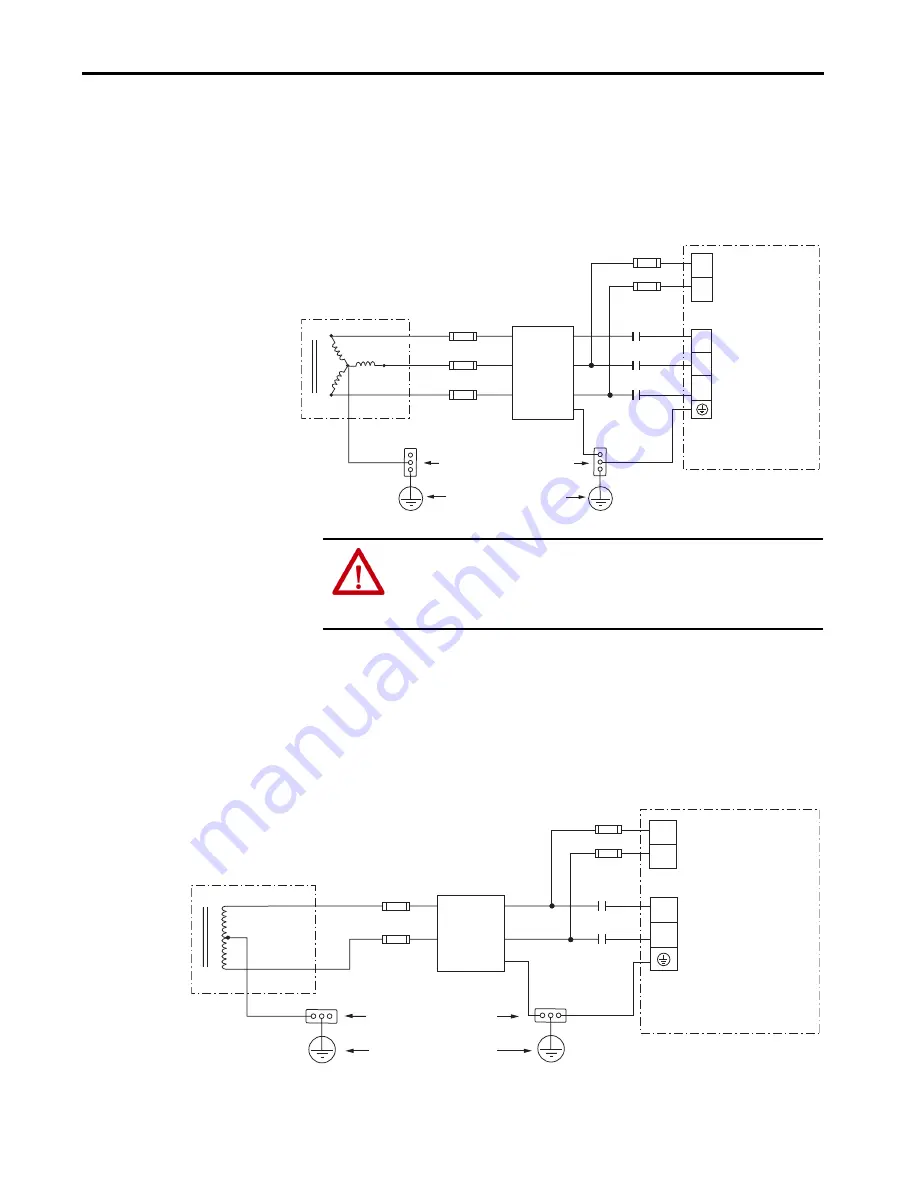
Rockwell Automation Publication 2198-UM004A-EN-P - October 2019
73
Connect the Kinetix 5100 Drive System
Chapter 4
Three-phase Power Wired to Three-phase Drives
These examples illustrate grounded three-phase power that is wired to three-
phase Kinetix 5100 drives when phase-to-phase voltage is within drive
specifications.
Figure 47 - Three-phase (200…230V) Grounded Power Configuration (wye secondary)
Single-phase Power Wired to Single-phase Drives
These examples illustrate grounded single-phase power that is wired to single-
phase Kinetix 5100 drives when phase-to-phase voltage is within drive
specifications.
Figure 48 - Single-phase (200…230V) Grounded Power Configuration
Reducing the transformer output reduces motor speed. Feeder and branch short-circuit protection is not illustrated.
L3
L2
L1
L3
L2
L1
E
L3
L2
L1
L3
L2
L1
2198-E
xxxx
-ERS
Servo Drives
L1C
L2C
Transformer (wye) Secondary
Mains AC Input
Power Connector
Bonded Cabinet Ground Bus
Ground Grid or
Power Distribution Ground
AC Line
Filter
Circuit
Protection
Feeder and branch short-circuit
protection is not illustrated.
M1
Contactor
Control AC Input
Power Connector
Circuit
Protection
ATTENTION:
For the 230V Kinetix 5100 drives to meet proper voltage creepage
and clearance requirements, each phase voltage to ground must be less than or
equal to 253V AC rms. This means that the power system must use center-
grounded wye secondary configuration for 230V AC mains.
L2
L1
L2
L1
L2
L1
L2
L1
E
L1C
L2C
Transformer Secondary
Bonded Cabinet Ground Bus
Ground Grid or
Power Distribution Ground
AC Line
Filter
200…230V AC
Output
Circuit
Protection
M1
Contactor
Circuit
Protection
Mains AC Input
Power Connector
Control AC Input
Power Connector
2198-E1004-ERS, 2198-E1007-ERS,
2198-E1015-ERS, and 2198-E1020-ERS
Drives with Single-phase Operation
Содержание Kinetix 5100 2198-E1004-ERS
Страница 114: ...114 Rockwell Automation Publication 2198 UM004A EN P October 2019 Chapter 6 Set Up EtherNet IP Communication Notes ...
Страница 402: ...402 Rockwell Automation Publication 2198 UM004A EN P October 2019 Chapter 14 Absolute Position Recovery Notes ...
Страница 484: ...484 Rockwell Automation Publication 2198 UM004A EN P October 2019 Appendix C Use Add On Instructions Notes ...
Страница 488: ...488 Rockwell Automation Publication 2198 UM004A EN P October 2019 Appendix D Full Closed Loop Control Notes ...
Страница 499: ......