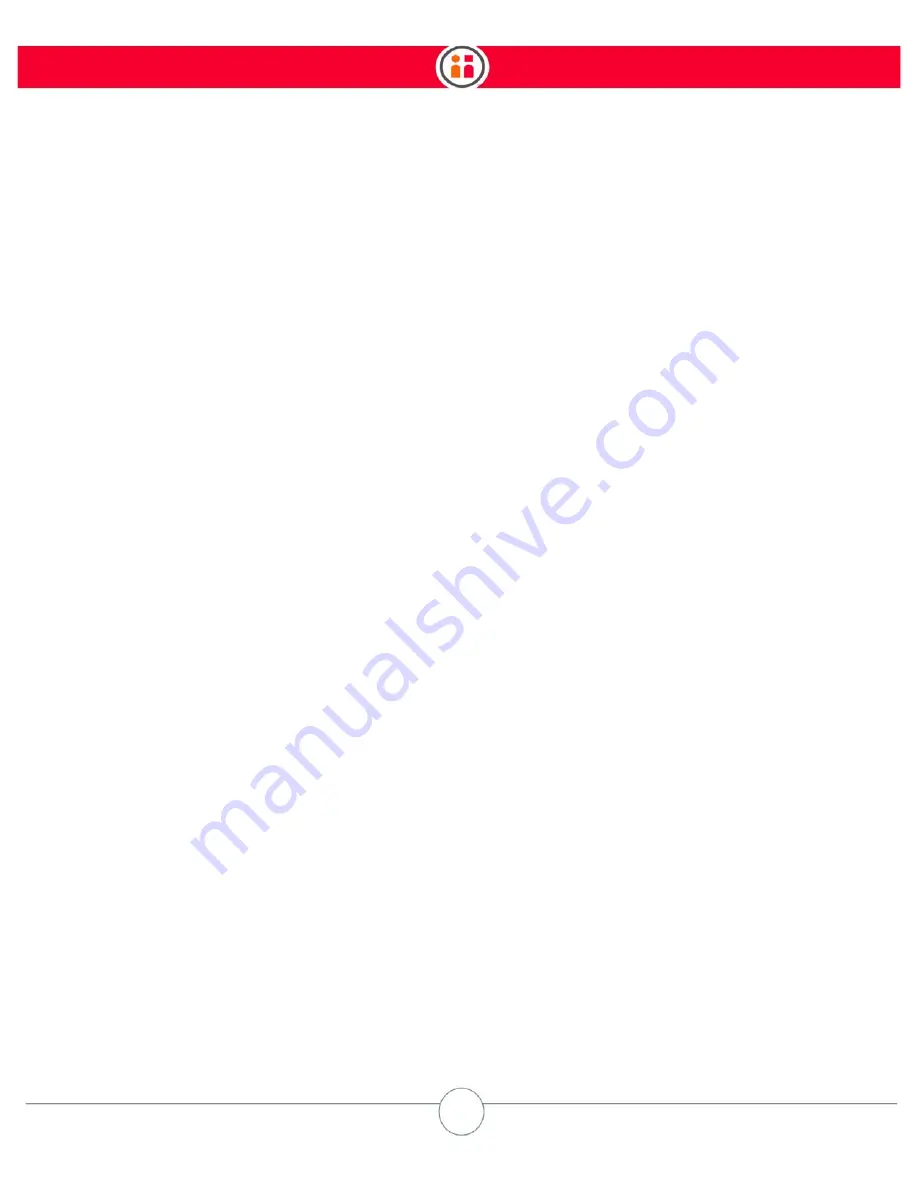
122
Intera 5.3
I/O Devices
SPECIFICATIONS
Safety
Category 4, PL e (EN ISO 13849)
SIL CL 3 (IEC 62061, IEC 61508)
Product Performance Standards
See Standards and Regulations section in the Instruction Manual for a list of industry applicable U.S. and international standards.
