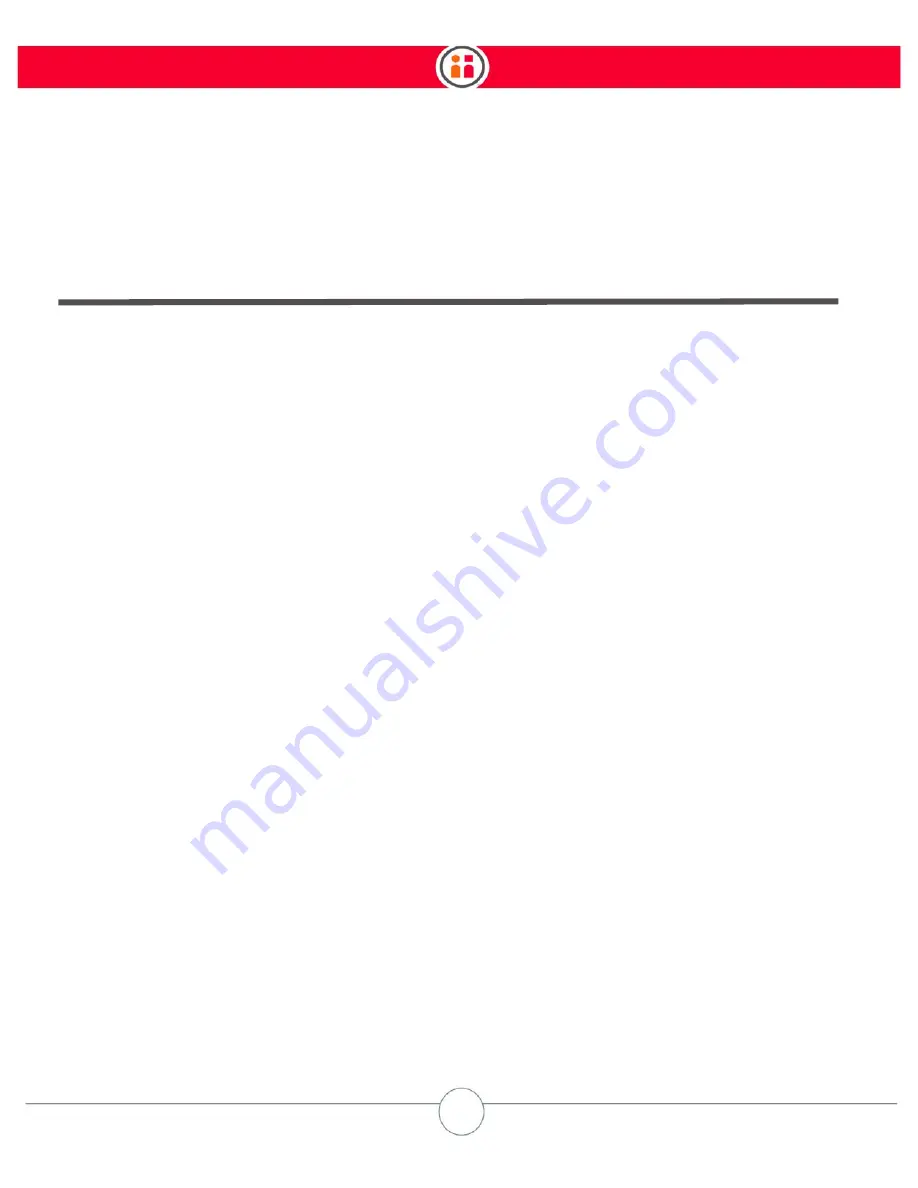
136
Intera 5.3
Sawyer and Safety
Also refer to the Banner Safety Controller documentation (SC26-2evm) and, for guidance on how to
perform risk assessments for collaborative robots applications, refer to ISO TS 15066:2016.
How these unique collaborative robots safely manage operational risks
Unlike typical industrial robots that operate behind safeguarding, Sawyer(TM), the collaborative
robot from Rethink Robotics, is designed to work effectively directly alongside people in a factory
setting, making it possible to deploy in environments which have historically been off-limits to
robotic automation. Rethink’s Collaborative Robots combine a number of unique technologies
designed to allow deployment without some of the traditional safeguarding described in ANSI, ISO,
or other safety standards, based on the application’s risk assessment. Sawyer(TM) is designed for:
•
Physical interaction between a worker and the robot.
•
Avoiding accidental contact.
•
Minimizing forces and stopping on human contact.
Rethink’s Collaborative Robots meet the requirements of a collaborative robot that is Power and
Force Limited by Inherent Design as described in ISO 10218-1: 2011, section 5.10.5. The most
recent edition of ISO 10218-1 does not include these power and force limiting collaborative
requirements, but instead points to the requirement in ISO 10218-2 requiring a risk assessment of
the entire robotic application, and refers readers to Technical Specification ISO TS 15066:2016 for
further guidance. ANSI RIA R15.06-2012 is a U.S.-national adoption of ISO 10218-1 & 2.
Rethink’s Collaborative Robot Safety Features
1. Safety by Design: Mechanical design and human-like cadence inherently reduces risks and
injuries.
•
Series Elastic Actuators (SEAs): Flexures at all joints provide passive compliance
to minimize the force of any contact or impact.
•
Smooth and Impact-Absorbing Surfaces: Sawyer has smooth, rounded arms
with padding in key areas, such as the elbows and wrists.
•
Backdrivable Joints: Sawyer has backdrivable joints allowing manual
repositioning of the arm and avoiding clamping hazards common with traditional
industrial robots, whether the arm actuators are powered up or not.
Summary of Contents for Sawyer
Page 15: ...8 Intera 5 3 Getting to Know Sawyer Hardware Overview of Your Robot ...
Page 16: ...9 Intera 5 3 Getting to Know Sawyer Dimensions ...
Page 17: ...10 Intera 5 3 Getting to Know Sawyer Sawyer Reach ...
Page 93: ...86 Intera 5 3 Train Pick and Place Patterns on the Head 11 Press OK to go to the next step ...
Page 104: ...97 Intera 5 3 Train Pick and Place Patterns on the Head You may now run the task ...
Page 134: ...127 Intera 5 3 TCP IP The Set To node in the Behavior Editor is used to output information ...
Page 138: ...131 Intera 5 3 Fieldbus Devices 3 Using a keyboard navigate to CONFIGURATION and press ENTER ...
Page 155: ...148 Intera 5 3 ...
Page 156: ...149 Intera 5 3 ...
Page 180: ...173 Intera 5 3 ...
Page 190: ...183 Intera 5 3 Fixed Data 112 From Robot ...
Page 206: ...199 Intera 5 3 Small Assembly 114 From Robot 115 To Robot ...
Page 207: ...200 Intera 5 3 Large Assembly 116 From Robot 117 To Robot ...
Page 208: ...201 Intera 5 3 Floats 118 From Robot 119 To Robot ...
Page 209: ...202 Intera 5 3 Strings 120 From Robot 121 To Robot ...
Page 218: ...Z Zero G button 16 17 Zero G mode 24 Zero Gravity mode 17 zoom reset 42 ...
Page 219: ......
Page 220: ...Last updated June 18 2018 Intera 5 3 User Guide Getting Started Rev A ...