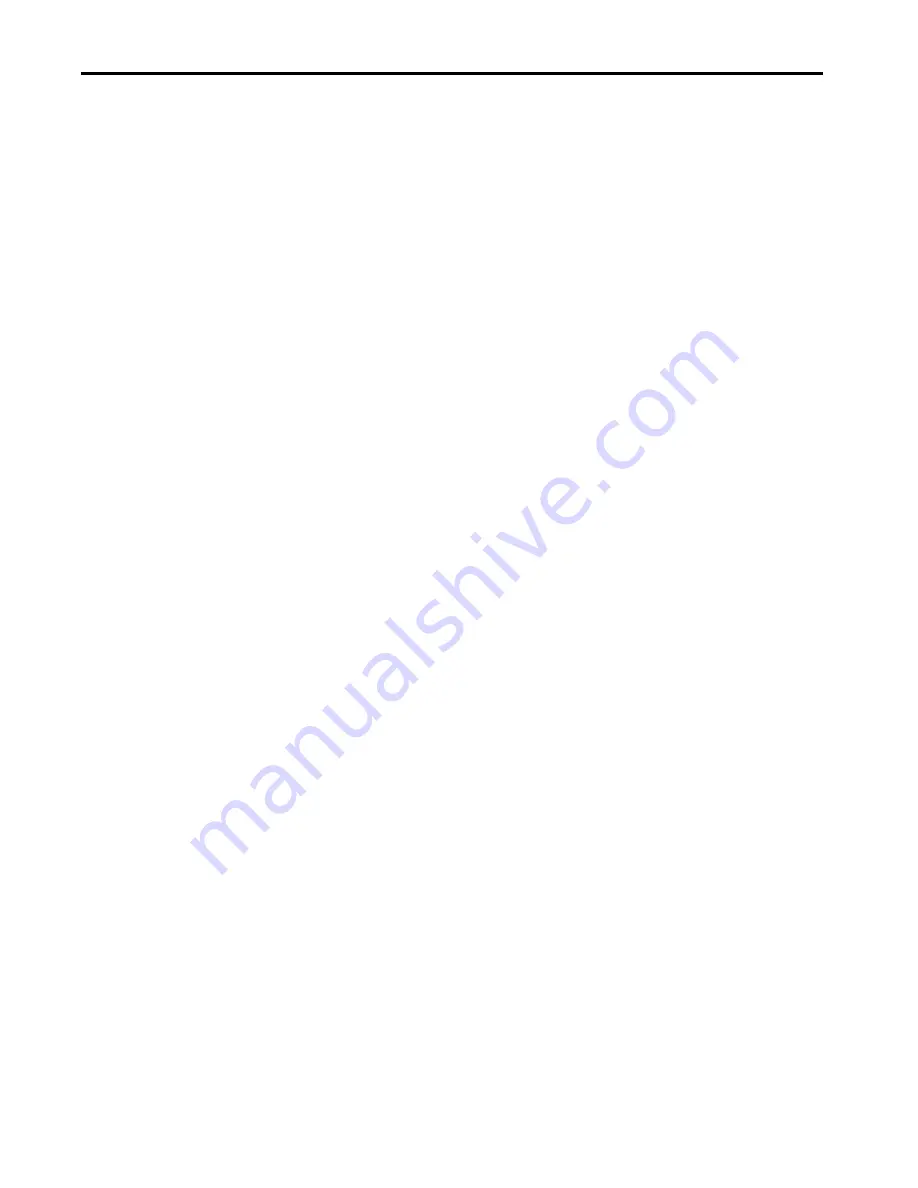
210
Rockwell Automation Publication 2198-UM004A-EN-P - October 2019
Chapter 10
Modes of Operation
The parameter ID140 (P1.030) is to set the range to detect the magnitude of
low-frequency vibration. When the frequency is not detected, it is probably
because the value of parameter ID140 (P1.030) is set too high and exceeds the
range. In this case, it is suggested to decrease the value of parameter ID140
(P1.030). If the value is too small, the system might regard noise as vibration
frequency. You can also use scope to observe the range of position error (pulse)
between upper and lower magnitude of the curve to adjust the value of parameter
ID140 (P1.030).
Manual Setting
There are two sets of low-frequency vibration suppression. One is parameters
ID135 and ID136 (P1.025 and P1.026), and the other is parameters ID137 and
ID138 (P1.027 and P1.028). These two sets of low-frequency vibration
suppression can be used to reduce two different frequency vibrations. Parameters
ID135 (P1.025) and ID137 (P1.027) are used to suppress the low-frequency
vibration. The function works only when the low-frequency vibration setting is
close to the real vibration frequency. Parameter P1.026 and P1.028 are used to set
the response after frequency filtering. The bigger the setting values of parameters
ID136 (P1.026) and ID138 (P1.028) are, the better the response is. However, if
the value is set too big, the motor might not operate smoothly. The default values
of parameters ID136 (P1.026) and ID138 (P1.028) are 0, which means the two
filters are disabled.
Speed Mode
This servo drive includes three types of command input: analog, register and I/O
mode. Analog command controls the motor speed by external voltage. Register
command controls the speed by two ways. One is to set different speed values in
three command registers and to switch the speed by using DI.SPD0 and
DI.SPD1 signals from the I/O connector. Another way is to change the value of
register by communication in I/O mode.
To deal with the problem of non-continuous speed when switching registers, an
S-curve acceleration/deceleration setting is provided. In a close-loop system, this
servo drive adopts gain adjustment and integrated PI controller and two modes
(manual and auto) for selection.
Manual mode is for manual parameter setting. In this mode, all auto or auxiliary
function will be disabled. The gain adjustment function provides different modes
for you to estimate load inertia and tune the bandwidth as well as responsiveness.
In addition, the parameter values set by you are regarded as the default.
Selection of Speed Command
There are two types of speed command source: analog voltage and internal
register (parameters). You can select the source by using the DI signal from the
I/O controller when the operating mode is S or Sz.
Содержание Kinetix 5100 2198-E1004-ERS
Страница 114: ...114 Rockwell Automation Publication 2198 UM004A EN P October 2019 Chapter 6 Set Up EtherNet IP Communication Notes ...
Страница 402: ...402 Rockwell Automation Publication 2198 UM004A EN P October 2019 Chapter 14 Absolute Position Recovery Notes ...
Страница 484: ...484 Rockwell Automation Publication 2198 UM004A EN P October 2019 Appendix C Use Add On Instructions Notes ...
Страница 488: ...488 Rockwell Automation Publication 2198 UM004A EN P October 2019 Appendix D Full Closed Loop Control Notes ...
Страница 499: ......