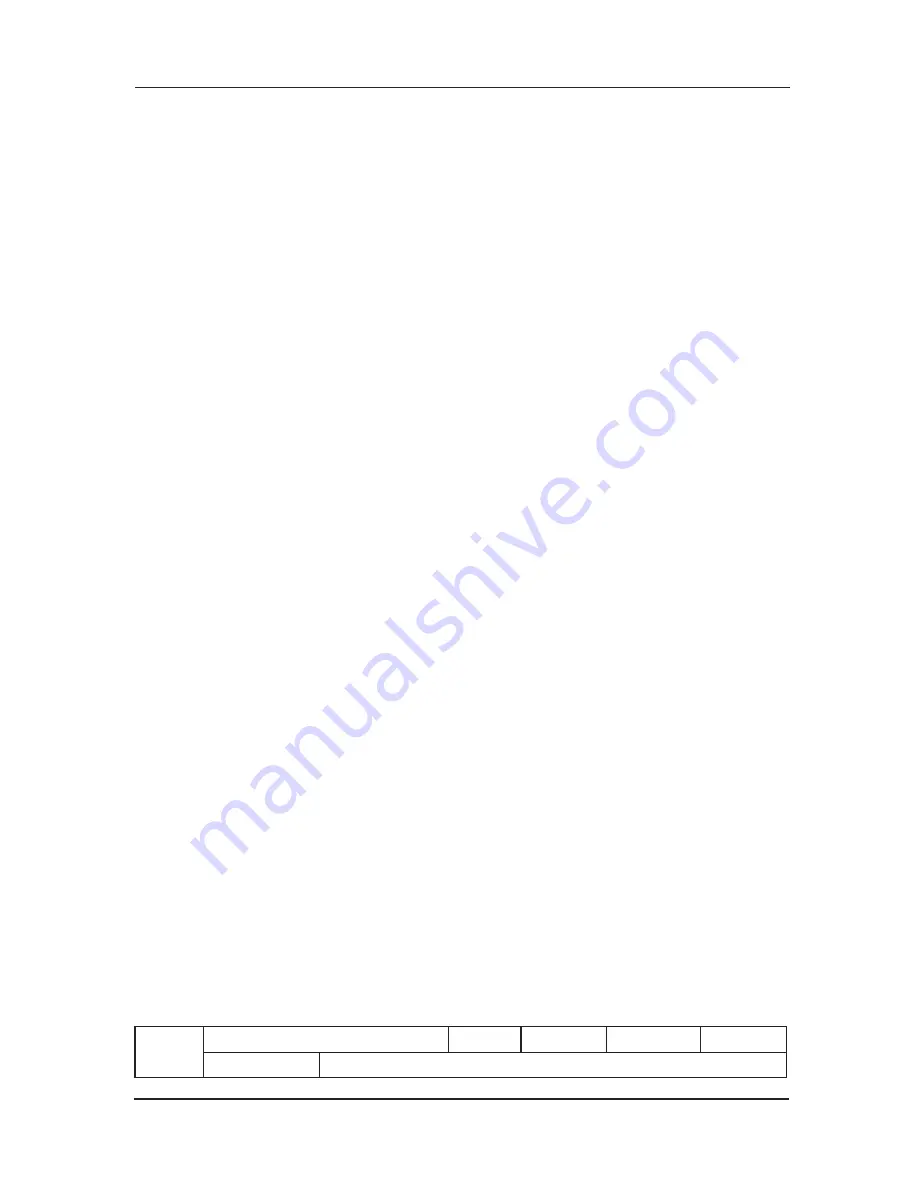
NICE3000 User Manual Function parameter description
109
If E21 alarms in the starting, check that whether the identification result parameters F1-06 and
F1-08 are correct t. If it
’
s ensured that the wiring of motor and PG card isn
’
t changed, you
can directly input the two data recorded after the first identification, or re-recognize the pulse
wheel encoder
’
s position angle.
Recommendation: Recognize the encoder
’
s position several times, compare with the data of
F1-06, if the error is without
±
5
°
, which indicates errors exist in the encoder or wiring.
Running trial
After the encoder
’
s position identification, do the running trials with no load (the traction
machine with no iron wires) before the recovery. The mode of running trial is recommended to
adopt inspection up and down buttons, at the moment, deal with the safety circuit and door lock
circuit according to the system condition. In the running trial course, the following two points
need specially care:
If the direction of the traction machine is corresponding to the reality (Up and Down), if not,
it needs to adjust the NICE 3000 wiring outputting to the motor, re-recognize the encoder
’
s
position.
Whether the traction machine
’
s forward and reversal running are stable and no noise;
because of no load in the traction machine, the current will be extremely small and NICE 3000
displays the current lower than 1A.
After the confirmation of the two points, NICE 3000 have recorded the traction machine
’
s
encoder position correctly into F1-06 (Users can record it down for the later using), and it can
do the normal control. The following step is adjusting according to the lift
’
s normal adjusting
course. Due to the different features of synchronous motor and asynchronous motor, user can
reduce the speed loop P1 gain of F2 group when in use.
Note: After the lift is using normally, adjust the motor wiring and encoder wiring will both cause
the lift can
’
t be normally used.
The usually used parameters:
Shaft parameter auto-tuning is used to record the position of shaft
’
s opening and closing
(Including leveling switch and force reducer switch). Requirements are as follows:
Encoder and leveling feedback is normal; the switch of the shaft is installed well.
The lift is in the ground floor, forced deceleration switch operation.
The lift is in examination and can check running.
The lowest and highest floors are set correctly.
NICE 3000 is not in the error alarming state.
Note: shaft auto-tuning can also be realized by the small keyboards on the main control panel.
Two floor auto-tuning needs the lift run under the first leveling which means there
’
s one
leveling sensor under the leveling plate..
F1-12
Encoder pulse number per rotation
Default
1024
Min. Unit
1
Setting Range
0
~
10000
Summary of Contents for MCTC-CTB-A
Page 12: ...Preface NICE3000 User Manual 12...
Page 15: ...Safety information and attention items 1...
Page 21: ...Product information 2...
Page 29: ...3 Structure of the control system and the component introduction...
Page 69: ...4 Installation and wiring...
Page 80: ...Installation and wiring NICE3000 User Manual 80...
Page 81: ...5 Function parameters tables...
Page 100: ...Function parameters tables NICE3000 User Manual 100...
Page 101: ...6 Function parameter description...
Page 153: ...7 System typical application and adjustment...
Page 172: ...System typical application and adjustment NICE3000 User Manual 172...