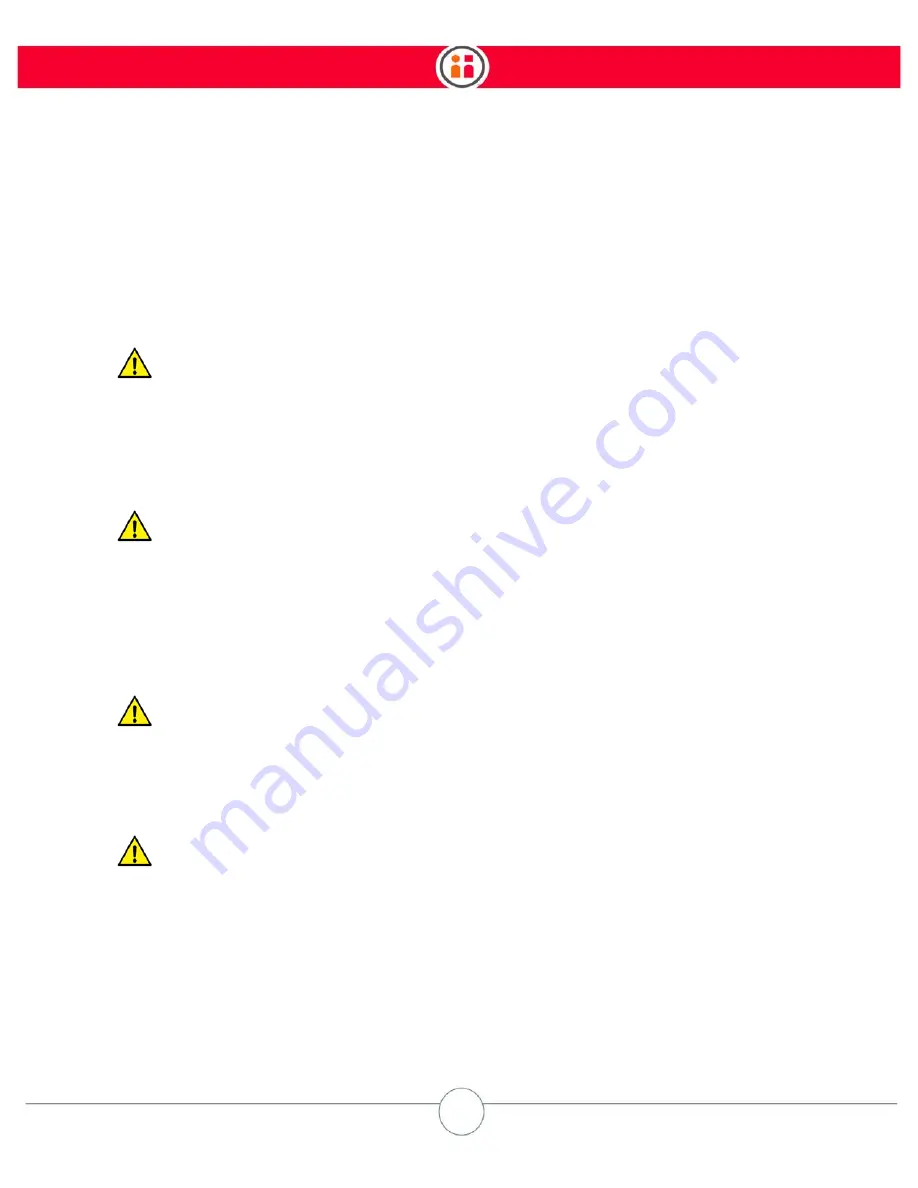
4
Intera 5.3
Welcome!
Intended use:
Sawyer is a collaborative robot intended for use in machine tending applications in manufacturing.
Warnings
Rethink Robotics’ collaborative robots are provided as partly completed machinery. The
robots are not supplied for specific applications. The integrator and/or end user is responsible for
ensuring that all appropriate regulations including but not limited to safety, electrical, and environ-
mental regulations are met for the appropriate regions or countries where the application will be
deployed.
The information provided with this robot and online does not cover how to design, fabricate,
install and commission a complete robotic application. If Rethink Robotics’ collaborative robots are
used to create a collaborative robotic workcell, the integrator and/or end user is responsible for
complying with the industrial robot safety standards relevant for the region where the robotic work-
cell will be deployed will apply. Examples of such standards are EN ISO 10218:2011, ANSI/RIA
R15.06:2012, CSA Z434:2014, and JIS B 8433:2015.
As part of complying with these standards, a risk assessment must be performed to identify
and eliminate, substitute or acceptably mitigate risk associated with hazards present in the applica-
tion. For more information see the relevant standards and associated documentation for your
region.
Note that it is possible to integrate and use Rethink Robotics’ collaborative robots in such a
way that presents an injury hazard if contact is made with a person. The integrator and/or end user
is responsible for evaluating the safety of the robotic application and determining and implementing
any risk reduction measures to eliminate, substitute or acceptably mitigate the risks associated with
the hazards. The integrator and/or end user assumes all responsibility for damage and/or harm
caused by use of the robot in a hazardous manner and agrees to indemnify Rethink Robotics from
all liability relating to such damage or harm.
Summary of Contents for Sawyer
Page 15: ...8 Intera 5 3 Getting to Know Sawyer Hardware Overview of Your Robot ...
Page 16: ...9 Intera 5 3 Getting to Know Sawyer Dimensions ...
Page 17: ...10 Intera 5 3 Getting to Know Sawyer Sawyer Reach ...
Page 93: ...86 Intera 5 3 Train Pick and Place Patterns on the Head 11 Press OK to go to the next step ...
Page 104: ...97 Intera 5 3 Train Pick and Place Patterns on the Head You may now run the task ...
Page 134: ...127 Intera 5 3 TCP IP The Set To node in the Behavior Editor is used to output information ...
Page 138: ...131 Intera 5 3 Fieldbus Devices 3 Using a keyboard navigate to CONFIGURATION and press ENTER ...
Page 155: ...148 Intera 5 3 ...
Page 156: ...149 Intera 5 3 ...
Page 180: ...173 Intera 5 3 ...
Page 190: ...183 Intera 5 3 Fixed Data 112 From Robot ...
Page 206: ...199 Intera 5 3 Small Assembly 114 From Robot 115 To Robot ...
Page 207: ...200 Intera 5 3 Large Assembly 116 From Robot 117 To Robot ...
Page 208: ...201 Intera 5 3 Floats 118 From Robot 119 To Robot ...
Page 209: ...202 Intera 5 3 Strings 120 From Robot 121 To Robot ...
Page 218: ...Z Zero G button 16 17 Zero G mode 24 Zero Gravity mode 17 zoom reset 42 ...
Page 219: ......
Page 220: ...Last updated June 18 2018 Intera 5 3 User Guide Getting Started Rev A ...