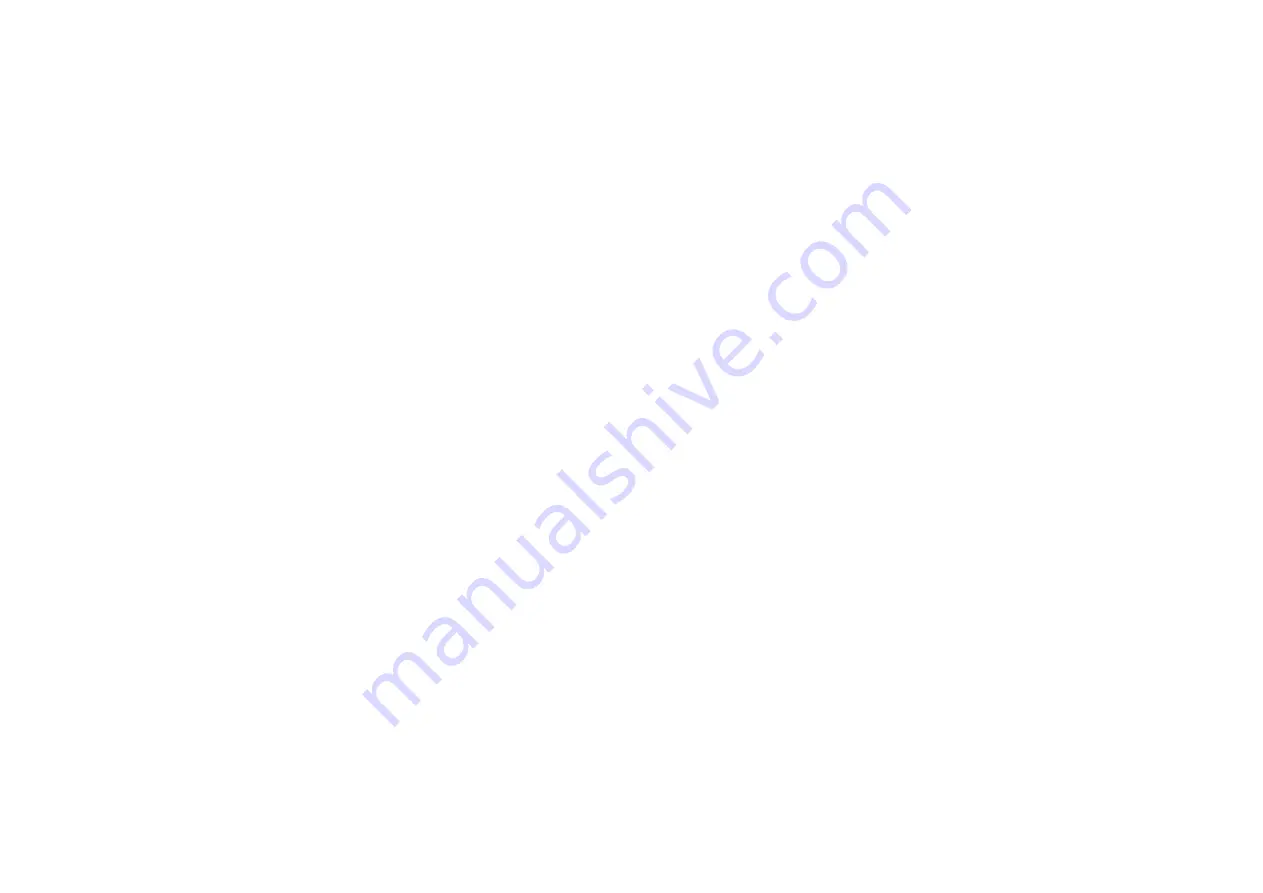
Operating the Drive
8-22
890CS Common Bus Supply - Frames B & D; 890CD Common Bus Drive and 890SD Standalone Drive - Frames E & F
8
9
10
11
A
B
C
D
1
2
3
4
5
6
E
High Starting Torque
Applications requiring high motor starting torque (greater than 100% of rated torque) need careful setup of
the drive voltage boost feature. For most motors, a FIXED BOOST parameter (FLUXING function block)
setting of 6.0% is usually adequate. Setting the FIXED BOOST parameter level too high can cause the
drive current limit feature to operate. If this occurs, the drive will be unable to ramp up in frequency. The IT
LIMITING diagnostic (INVERSE TIME function block) will indicate TRUE when the inverse time current
limit feature is operating. Simply reducing the level of the FIXED BOOST parameter will remove this
problem. It is important to use the minimum level of FIXED BOOST necessary to accelerate the load.
Using a level of FIXED BOOST higher than necessary will lead to increased motor heating and increased
risk of drive overload.
Note
Motor torques greater than 100% require high currents to be drawn from the drive. Thus, the
CURRENT LIMIT parameter (CURRENT LIMIT function block) will have to be set accordingly such
that the drive current limit feature will not activate when accelerating the load.
The best motor starting performance can be achieved by setting up the SLIP COMP function block, refer to
the Appendix D: “Programming” - SLIP COMP. Also setting the BASE VOLTS parameter (VOLTAGE
CONTROL function block) to 115.4% and the FREQ SELECT parameter (PATTERN GEN function
block) to 3kHz, can help to start difficult loads in the most extreme cases.