EMC
Meets or exceeds all EMC requirements in IEC 61131-2, IEC 62061 Annex E, Table E.1 (increased immunity levels), IEC 61326-1:2006,
and IEC61326-3-1:2008
Convertible I/O
·
Sourcing current: 80 mA maximum (overcurrent protected)
Test Pulse
·
Width: 200
μ
s max.
·
Rate: 200 ms typical
Certifications
·
Certification Pending
Removable Screw Terminals
·
Wire size: 24 to 12 AWG (0.2 to 3.31 mm²)
·
Wire strip length: 7 to 8 mm (0.275 in to 0.315 in)
·
Tightening torque: 0.565 N·m (5.0 in-lb)
Removable Clamp Terminals
·
Important: Clamp terminals are designed for 1 wire only. If more than 1 wire is connected to a terminal, a wire could loosen or
become completely disconnected from the terminal, causing a short.
·
Wire size: 24 to 16 AWG (0.20 to 1.31 mm²)
·
Wire strip length: 8.00 mm (0.315 in)
Safety Inputs (and Convertible I/O when used as inputs)
·
Input On threshold: > 15 V dc (guaranteed on), 30 V dc max.
·
Input Off threshold: < 5 V dc and < 2 mA, –3 V dc min.
·
Input On current: 5 mA typical at 24 V dc, 50 mA peak contact cleaning current at 24 V dc
·
Input lead resistance: 300
Ω
max. (150
Ω
per lead)
·
Input requirements for a 4-wire Safety Mat:
o
Max. capacity between plates: 0.22
μ
F
o
Max. capacity between bottom plate and ground: 0.22
μ
F
o
Max. resistance between the 2 input terminals of one plate: 20
Ω
Solid State Safety Outputs
0.5 A max. at 24 V dc (1.0 V dc max. drop), 1 A max. inrush
·
Output OFF threshold: 1.7 V dc typical (2.0 V dc max.)
·
Output leakage current: 50
μ
A max. with open 0 V
·
Load: 0.1
μ
F max., 1 H max., 10
Ω
max. per lead
Response and Recovery Times
·
Input to Output Response Time (Input Stop to Output Off): see the Configuration Summary in the PC Interface, as it can vary
·
Input Recover Time (Stop to Run):
·
Dependent on configuration
Summary of Contents for Sawyer
Page 15: ...8 Intera 5 3 Getting to Know Sawyer Hardware Overview of Your Robot ...
Page 16: ...9 Intera 5 3 Getting to Know Sawyer Dimensions ...
Page 17: ...10 Intera 5 3 Getting to Know Sawyer Sawyer Reach ...
Page 93: ...86 Intera 5 3 Train Pick and Place Patterns on the Head 11 Press OK to go to the next step ...
Page 104: ...97 Intera 5 3 Train Pick and Place Patterns on the Head You may now run the task ...
Page 134: ...127 Intera 5 3 TCP IP The Set To node in the Behavior Editor is used to output information ...
Page 138: ...131 Intera 5 3 Fieldbus Devices 3 Using a keyboard navigate to CONFIGURATION and press ENTER ...
Page 155: ...148 Intera 5 3 ...
Page 156: ...149 Intera 5 3 ...
Page 180: ...173 Intera 5 3 ...
Page 190: ...183 Intera 5 3 Fixed Data 112 From Robot ...
Page 206: ...199 Intera 5 3 Small Assembly 114 From Robot 115 To Robot ...
Page 207: ...200 Intera 5 3 Large Assembly 116 From Robot 117 To Robot ...
Page 208: ...201 Intera 5 3 Floats 118 From Robot 119 To Robot ...
Page 209: ...202 Intera 5 3 Strings 120 From Robot 121 To Robot ...
Page 218: ...Z Zero G button 16 17 Zero G mode 24 Zero Gravity mode 17 zoom reset 42 ...
Page 219: ......
Page 220: ...Last updated June 18 2018 Intera 5 3 User Guide Getting Started Rev A ...