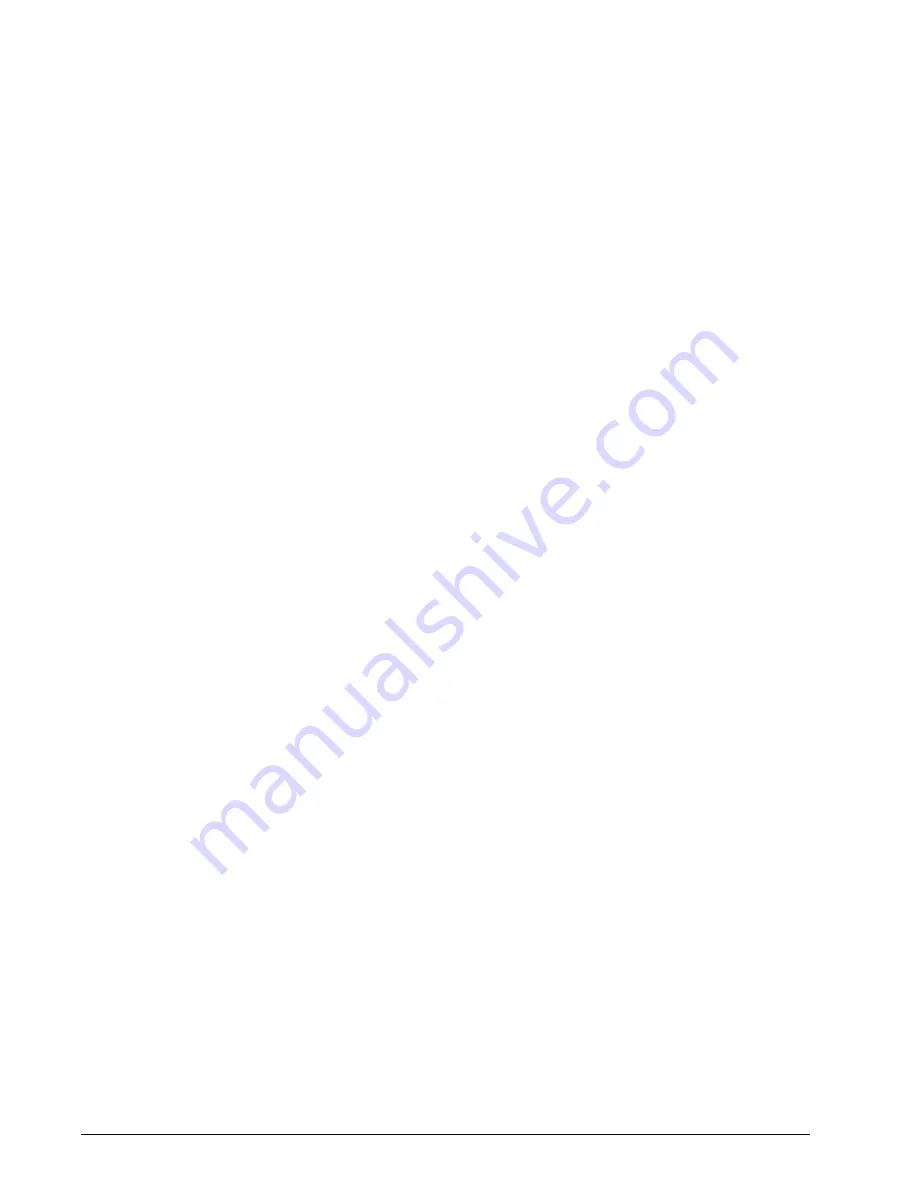
Chapter 7
7-4
Esprit® Ventilator Service Manual © Respironics, Inc.
REF 580-1000-02 G
Ventilator Communications
10. Touch the
Software
key on the ventilator screen.
11. Verify that the
Flash Version
is the same as the version on the Esprit
software CD-ROM.
IMPORTANT:
Reset the altitude and turn compliance off then back on
to reactivate compliance compensation
(use the User Configuration
Screen in diagnostic mode as described in Chapter 5).
12. Disconnect the serial cable from the ventilator.
13. Perform EST (Chapter 5).
Programming the
Ventilator Serial
Number
The serial number of each Esprit ventilator is stored in nonvolatile memory on
its CPU PCB, and must be reprogrammed if you replace the CPU PCB. There
are two ways to program the serial number:
•
You can program the serial number during a software download
(replacement CPU PCBs are shipped without Esprit software
installed).
•
You can program the serial number without downloading software (use
this method to save time if you’ve already downloaded software but
have not yet reprogrammed the serial number).
CAUTION:
Programming the ventilator serial number disables any installed options,
such as color or graphics. Be sure to program the serial number
before
enabling an option.
To program the serial number during a software download:
1. While turning the ventilator on, simultaneously press the two
Options
keys on the ventilator front panel for five seconds. The message
Looking for a download server
appears on the ventilator display, and
the backup alarm sounds.
2. With the Esprit software CD-ROM in the CD drive, click on
Start >
Run
, then enter
D:\setup.exe -vs
to begin a software download,
where
D
is the CD drive letter.
Enter the command exactly as shown, in lowercase letters with a space
between
exe
and
-vs
. (This is the same procedure as described in
section 7.1, except that you enter the above command rather than
double-clicking on SETUP.EXE.)
3. At the end of the download, a dialog box prompts you to enter the
ventilator serial number. Enter the serial number (
VSxxxxxxx
) after the
ventilator has restarted in diagnostic mode, where
xxxxxxx
is the
seven-digit ventilator serial number. Enter
VS
in uppercase letters.