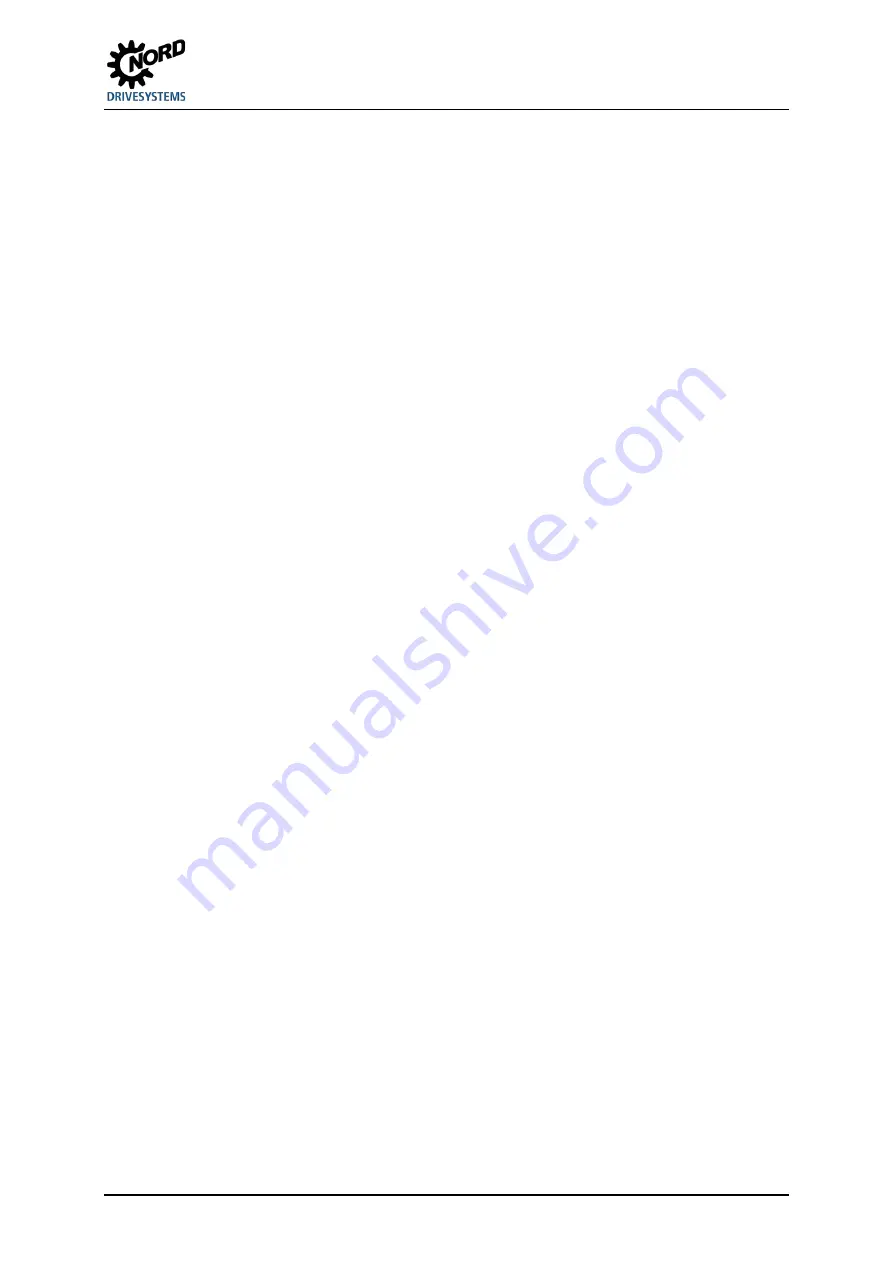
5 Parameter
BU 0180 en-4118
115
13 = Current limit
,
"Current limited"
depends on parameter (P536). This value corresponds to
100% of the setpoint value. When the set limit value is reached, the output voltage is
reduced in order to limit the output current.
14 = Current switch-off
,
"Current limit switch
-
off",
depends on parameter (P536), this value
corresponds to 100% of the setpoint value. When the set limit value is reached, the
device switches off with error code E12.4.
15 = Ramp time
, normally only used in combination with a potentiometer.
Lower limit: 50 ms
Standardisation: T_Rampenzeit= 10s * U[V] / 10V (U=Potentiometer voltage)
16 = Torque precontrol
, a function that enables a value for the anticipated torque requirement
to be entered in the controller (interference factor switching). This function can be used to
improve the load take-up of lifting equipment with separate load detection.
17 = Multiplication
, the setpoint is multiplied with the analogue value supplied. The analogue
value adjusted to 100% then corresponds to a multiplication factor of 1.
18 = Curve travel calculator
, via the external analogue input (P400 [-03] or P400 [-04]) or via
the BUS (P546 [-01 .. -03]) the master receives the actual speed from the slave. From its
own speed, the slave speed and the guide speed, the master calculates the actual
setpoint speed, so that neither of the two drives travels faster than the guide speed in the
curve.
19 =
…reserved
25 = Transfer Factor Gearing
,
"Gearing Transfer Factor"
, is a multiplier to compensate for the
variable transfer of a setpoint value. E.g.: Setting of the transformation between the
master and the slave by means of a potentiometer.
26 =
…reserved
30 = Motor temperature
: enables measurement of the motor temperature with a
KTY-84 temperature sensor (
Section
)
33 = Setpoint Torque Proc. cntrl.
,
"Setpoint torque process controller",
for even distribution
of the torques to coupled drive units (e.g.: S-roller drive). This function is also possible
with the use of ISD control.
34 = d-correction F process
- (diameter correction, frequency PI / process controller).
35 = d-correction Torque
-
(diameter correction, torque).
36 = d-correction F + Torque
- (diameter correction, frequency for PI / process controller and
torque)
*) For further details of the PI and process controller, please refer to Section 8.2 "Process
controller".
**) The limits of these values are formed by the parameters >minimum frequency auxiliary
setpoint values< (P410) and the parameter >maximum frequency auxiliary setpoint values<
(P411), whereby the limits defined by (P104) and (P105) cannot be undershot or overshot.
Summary of Contents for SK 180E Series
Page 1: ...BU 0180 en NORDAC BASE SK 180E SK 190E Users Manual for Frequency Inverters...
Page 4: ...NORDAC BASE SK 180E SK 190E Users Manual for Frequency Inverters 4 BU 0180 en 4118...
Page 185: ...8 Additional information BU 0180 en 4118 185 8 3 4 EU Declaration of Conformity...
Page 211: ...Key word index BU 0180 en 4118 211...
Page 212: ...6071802 4118...