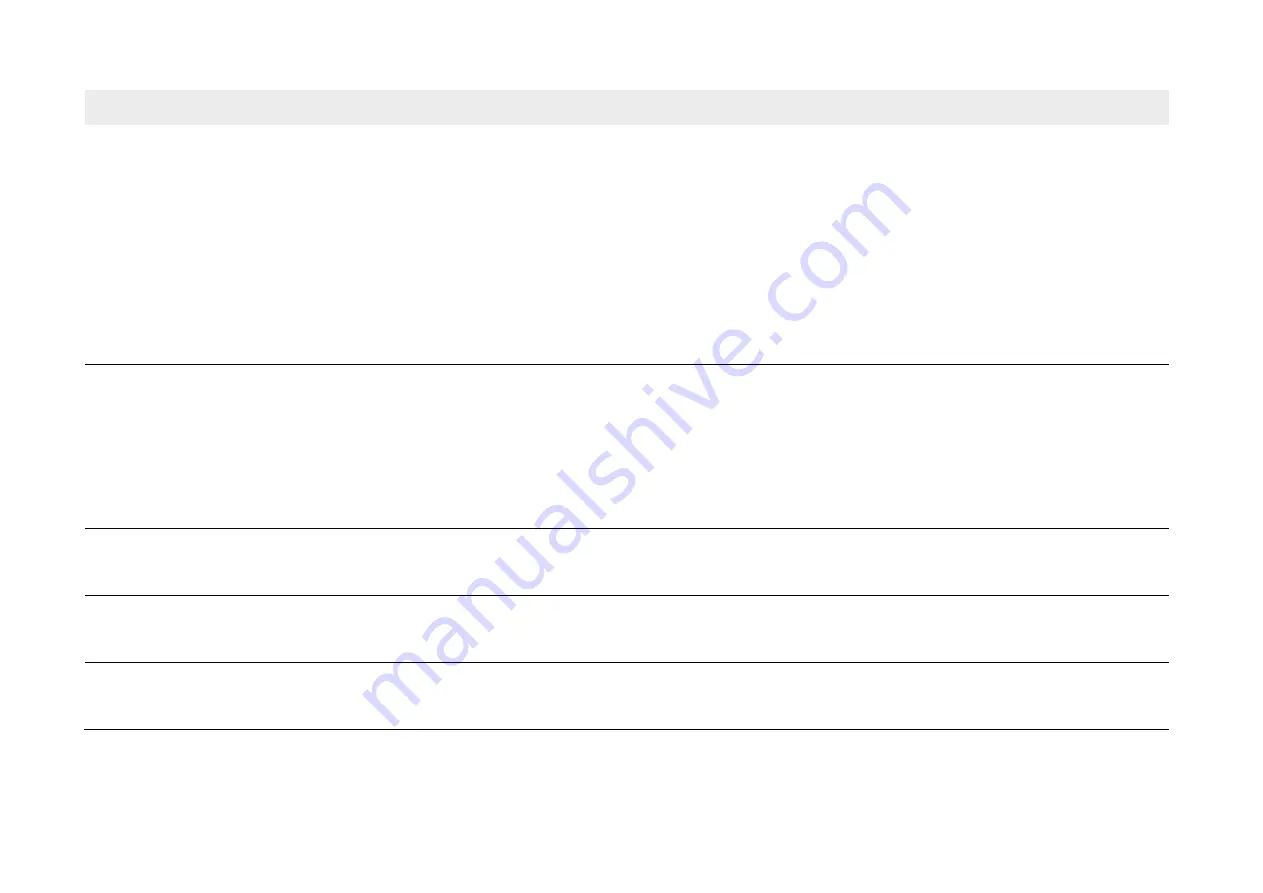
Programming
D-123
890CS Common Bus Supply - Frames B & D; 890CD Common Bus Drive and 890SD Standalone Drive - Frames E & F
Parameter Descriptions
* OUTPUT GBOX OUT
PREF: 158.26
Default: 1
Range: -2000000000 to
+2000000000
OUTPUT GBOX IN and OUTPUT GBOX OUT together define the gearbox ratio between the motor and the load. For
example, if a 3:2 gearbox is fitted between the motor and the load such that the motor turns through 3 revolutions for every 2
revolutions of the load, then set OUTPUT GBOX IN to 3, and set OUTPUT GBOX OUT to 2. The software will then keep
track of the load position.
If the power is removed and then reapplied, it is possible for the drive to keep track of the load position even if the shaft has
moved since the power was removed. This is only possible if the encoder is an absolute multi-turn. Otherwise, the load
position will be set equal to the motor position on power-up.
ENCODER MECH O/S
PREF: 158.06
Default: 0.0000 deg
Range: 0.0000 to
360.0000 deg
(Encoder mechanical offset). When using an absolute encoder, the SHAFT POSITION diagnostic shows the absolute position
of the input encoder. The zero position can be adjusted by setting ENCODER MECH O/S. Locate the position which is
required to be zero, and note the value of SHAFT POSITION. Enter this value into ENCODER MECH O/S to zero its
position.
ENCODER FEEDBACK
PREF: 158.30
Default: 0.00
Range: —.xx RPM
This parameter shows the mechanical speed of the motor shaft, calculated from the encoder feedback, in RPM.
SHAFT POSITION
PREF: 158.09
Default: —.xx deg
Range: —.xx deg
This diagnostic provides the motor shaft position (before the gear box).
* LOAD POSITION
PREF: 158.10
Default: —.xx deg
Range: —.xx deg
This diagnostic provides the motor load position (after the gear box).