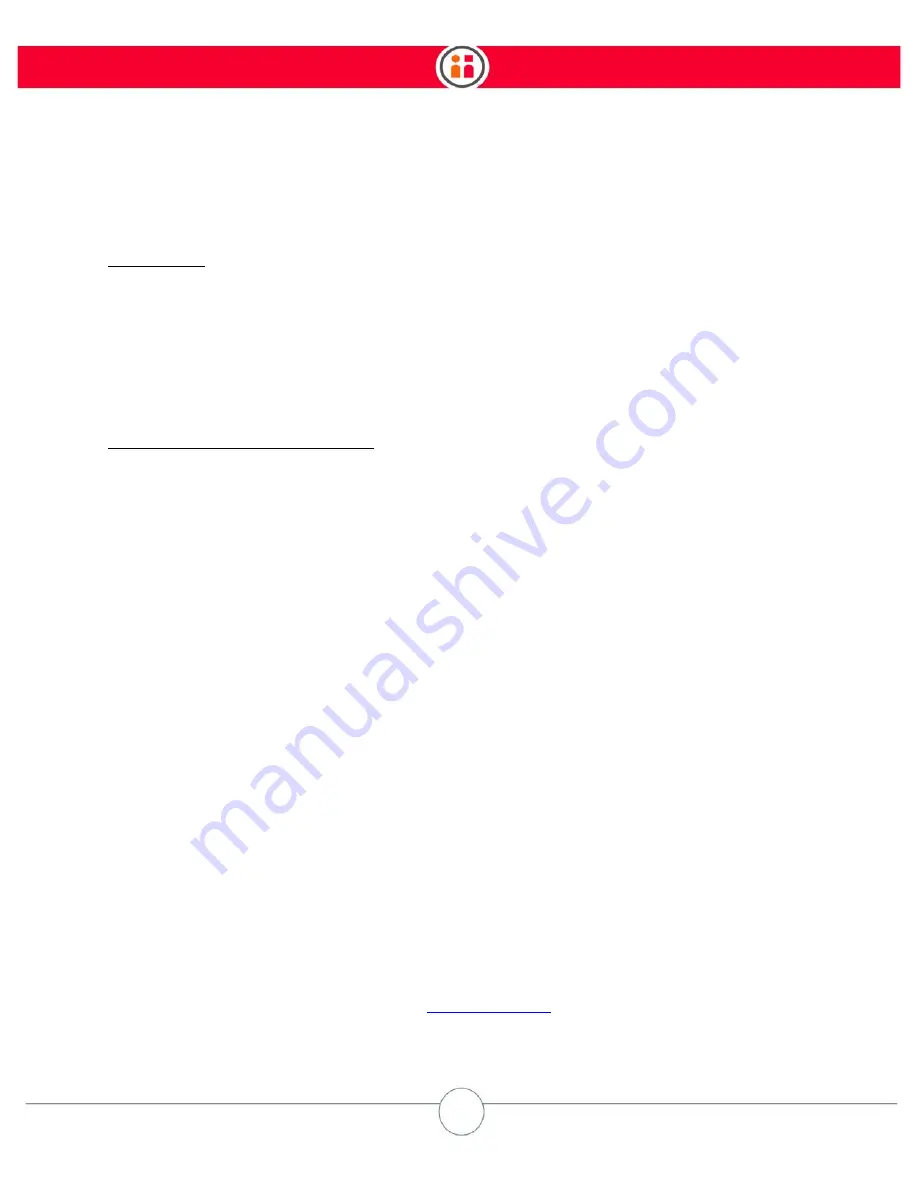
118
Intera 5.3
I/O Devices
configured as a Modbus Server (Slave) and communicate using Modbus TCP in order to
communicate with Sawyer.
Modbus TCP
INTERA is capable of communicating to external devices, configured as Slave Devices, with the
Modbus TCP Protocol. INTERA uses the FieldTalk Modbus Master library for modbus communica-
tions and is limited to discrete inputs and outputs using two modbus function codes, which are:
•
02 - Read Discrete Inputs (Read Input Status)
•
15 - Force Multiple Coils
Intera Lines and Modbus Addresses
The following information is for connecting to a device such as a PLC for Modbus communication.
Devices such as a Remote Terminal Unit (ex. Moxa E1212) may not need any further configuration
to work with the corresponding addresses. The Intera software uses lines for communicating with
external devices and these lines correspond to an address for communicating with Modbus
addresses. The Lines are 0 based, meaning that 8 configured lines on Sawyer correspond to lines
0-7. The corresponding Modbus addresses are 1 based, meaning that 8 configured lines on Sawyer
correspond to modbus addresses 1-8. (This is not a concern, however, because Intera Studio
abstracts away this problem by subtracting 1 from every line.)
The addressing below works with Modbus TCP devices that have addresses that are pre-config-
ured on the device. If a device needs to be configured to assign variables to specific addresses,
those addresses and variables must be configured on the device prior to configuring the device in
Intera.
NOTE: This a guideline for some but not all devices, please refer to device manufacturers’ docu-
mentation.
For further assistance with configuration of a device or Intera please contact the Rethink Robotics
Support Department at:
866-704-7400 (USA)
visit
Summary of Contents for Sawyer
Page 15: ...8 Intera 5 3 Getting to Know Sawyer Hardware Overview of Your Robot ...
Page 16: ...9 Intera 5 3 Getting to Know Sawyer Dimensions ...
Page 17: ...10 Intera 5 3 Getting to Know Sawyer Sawyer Reach ...
Page 93: ...86 Intera 5 3 Train Pick and Place Patterns on the Head 11 Press OK to go to the next step ...
Page 104: ...97 Intera 5 3 Train Pick and Place Patterns on the Head You may now run the task ...
Page 134: ...127 Intera 5 3 TCP IP The Set To node in the Behavior Editor is used to output information ...
Page 138: ...131 Intera 5 3 Fieldbus Devices 3 Using a keyboard navigate to CONFIGURATION and press ENTER ...
Page 155: ...148 Intera 5 3 ...
Page 156: ...149 Intera 5 3 ...
Page 180: ...173 Intera 5 3 ...
Page 190: ...183 Intera 5 3 Fixed Data 112 From Robot ...
Page 206: ...199 Intera 5 3 Small Assembly 114 From Robot 115 To Robot ...
Page 207: ...200 Intera 5 3 Large Assembly 116 From Robot 117 To Robot ...
Page 208: ...201 Intera 5 3 Floats 118 From Robot 119 To Robot ...
Page 209: ...202 Intera 5 3 Strings 120 From Robot 121 To Robot ...
Page 218: ...Z Zero G button 16 17 Zero G mode 24 Zero Gravity mode 17 zoom reset 42 ...
Page 219: ......
Page 220: ...Last updated June 18 2018 Intera 5 3 User Guide Getting Started Rev A ...