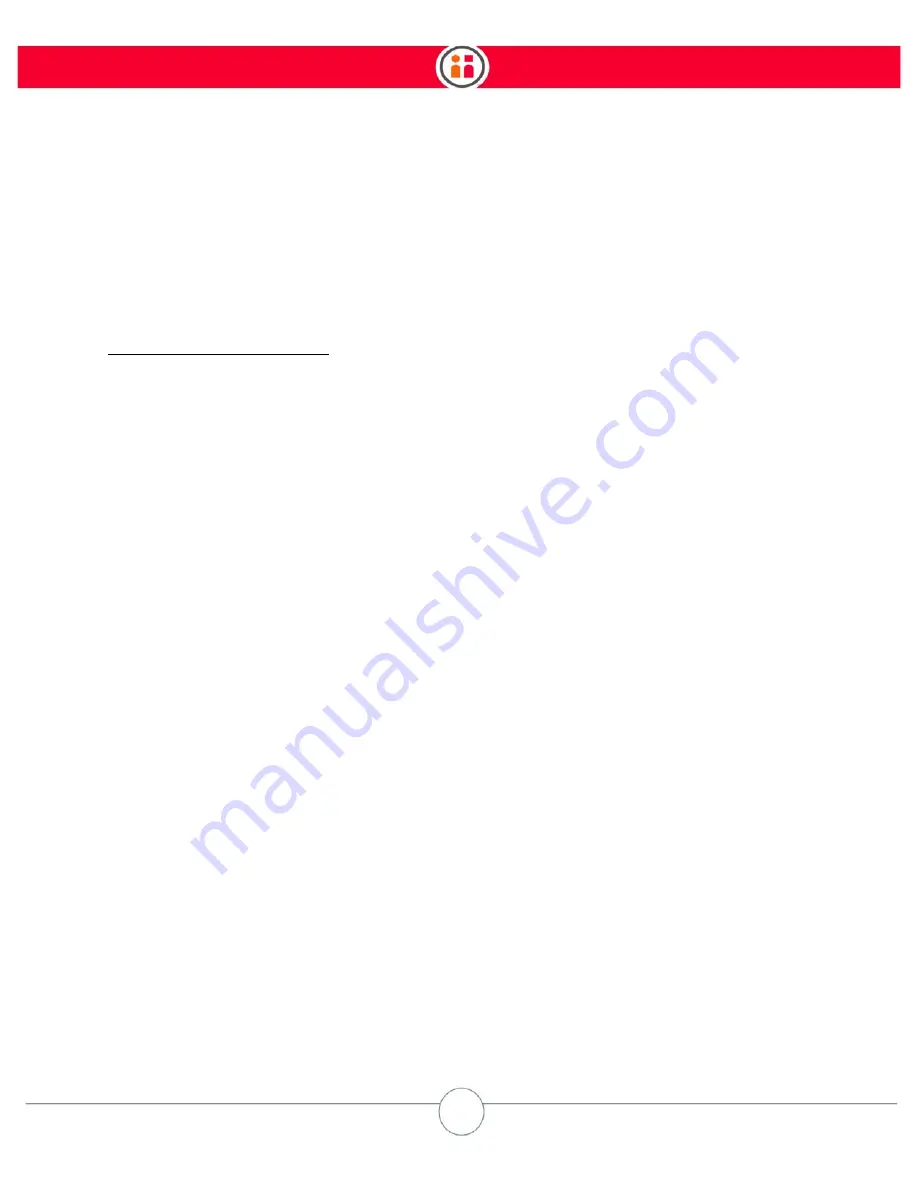
119
Intera 5.3
I/O Devices
The configured Modbus Device Lines/Modbus Addresses can be offset to achieve the necessary
address, by changing the Input and Output Base when configuring the Modbus Device.
With Intera 5, you can set the line numbers directly in the modbus device editor (shown above).
Intera 5 abstracts away the "mobus=1" issue, so if you want the lines 0, and 1024-1028,
you can use the literal string "0,1024-1028" to configure the lines in the software.
Networking and Configuration
Sawyer is configured for DHCP addressing by default. If Sawyer is not connected to a DHCP net-
work, the IP address will default to a link-local address.
NOTE: The link-local IP address range is 169.254.#.#, where "#" is any number between and includ-
ing 1 to 254. The subnet mask for link-local address is 255.255.0.0
If Sawyer is connected to a DHCP network, the IP address and subnet mask will be assigned to
reflect the connected network.
NOTE: Please check with your IT administrator if the IP address and subnet are not configured as
expected.
Safety Rated Controller
The Sawyer robot controller is supervised by a safety system comprised of a custom and preconfig-
ured Banner Safety Controller and associated wiring. The safety controller provides safety-rated E-
Stop functionality, and provides support for safety-rated safeguarding solutions for those applica-
tions that require them. The control systems monitors a variety of input devices such as e-stop but-
tons, safety mats, inter-locked guards, etc. and will limit or disconnect the voltage being supplied to
the robot motors.
Please refer to the Banner Safety Controller Instruction Manual for additional details on the ratings
and specifications of the safety controller: http://www.bannerengineering.com/
Summary of Contents for Sawyer
Page 15: ...8 Intera 5 3 Getting to Know Sawyer Hardware Overview of Your Robot ...
Page 16: ...9 Intera 5 3 Getting to Know Sawyer Dimensions ...
Page 17: ...10 Intera 5 3 Getting to Know Sawyer Sawyer Reach ...
Page 93: ...86 Intera 5 3 Train Pick and Place Patterns on the Head 11 Press OK to go to the next step ...
Page 104: ...97 Intera 5 3 Train Pick and Place Patterns on the Head You may now run the task ...
Page 134: ...127 Intera 5 3 TCP IP The Set To node in the Behavior Editor is used to output information ...
Page 138: ...131 Intera 5 3 Fieldbus Devices 3 Using a keyboard navigate to CONFIGURATION and press ENTER ...
Page 155: ...148 Intera 5 3 ...
Page 156: ...149 Intera 5 3 ...
Page 180: ...173 Intera 5 3 ...
Page 190: ...183 Intera 5 3 Fixed Data 112 From Robot ...
Page 206: ...199 Intera 5 3 Small Assembly 114 From Robot 115 To Robot ...
Page 207: ...200 Intera 5 3 Large Assembly 116 From Robot 117 To Robot ...
Page 208: ...201 Intera 5 3 Floats 118 From Robot 119 To Robot ...
Page 209: ...202 Intera 5 3 Strings 120 From Robot 121 To Robot ...
Page 218: ...Z Zero G button 16 17 Zero G mode 24 Zero Gravity mode 17 zoom reset 42 ...
Page 219: ......
Page 220: ...Last updated June 18 2018 Intera 5 3 User Guide Getting Started Rev A ...