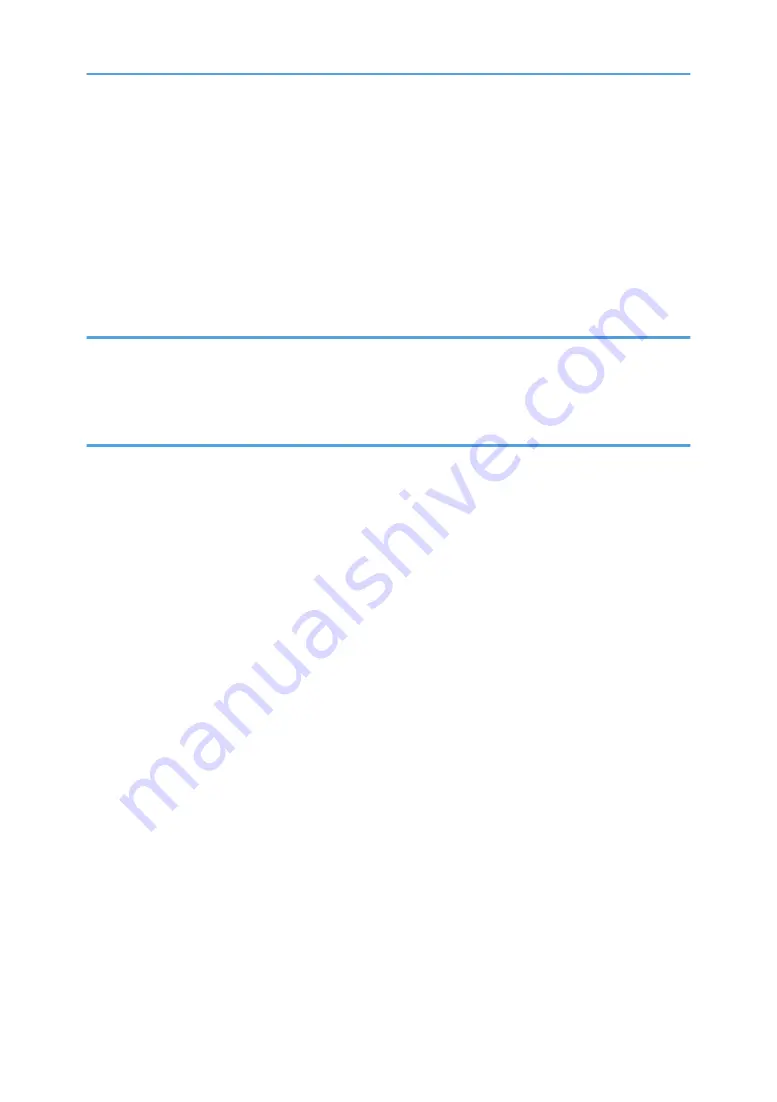
USB Host Interface Unit Type A (B819)..................................................................................................114
IEEE1284 B679........................................................................................................................................115
Gigabit Ethernet G874.............................................................................................................................116
Before You Begin.......................................................................................................................................118
Seal Check and Removal.........................................................................................................................118
DOS Unit Installation.................................................................................................................................119
Main Machine...........................................................................................................................................121
Optional Peripheral Devices....................................................................................................................125
General Cautions..........................................................................................................................................129
Drum...........................................................................................................................................................129
Drum Unit...................................................................................................................................................129
Transfer Belt Unit........................................................................................................................................130
Laser Unit....................................................................................................................................................130
Charge Corona.........................................................................................................................................130
Development..............................................................................................................................................131
Cleaning.....................................................................................................................................................131
Fusing Unit..................................................................................................................................................131
Paper Feed.................................................................................................................................................132
Used Toner.................................................................................................................................................132
Special Tools And Lubricants........................................................................................................................133
Special Tools..............................................................................................................................................133
Lubricants...................................................................................................................................................133
Operation Panel........................................................................................................................................134
Front Door..................................................................................................................................................135
Right Covers...............................................................................................................................................135
Left Covers..................................................................................................................................................136
Rear Covers...............................................................................................................................................137
Top Cover..................................................................................................................................................138
15
Summary of Contents for G148
Page 1: ...Model MT P2 Machine Code G148 SERVICE MANUAL 23 June 2006 Subject to change...
Page 52: ...10 Clamp 1 LCT B473 51 1...
Page 94: ...16 Set the hopper 13 in its holder Punch Unit B702 93 1...
Page 129: ...2 Preventive Maintenance 128 2...
Page 163: ...1 Open the front door 2 Pull out the internal dust filter A 3 Replacement and Adjustment 162 3...
Page 172: ...4 Development motor bracket D x 3 x 1 5 Development motor E x 4 Development Unit 171 3...
Page 237: ...3 Replacement and Adjustment 236 3...
Page 295: ...Install the paper feed unit 4 Troubleshooting 294 4...
Page 435: ...5 Service Tables 434 5...
Page 521: ...6 Details 520 6...